For businesses in construction and manufacturing, selecting the right machinery is crucial for operational efficiency and product quality. Among these machines, the stud making machine stands out as an indispensable asset. With a rich history and evolving technological relevance, this piece of equipment is a testament to engineering advancements and industry needs.
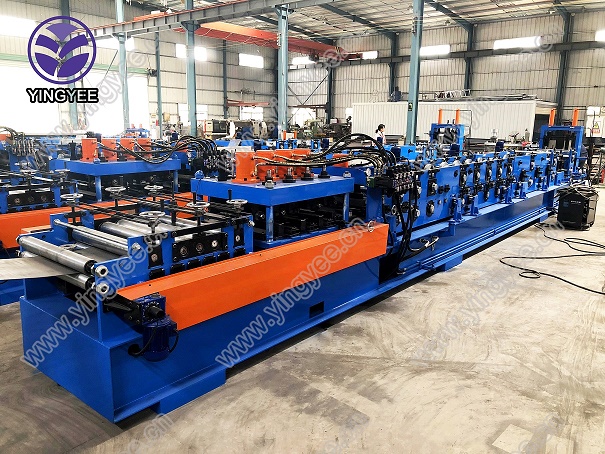
Stud making machines are designed for precision and versatility, producing metal studs that are pivotal in framing and securing structures, especially in fields like construction and automotive manufacturing. These machines transform raw materials, typically steel, into durable and reliable studs essential for industrial projects.
Expertise in operating a stud making machine begins with understanding its core components and their interactions. The primary elements typically include the decoiler, feeder, straightener, punch press, and cutting system. Each of these parts plays an integral role the decoiler holds and uncoils the steel, the feeder ensures precise feed into the machine, the straightener aligns the material to prevent deformities, the punch press shapes and forms the studs, and finally, the cutting system segments the finished product with precision.
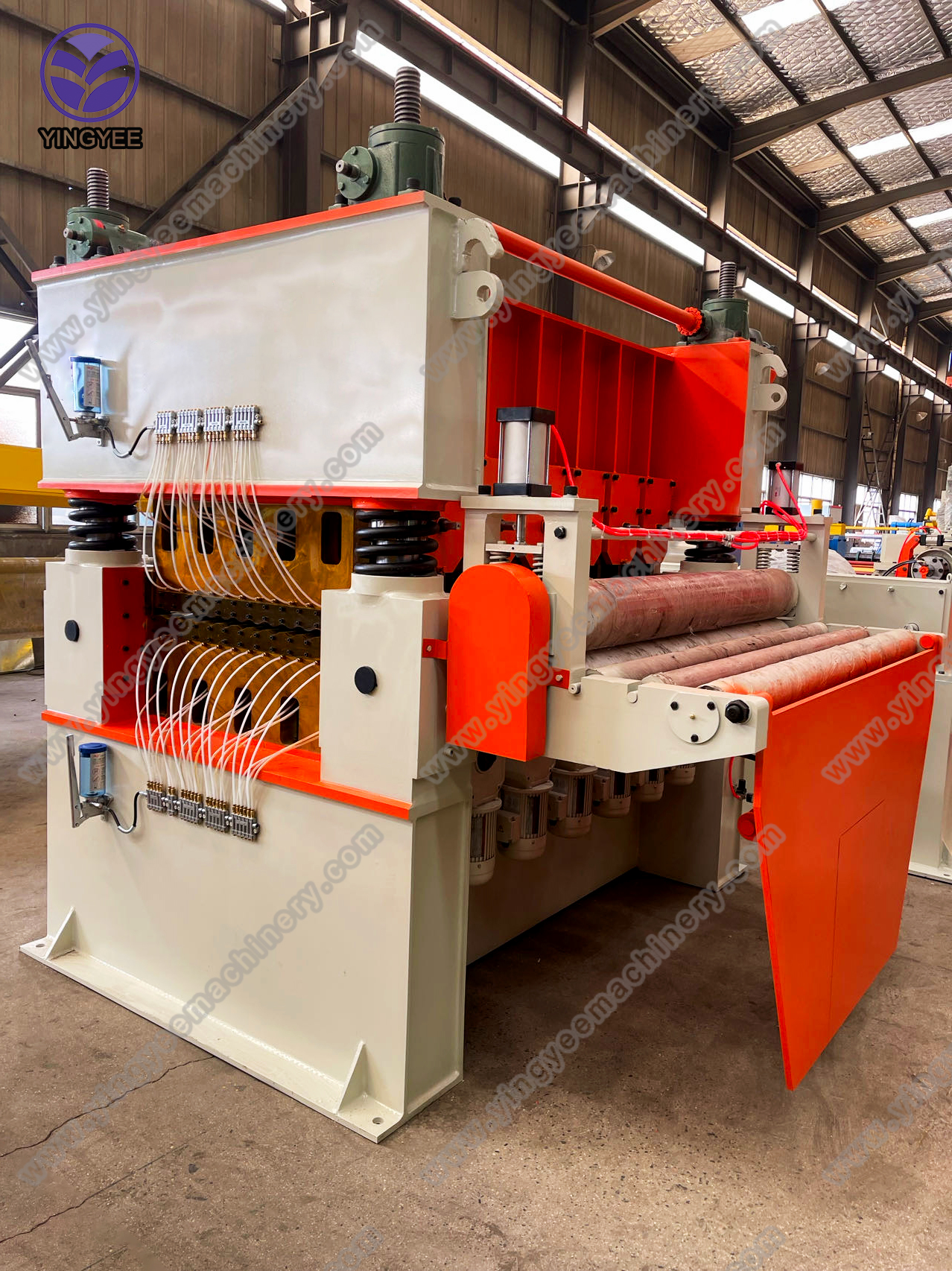
The operational efficiency of a stud making machine is profoundly influenced by technological advancements. Modern machines now feature computerized controls that enhance precision, speed, and safety. Automation in these machines reduces human error and enhances output consistency, which is crucial for meeting industry standards and client specifications.
Professional users of stud making machines acknowledge the importance of regular maintenance. Routine checks and servicing ensure the longevity of the machine and the quality of the studs produced. From lubricating moving parts to calibrating the computerized systems, maintenance is not only a recommendation but a necessity for staying ahead in competitive markets.
Authoritativeness in the stud making industry is characterized by adherence to international standards and certifications. Machines are often assessed on their compliance with ISO certifications, which reassure clients of quality and safety in production. It is advisable for businesses to select machines from manufacturers that have a proven track record and are recognized in the industry for their technology and reliability.
stud making machine
Customer feedback and case studies from existing users of stud making machines highlight their versatility and customization options. Whether used for creating standard-sized studs for building frames or custom shapes for specific industrial applications, these machines offer users flexibility in design without compromising on output precision. This adaptability is a decisive factor for businesses that deal with a diverse range of projects.
Integrating a stud making machine into a production line also requires considering the environmental impact. The modern industry is leaning toward sustainable practices, and stud making machines are no exception. Innovations aimed at reducing energy consumption and waste, such as using energy-efficient motors and recycling systems for scrap material, are now part of the standard offering from leading machine manufacturers.
Choosing the right stud making machine is a decision that encompasses evaluating technical specifications, manufacturer support, long-term maintenance requirements, and potential environmental impact. Companies that invest in high-quality, reputable brands often experience fewer downtimes, better product quality, and higher client satisfaction.
Trustworthiness in this domain comes from the transparency of machine capabilities, testimonials from credible users, and the manufacturer's commitment to post-sale service and education. Rigorous training support offered by manufacturers not only elevates the machine’s operational efficiency but also empowers the workforce, aligning with the business's strategic goals for growth and innovation.
In summary, a stud making machine is not merely an investment in equipment; it's a pivotal element in enhancing production efficacy, securing structural integrity, and maintaining a competitive edge in various industries. As the industry continues to advance, these machines will undoubtedly revolutionize traditional processes, setting new benchmarks for quality and efficiency.