The W beam guardrail cold bending machine plays a pivotal role in the road safety industry, shaping infrastructure that is both durable and effective. This machinery is critical for producing the W beam guardrail components, which line countless roadways across the globe, protecting vehicles from hazards. Delving deep into the nuances of this machine offers insight into its indispensability in modern road construction and safety measures.
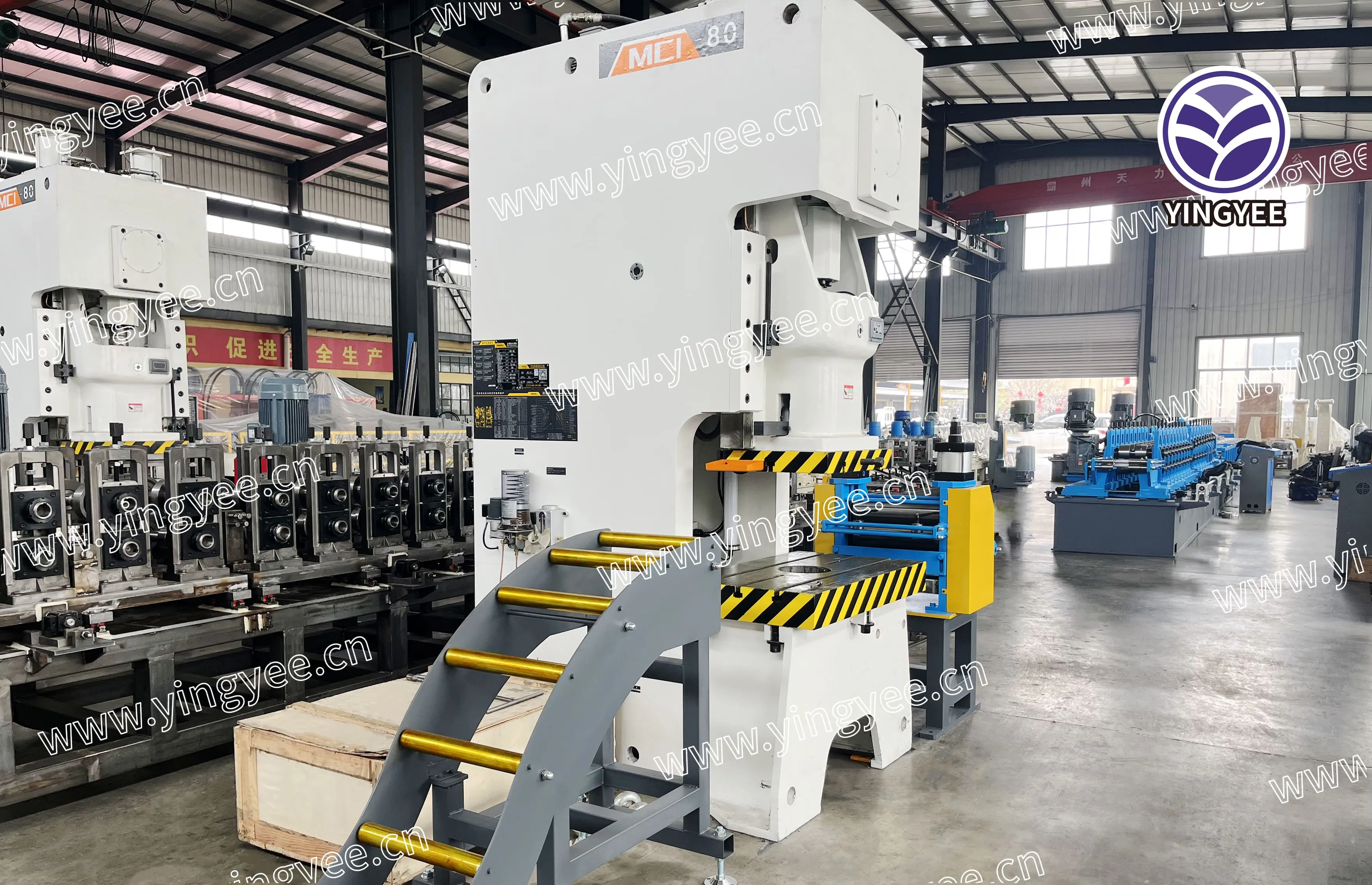
The Evolution of W Beam Guardrail Cold Bending Machines
The W beam guardrail has been a staple in road safety for decades. Its unique design, resembling a W, is engineered to absorb impact, thereby minimizing the extent of damage during vehicular accidents. To achieve its specific shape, manufacturers rely on cold bending machines, which have evolved significantly over the years.
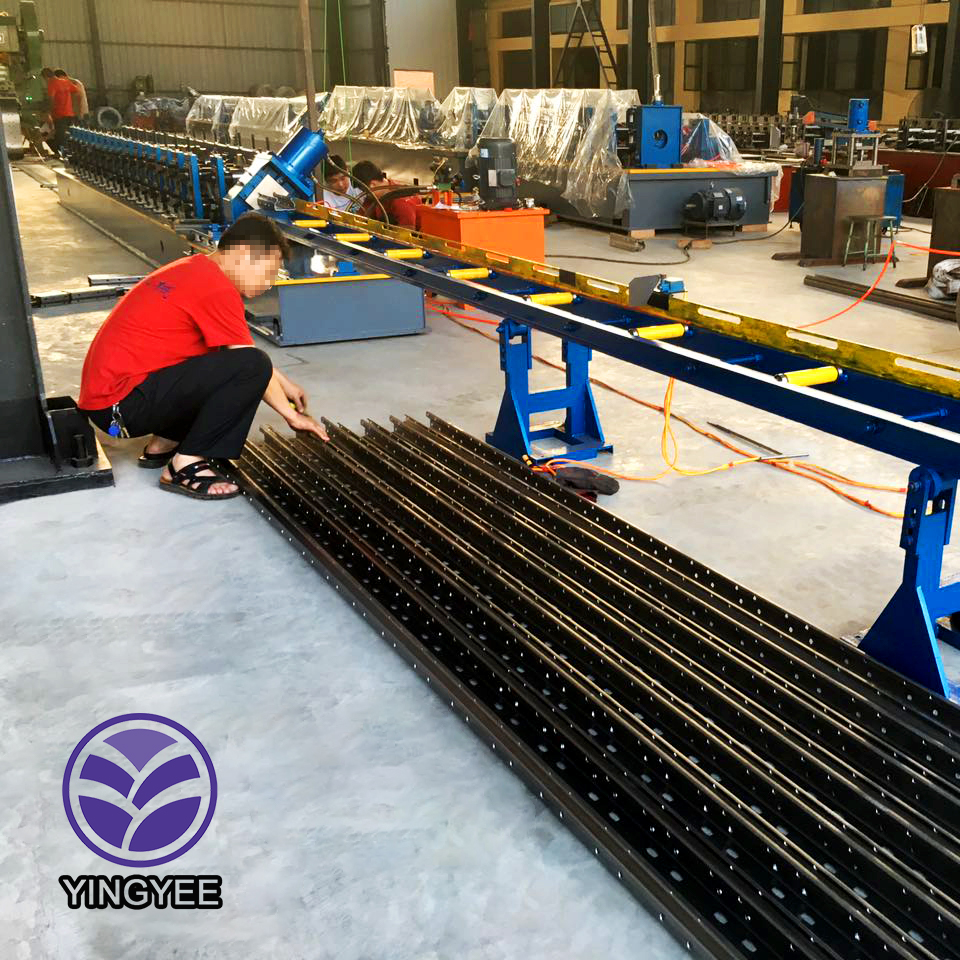
Initially, producing W beam guardrails involved labor-intensive processes that were slow and prone to inaccuracies. With the advent of specialized cold bending machines, production has become more streamlined, precise, and efficient. These machines use advanced technologies, such as CNC systems, to ensure each beam is bent to exact specifications.
Key Features that Define Modern Cold Bending Machines
Modern W beam guardrail cold bending machines are characterized by several innovative features that enhance their performance and reliability. These include
1. Precision Engineering These machines are equipped with state-of-the-art controls that ensure precise bending angles and curvature. This precision is crucial for maintaining the structural integrity of the guardrails.
2. Automated Systems Automation has revolutionized the production process. With integrated systems, these machines can operate continuously with minimal human intervention, reducing labor costs and increasing output.
3. Versatility Advanced machines can handle various materials and thicknesses, accommodating different specifications required for various road projects.
4. Energy Efficiency As sustainability becomes a pressing concern, these machines are designed to minimize energy consumption without compromising on output quality.
5. Safety Protocols Built-in safety features protect operators from potential hazards, ensuring a safer working environment.
Real-world Applications and Benefits
w beam guardrail cold bending machine
The deployment of W beam guardrail cold bending machines transcends mere production. Their impact is felt in several critical areas
1. Enhanced Road Safety By producing guardrails that meet rigorous safety standards, these machines contribute to safer road environments. The precision bending ensures that guardrails can perform effectively during collisions, safeguarding lives.
2. Cost-effectiveness The efficiency of modern machines translates to lower production costs. Manufacturers can produce high-quality guardrails in large quantities without incurring exorbitant expenses, making infrastructure development more affordable.
3. Rapid Deployment In emergency situations where roads are damaged or new roads need swift construction, these machines enable rapid production of guardrails, ensuring timely completion of projects.
4. Customization Options Depending on the geographical challenges or specific road layouts, cold bending machines can produce customized guardrails that perfectly fit the required dimensions and specifications.
Expert Insights into Choosing the Right Machine
Selecting the right W beam guardrail cold bending machine is crucial for optimal performance. Industry experts emphasize the importance of
- Researching Manufacturers Opt for machines from reputable manufacturers known for their quality and after-sales service. This ensures long-term reliability and support.
- Evaluating Technological Advancements As technology rapidly evolves, investing in a machine with the latest features and capabilities can significantly enhance production efficiency.
- Considering Longevity and Maintenance Machines with robust construction and easy maintenance protocols guarantee a longer lifespan and reduced downtime.
- Prioritizing User Interface and Training Machines that offer intuitive interfaces and comprehensive training resources enable operators to utilize their full potential effectively.
The Future of W Beam Guardrail Cold Bending Machines
As infrastructure demands grow and technology advances, the future of W beam guardrail cold bending machines is promising. Emerging technologies such as AI and IoT are set to further automate and optimize production processes, offering unprecedented levels of precision and efficiency.
Investments in research and development will likely lead to the creation of even more sophisticated machines, capable of producing eco-friendly materials without compromising on strength or durability. Moreover, as global safety standards rise, these machines will continue to evolve to meet new criteria, ensuring that road safety infrastructure remains robust and reliable.
In conclusion,
the W beam guardrail cold bending machine is an essential asset in the road safety domain. Its evolution reflects significant advancements in technology and methodology, underscoring the continual pursuit of safer and more efficient infrastructure solutions worldwide. By prioritizing quality, innovation, and safety, these machines stand as testaments to engineering excellence and commitment to public safety.