In the ever-evolving world of construction, efficiency and adaptability are key. A double layer roof sheet forming machine stands as a testament to modern innovation, blending technology with practicality to meet the demands of contemporary building projects. This machinery is more than just a tool; it's a crucial component in the arsenal of construction professionals, merging cutting-edge technology and robust engineering to deliver superior results.
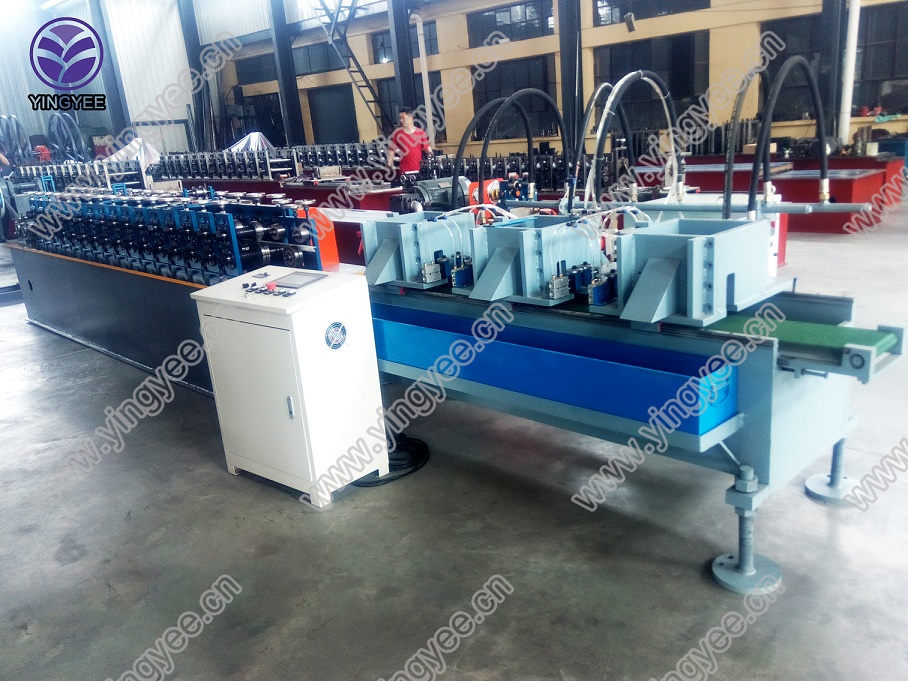
A double layer roof sheet forming machine is a specialized piece of equipment designed to manufacture metal roofing in two distinct profiles simultaneously. This unique capability represents significant advancements in construction technology, offering substantial benefits in terms of resource management, production efficiency, and versatility.
One of the primary advantages is its ability to save space and investment costs. Traditionally, producing different roofing profiles would require multiple machines, increasing the required floor space and capital investment. However, a double-layer machine integrates these capabilities within a single unit, effectively doubling productivity without doubling costs or space requirements. This consolidation empowers manufacturers to maximize their output while minimizing overheads, a critical consideration in contemporary business environments.
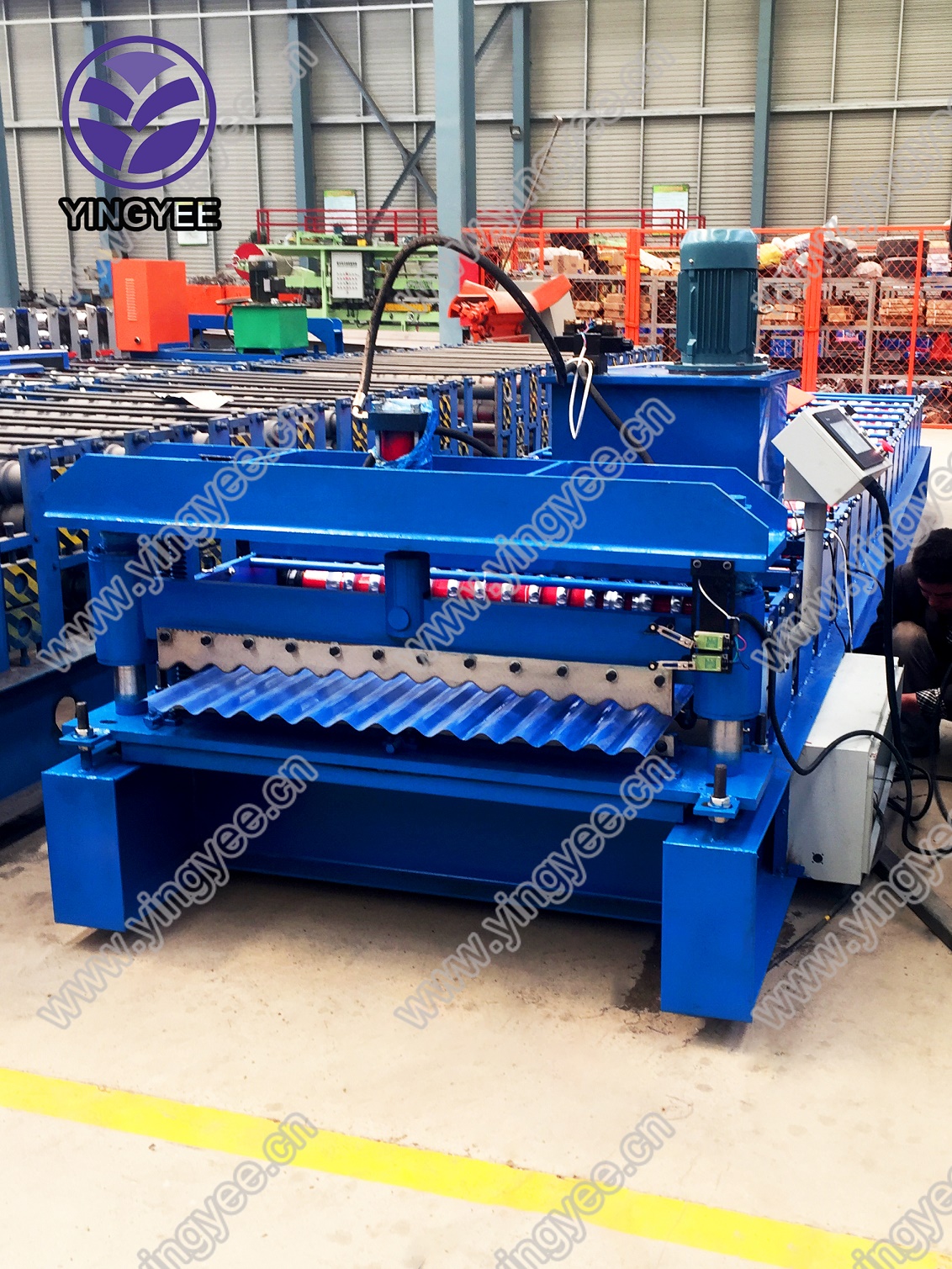
From an expertise perspective, operating a double layer roof sheet forming machine demands an understanding of sophisticated mechanisms and controls. These machines are equipped with advanced PLC control systems that enhance precision and reliability, ensuring that each sheet produced meets stringent quality standards. Operators must be well-versed in these control systems, capable of troubleshooting and maintaining machinery to optimize performance and extend service life.
Further establishing its credibility, the double-layer machine is constructed using high-grade materials and components. The robust build quality not only improves the machine's longevity but also enhances its ability to produce a consistent product over extended periods. This durability makes it a trusted choice for operations aiming to maintain continuous production cycles without the threat of frequent breakdowns or the need for constant maintenance.
double layer roof sheet forming machine
In terms of adaptability, double layer roof sheet forming machines cater to a wide array of design requirements. They can produce various profiles, including trapezoidal, corrugated, and more complex custom designs, thus enabling construction professionals to meet specific project needs with ease. This versatility is critical in an industry where aesthetic and functional demands can vary greatly from one project to another.
Furthermore, the machine’s capability to swiftly switch between profiles minimizes downtime, an essential factor in projects with tight deadlines. This agility allows manufacturers to adapt to market demands quickly, providing a competitive edge in an industry where time is of the essence.
Understanding the market dynamics, manufacturers have optimized these machines to reduce energy consumption and operational costs. Energy efficiency is achieved through intelligent machine design, which involves minimizing waste and optimizing power usage without compromising output quality. This consideration for sustainability not only reduces operational costs but also aligns with global movements towards environmentally conscious manufacturing practices.
As a cornerstone in the world of sheet metal forming machines, the double layer variant is supported by extensive service networks and training programs. These initiatives ensure that operators are proficient in both the practical operation and theoretical understanding of the machine, fostering a sense of reliability and trust within the user community. The availability of comprehensive customer support services further solidifies the machine’s standing as a reliable and trusted investment for any manufacturing entity.
In conclusion, the double layer roof sheet forming machine exemplifies modern progress in construction equipment. Its ability to seamlessly integrate multiple functionalities into a single, compact, and efficient unit is a testament to the ongoing evolution in engineering and construction technologies. For professionals in the field, this machine represents not just an investment in equipment, but an investment in future-ready capabilities that will drive success in an increasingly competitive market.