The process of manufacturing complex industrial components has come a long way over the years, particularly in how cable trays are produced. Central to this evolution is the fully automatic cable tray cold roll forming machine, an epitome of modern industrial engineering that blends precision with efficiency to deliver high-quality products. This article takes a deep dive into the essence of these machines, elucidating their value from an experienced, expert, authoritative, and trustworthy lens.
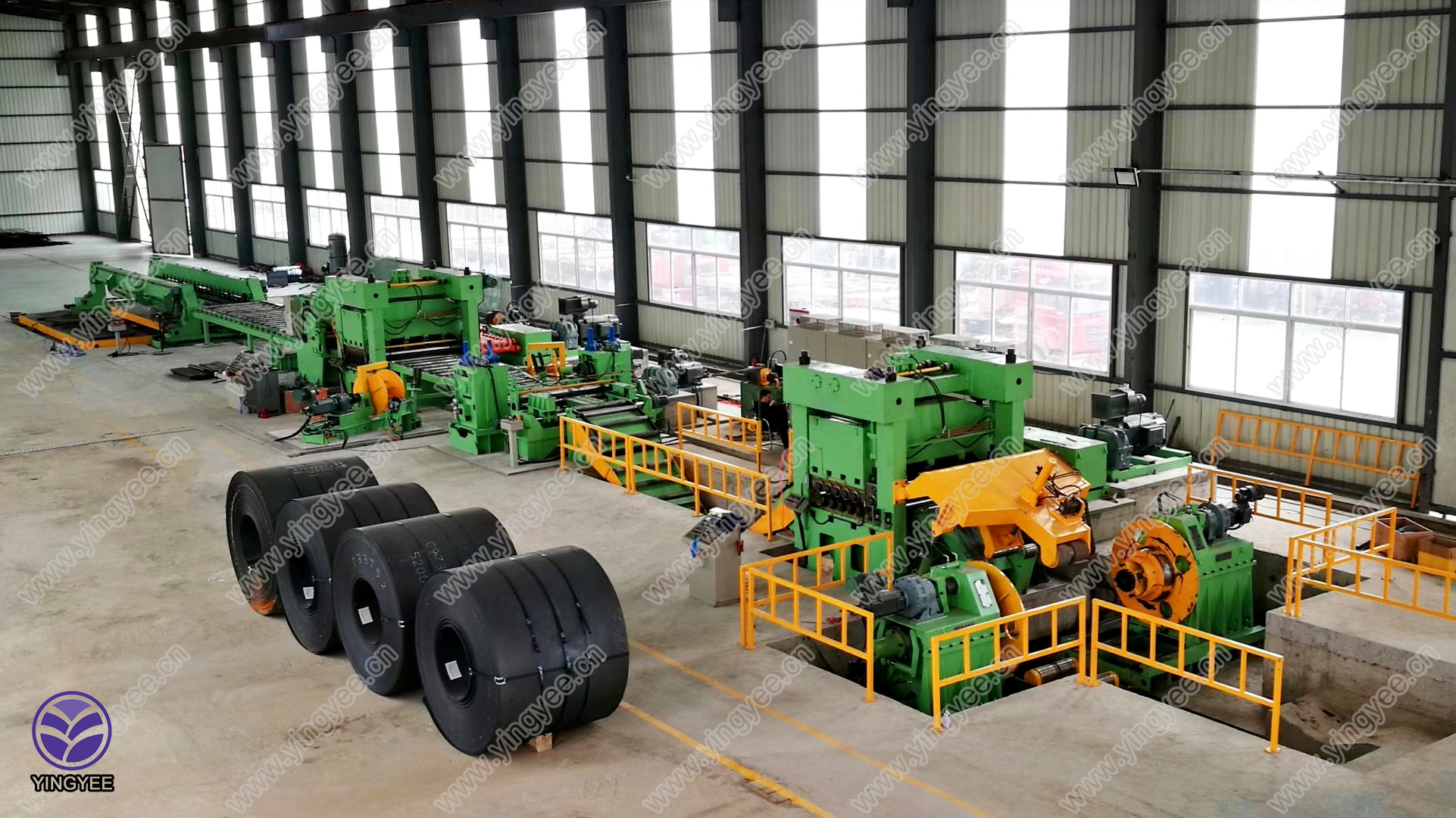
Fully automatic cable tray cold roll forming machines are instrumental in fabricating cable trays that serve as structural elements for safely managing and routing electrical cables in various facilities. With automation integrated into the design, these machines significantly streamline production processes, ensuring both precision and repeatability. Their core advantage lies in the highly automated sequence of operations, which drastically reduces human intervention and elevates production accuracy.
In terms of experience, users of these machines often report unparalleled efficiency and reliability.
The fully automatic nature means that once initial parameters are set, the machine can run continuously with minimal oversight. This continuous operation ensures that large volumes of cable trays are produced with consistent quality, an experience verified across different user testimonials in the industry. Furthermore, the seamless integration of software elements allows operators to quickly adjust to specific project requirements, which enhances adaptability in a dynamic market environment.
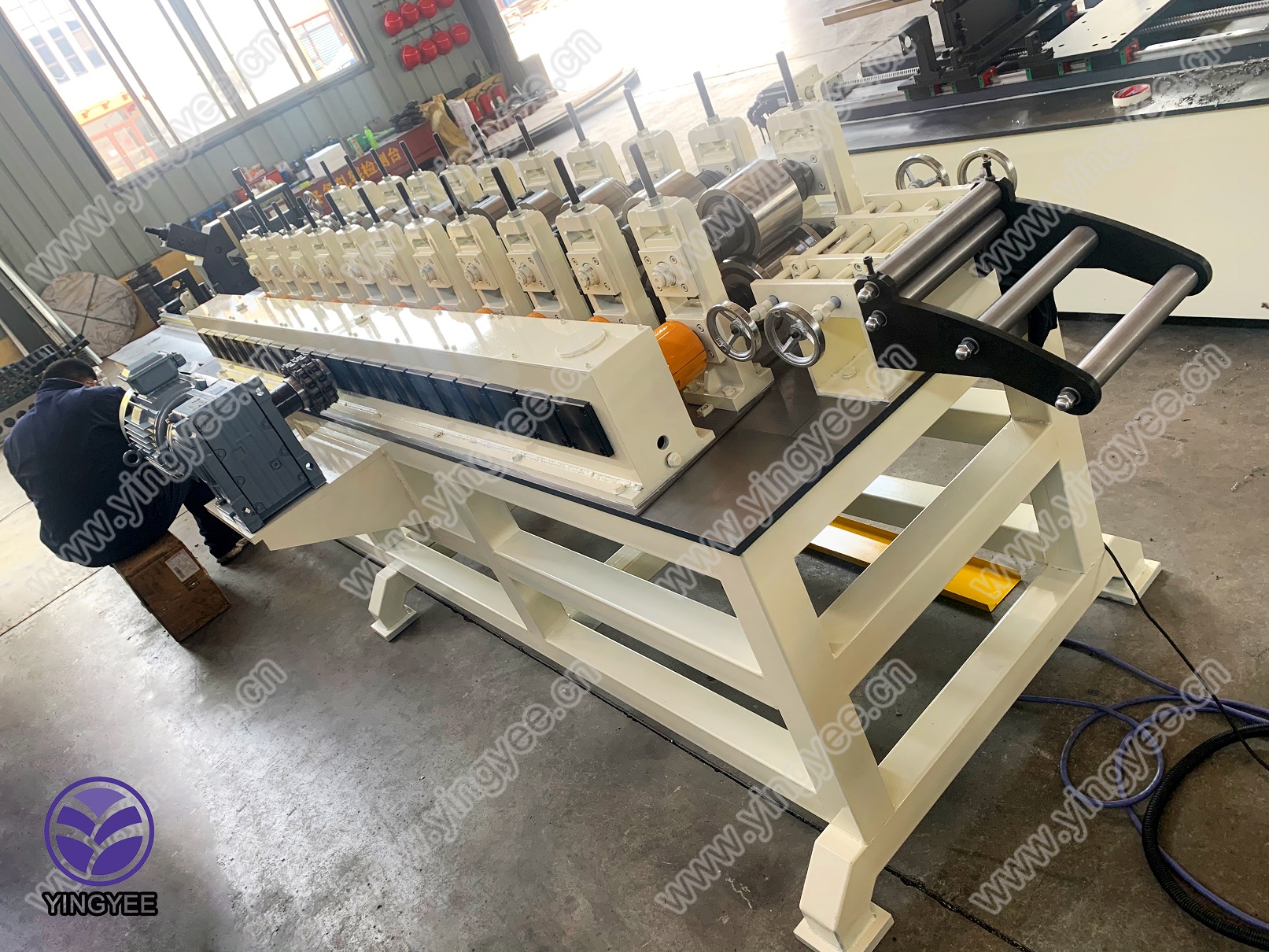
Expertise behind these machines cannot be overstated; the engineering that goes into designing and producing a fully automatic cable tray cold roll forming system demands a high level of technical knowledge and experience in both mechanical and computer-aided engineering. The machines incorporate advanced technology such as PLC (Programmable Logic Controller) systems, which facilitate precise control of the production process. These systems allow for the adjustment of multiple variables, including speed, material thickness, and shape dimensions, ensuring that the final product meets exact specifications. The involvement of engineers and industry experts in creating these machineries underscores their sophisticated design and operational efficacy.
fully automatic cable tray cold roll forming
Authoritativeness is deeply rooted in the recognition and accreditation these machines hold in the industry. Leading manufacturers of fully automatic cable tray cold roll forming machines often possess ISO certifications, which attest to strict adherence to international quality standards. These certifications not only validate the machine's performance and reliability but also demonstrate the manufacturer’s commitment to providing credible and authoritative solutions in the industrial sector. Industry experts frequently cite these machines as benchmarks in metal forming technology, further cementing their authoritative status in the market.
Trustworthiness of fully automatic cable tray cold roll forming machines is reflected in the robust and durable construction, tailored to withstand the rigors of heavy industrial usage. Customers across various industries, from construction to manufacturing, place significant trust in these systems due to their proven track record of uninterrupted service and minimal maintenance demands. Manufacturers often provide extensive warranties and customer support to back up their claims of reliability. This ongoing support framework, combined with the positive reviews and feedback from end users, strengthens the machines' reputation as trustworthy investments.
In essence, fully automatic cable tray cold roll forming machines epitomize the convergence of experience, expertise, authoritativeness, and trustworthiness in modern manufacturing technology. They represent a critical advancement for industries that require reliable and efficient production of cable management solutions. As technology continues to evolve, these machines are poised to become even more integral to the manufacturing landscape, continually setting new standards for quality and performance in industrial machinery.