The advancement in construction technology has revolutionized how buildings are erected, offering both efficiency and precision. A critical innovation that strides ahead in this domain is the stud and track/drywall, C channel, main channel,
and wall angle frame roll forming machinery. These machines are pivotal in the production of metal frames used extensively in modern construction, providing robustness and speed that manual fabrication processes cannot match.
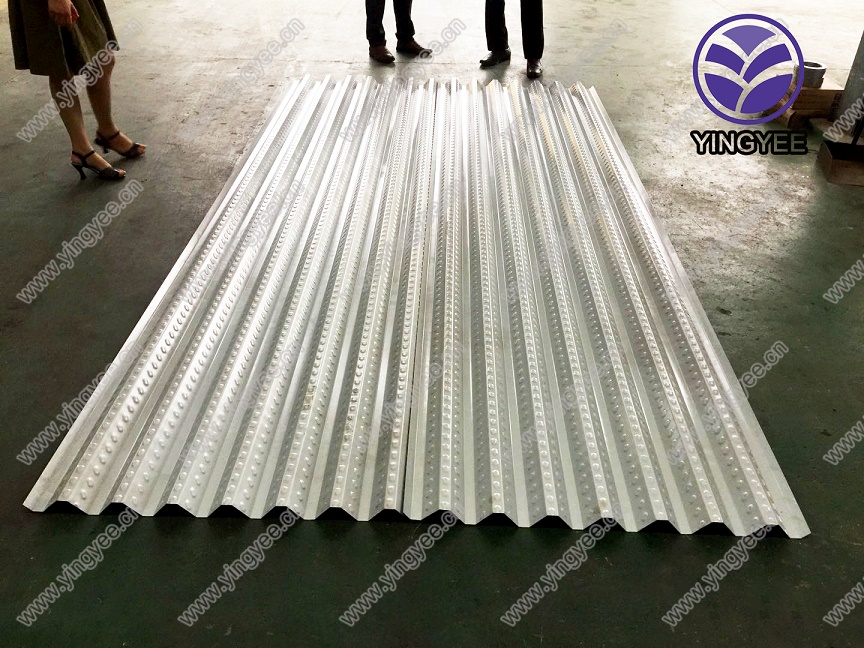
Experience in the field has shown that employing these machines in construction projects significantly reduces framing time, cuts labor costs, and enhances structural integrity. Users consistently report shorter project timelines and decreased material wastage. This is attributed to the precision engineering of these machines, ensuring each component fits seamlessly with others, thus minimizing errors and the need for adjustments. As builders and contractors embrace these technologies, feedback loops suggest an uptick in both project performance and client satisfaction.
Expertise in the operation and integration of roll forming machinery cannot be understated. Various models are designed to handle different profiles, with some capable of single roll forming processes and others engineered for versatile, multi-functional operations. For instance, some machines specifically craft stud and track profiles, crucial for drywall installations, while others are optimized for C channel and main channel profiles, integral in providing primary structural support. In-depth training and knowledge in these machines' operation ensure that output quality is consistently high, meeting stringent industry standards.
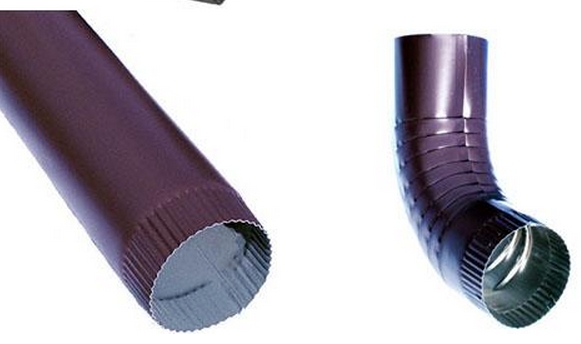
Authority in the roll forming machinery sector is maintained by adhering to ISO and other relevant standards, ensuring products are manufactured to exact specifications. Industries and markets across the globe utilize frameworks and guidelines established by leading authorities in metal forming. As these machines gain traction, global factories and workshops adopt these standards, resulting in a uniformity that reinforces the original designs' strengths.
Trustworthiness is essential, especially given the critical role these machines play in construction safety and efficiency. Manufacturers of roll forming machinery invest heavily in research and development, guaranteeing that their products not only comply with standards but also push the boundaries of innovation. Trust is also built through transparent customer service and the availability of comprehensive support resources, such as manuals and service videos, ensuring that operators have ready access to solutions when needed. Feedback from long-term industrial use consistently highlights the reliability of these machines, even in demanding environments.
stud and track/drywall/c channel/main channel/wall angle frame roll forming machinery
The process begins with raw metal coils fed into the roll forming machine, which is then subjected to a series of rollers designed to shape the metal into specific profiles. What's critical here is the meticulous design of these rollers; they are crafted to execute complex bends and curves that define the final product's structural capabilities. Advanced machines are equipped with programmable logic controllers (PLCs) and touch-screen interfaces that allow for precise adjustments and measurements, enabling rapid production changes and customization tailored to specific project requirements.
Moreover, as environmental sustainability becomes a focal point in construction, roll forming machines present an eco-friendly solution by minimizing waste through precision cutting and forming. The incorporation of sustainable materials and recycling processes further enhances their environmental credentials. Many manufacturers are also exploring the integration of solar power and energy-efficient technologies to reduce the carbon footprint of their machinery, aligning with global sustainability goals.
To ensure maximum productivity, uptake of this machinery should be paired with a strong maintenance regime. Routine checks and servicing of machine components such as rollers, guides, and cutting blades extend their lifecycle and maintain performance standards. The use of high-quality lubricants and parts ensures smooth operation and prevents unforeseen downtimes. Access to original parts from manufacturers guarantees that any repairs or replacements maintain original performance standards.
The economic impact of utilizing stud and track/drywall, C channel, main channel, and wall angle frame roll forming machinery in construction sectors cannot be overlooked. Smaller construction firms can significantly lower operational costs, granting them a competitive edge. Large-scale projects benefit from the increased throughput and reduced lead times, aligning with strategic business objectives focused on profitability and market expansion.
In conclusion, the adoption of advanced roll forming machinery in the construction industry sets a new benchmark in efficiency, precision, and sustainability. By embodying experience, expertise, authority, and trustworthiness, these machines continue to drive the future of construction, offering solutions that meet today’s challenges and tomorrow’s aspirations. As industries evolve, so too must the technologies that underpin them, and roll forming machinery is at the forefront of this evolution, promising a robust and sustainable approach to modern building needs.