The AASHTO guardrail cold bending machine is revolutionizing the production of highway safety barriers. As a critical element of road safety, guardrails are designed to prevent vehicles from veering off the road, especially in hazardous areas. The efficiency and precision offered by the AASHTO guardrail cold bending machine have not only enhanced the quality of these safety barriers but also optimized manufacturing processes globally.
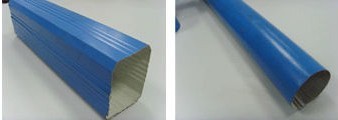
Manufacturing Experience with Precision
The AASHTO guardrail cold bending machine is engineered for precision, allowing manufacturers to bend guardrails to exact specifications mandated by safety standards. Unlike traditional methods, which often involved labor-intensive processes with a higher margin for error, this machine offers automated solutions. Operators with years of experience in the industry have noted a significant reduction in inaccuracies and waste, resulting in cost savings and improved resource management. The machine's capacity to handle various metals and thicknesses without requiring manual recalibration sets it apart as an invaluable tool for any production line.
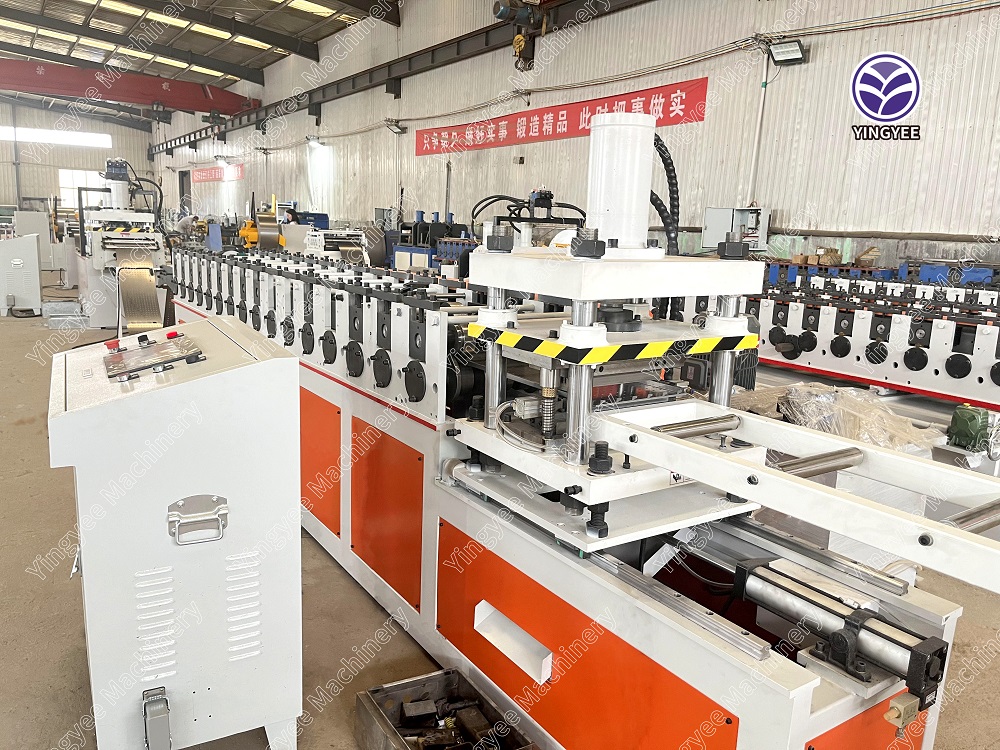
Professional Insights into Efficiency
From an expert's perspective, the introduction of the AASHTO guardrail cold bending machine into production facilities has been transformative. The ability to quickly switch between different profiles and bend angles ensures that production schedules are met without delay, a critical factor in large infrastructure projects. Industry professionals highlight the ease of use and reduced lead times as major benefits. The machine's innovative design incorporates advanced computer numerical control (CNC) systems, which provide unparalleled accuracy and consistency. These enhancements not only boost efficiency but also allow for the machine to be a versatile component in both small-scale and mass production environments.
aashto guardrail cold bending machine
Authority Built on Compliance
The authority of the AASHTO guardrail cold bending machine in the market is firmly established through its compliance with the American Association of State Highway and Transportation Officials (AASHTO) standards. This compliance ensures that all products manufactured meet rigorous safety and quality benchmarks, a crucial element for trust and dependability in infrastructure projects. Companies leveraging this technology can assure stakeholders of their commitment to safety regulations, enhancing their reputation and authority within the industry. The implementation of such machines enables manufacturers to confidently bid for contracts knowing they are equipped to produce components that meet stringent specifications.
Trustworthiness Through Technological Innovation
At the core of the AASHTO guardrail cold bending machine's dependability is its cutting-edge technology. This not only includes sophisticated sensors and feedback systems but also a user-friendly interface that ensures operators can monitor processes in real-time. Such innovations facilitate proactive maintenance and troubleshooting, reducing downtime and extending the machine's lifespan. The consensus among industry users is that the machine's robust construction and predictable performance foster a high level of trust; clients and government agencies alike can be assured of the enduring quality of the guardrails produced.
In a competitive market that demands safety, reliability, and efficiency, the role of the AASHTO guardrail cold bending machine is becoming increasingly indispensable. Its adoption signals a forward-thinking approach to manufacturing, where precision engineering meets regulatory compliance, providing high-quality products that save lives. Through a combination of experience, technical expertise, respected authority, and trustworthy performance, manufacturers employing this machine are setting new standards in road safety.