The metal sound barrier cold bending machine is an essential tool for manufacturing industries dealing with the production of barriers that mitigate noise pollution. These barriers play a crucial role in urban areas, especially along highways, train tracks, and industrial zones where noise control is paramount. The cold bending process utilized by these machines is pivotal in shaping metal without the need for heat, thereby improving the material’s structural integrity and resistance to environmental factors.
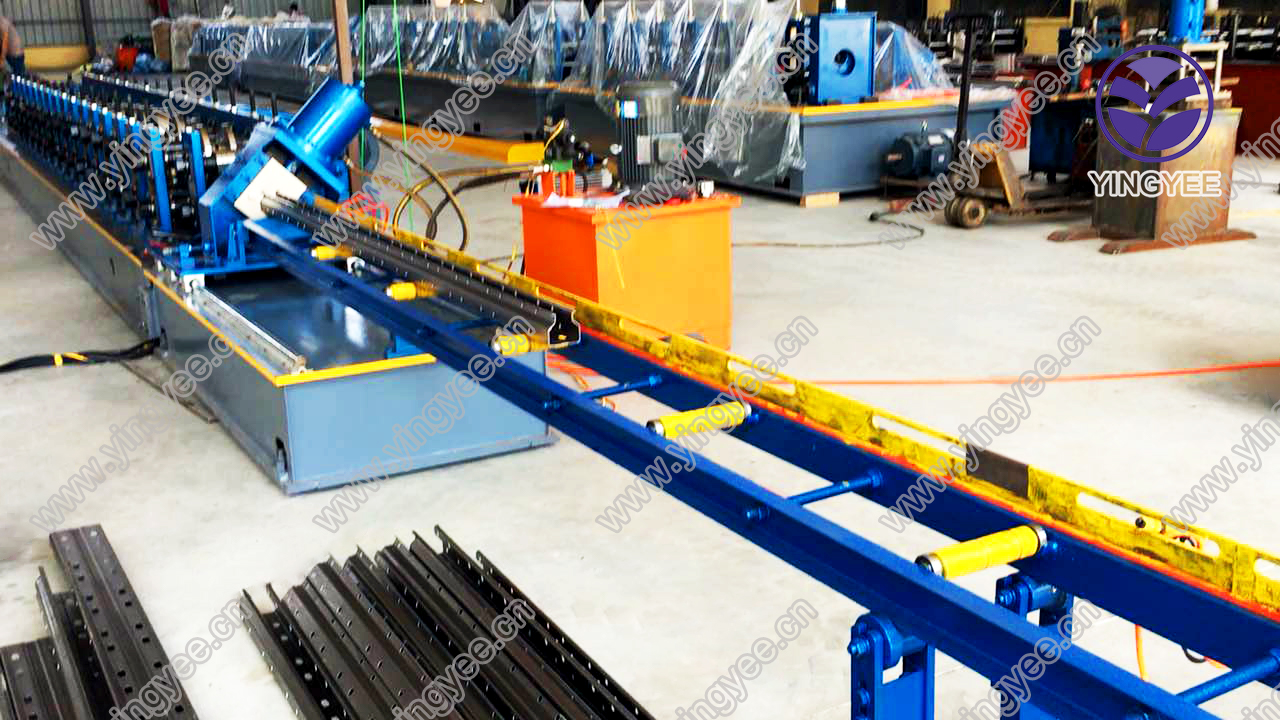
The core experience surrounding a metal sound barrier cold bending machine is its efficiency and precision in handling diverse metal types. As industries continually strive to meet stringent noise regulation standards, the demand for accurately constructed sound barriers rises. This demand necessitates machines that not only produce results quickly but do so without compromising on quality. Cold bending machines are designed to meet these expectations by utilizing advanced technology that allows precise control over the bending process, resulting in consistently high-quality barriers.
From an expertise standpoint, having a comprehensive understanding of the metallurgical properties of materials used in sound barriers is fundamental. Sound barriers often use materials like aluminum, galvanized steel, or alloy metals that are subject to various environmental stresses. The cold bending machine is engineered to handle these materials by ensuring that the mechanical processes involved do not produce microcracks or weaken the metal. The technical design of these machines incorporates features like adjustable bending speeds and programmable controls for different material types, which are essential for operations involving high volumes of metal barriers.

Authoritativeness in this domain is driven by the engineering precision and technological advancements in machine design. Manufacturers producing these cold bending machines often hold certifications and adhere to international standards like ISO, which assure clients of their reliability and safety. Furthermore, industry pioneers demonstrate authoritativeness by contributing to research and development, thereby advancing the manufacturing capabilities of these machines. By integrating cutting-edge technologies such as computer numerical control (CNC) systems, these machines offer unparalleled accuracy and repeatability, reinforcing their authority in metal forming processes.
metal sound barrier cold bending machine
Trustworthiness is underscored by the machine's operational longevity and the manufacturer's commitment to customer support and technical service.
A reputable manufacturer provides comprehensive training for operators, ensuring that they can effectively use the machines to their full potential. Additionally, these manufacturers prioritize customer satisfaction by offering robust after-sales services, including maintenance support and quick response times for any technical issues encountered. This reliability in both product and service enhances trust amongst users within the industry, making them valued partners in the manufacturing process.
The use of metal sound barrier cold bending machines also encompasses important safety considerations. Operators must possess not only technical skills but also an understanding of safety protocols to prevent accidents and maintain a safe working environment. Training programs and safety certifications are crucial in equipping operators with the knowledge to safely and efficiently handle these machines. This aspect of safety contributes significantly to the machine's trustworthiness and the overall productivity of the workspace.
Innovations in the field of cold bending technology continue to evolve, further enhancing the capabilities and applications of metal sound barrier machines. Newer models seek to incorporate energy-saving features and smart technology, which allow for remote monitoring and adjustments, providing industries with greater flexibility and control over their production processes. Such advancements not only position manufacturers at the forefront of innovation but also contribute to environmental sustainability efforts by reducing the carbon footprint of the manufacturing processes involved.
In conclusion, the metal sound barrier cold bending machine represents a convergence of experience, expertise, authoritativeness, and trustworthiness. It is an invaluable asset in the manufacturing industry, providing an efficient solution for noise control while ensuring the longevity and reliability of metal barriers. As technology progresses, these machines are poised to become even more integral to industry operations, continually adapting to the ever-evolving demands of urban development and environmental compliance. Whether through enhanced safety features, optimized performance, or reduced environmental impact, the metal sound barrier cold bending machine remains pivotal in shaping the infrastructure of noise control solutions.