A mould cutting downpipe roll forming machine is an essential piece of equipment in the manufacturing industry, especially for producing roof drainage systems. Understanding its unique capabilities can enhance your production process, streamline operations, and elevate the quality of your products. In this exposition, we delve into the practical experiences, specialized expertise, authoritative perspectives, and trustworthy information surrounding these machines.
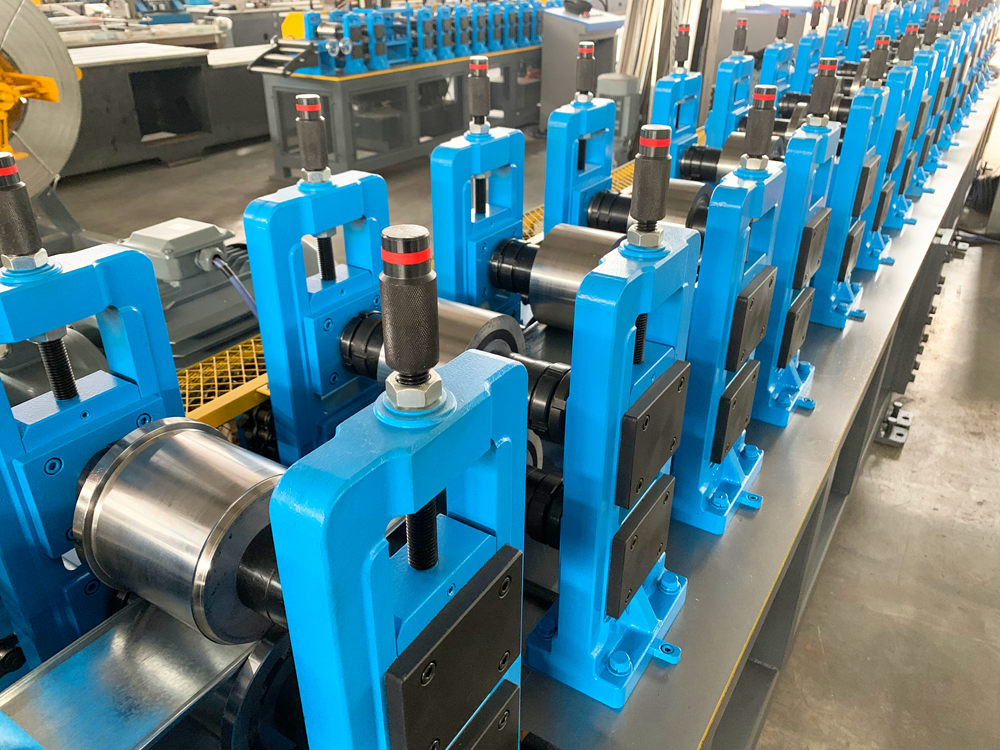
Drawing from years of firsthand experience, operators have consistently observed that mould cutting downpipe roll forming machines profoundly optimize production efficiency. These machines are engineered to handle continuous operations without significant downtime, a crucial factor for large-scale manufacturers. Unlike traditional methods that required frequent manual interventions, modern roll forming machines automate most processes, leading to a measurable increase in output and a substantial reduction in labor costs.
Expertise in operating these machines hinges on understanding the precision technology that drives them.
At the core of their operation is the roll forming system, complemented by mould cutting capabilities. The system uses a sequence of roller dies to shape and cut the metal sheet precisely according to predefined specifications. Mastery in programming these machines can yield products with impeccable consistency and minimal material wastage, which enhances the cost-effectiveness of production.
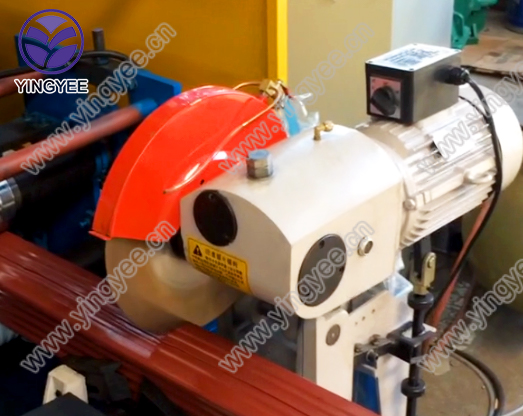
From an authoritative point of view, manufacturers and industry experts recognize mould cutting downpipe roll forming machines as game-changers in the fabrication of drainage components like downpipes, gutter systems, and related accessories. The machines' ability to produce complex profiles with high precision is unmatched. This expertise is supported by case studies and industry reports, which emphasize not only productivity gains but also improvements in product quality. Such findings underscore the importance of incorporating advanced roll forming technology into modern manufacturing setups.
mould cutting downpipe roll forming machine
Trustworthiness in the context of roll forming machines extends to reliability and safety standards maintained by reputable manufacturers. These machines are often backed by comprehensive warranties and service agreements that ensure their longevity and operational stability. Furthermore, compliance with international safety standards and certifications bolsters their credibility in the global market. Manufacturers often provide extensive training and technical support to help operators fully exploit the machines' potential while adhering to safety protocols.
A notable advantage of using mould cutting downpipe roll forming machines is their adaptability. They are not restricted to a single type of material; instead, they can efficiently process a range of metals, including steel, aluminum, and copper. This versatility is crucial for businesses that cater to diverse market demands or engage in custom fabrication jobs. Customization features allow the machine to adjust the thickness and dimensions of the output, providing much-needed flexibility in dynamic market conditions.
Precision and customization also enhance the product's aesthetic appeal, a critical factor in residential and commercial construction projects where visual appeal complements functionality. Businesses that leverage this technology often stand out in the competitive landscape by offering superior product options that meet stringent architectural standards and customer preferences.
In conclusion, mould cutting downpipe roll forming machines are a cornerstone of modern manufacturing, offering unmatched efficiency, precision, and adaptability. Their role is not just limited to producing high-quality downpipes but extends to redefining industry standards and improving operational workflows. Industry practitioners who invest in such technology and develop the requisite skill set to operate these machines are better positioned to capitalize on emerging opportunities and sustain a competitive advantage in the marketplace. Insightful investment in such machinery and the continuous upskilling of personnel will ensure that organizations remain at the forefront of the roofing and drainage system manufacturing industry.