Vertical large span roll forming machines represent a pinnacle of innovation in the metal forming industry, revolutionizing how large-scale constructions are approached. These machines are celebrated for their ability to produce massive, uniform components used extensively in sectors like construction, automotive, and aerospace. Their importance cannot be understated, as they combine precision engineering with high efficiency, catering to the growing demand for streamlined production in an increasingly competitive market.
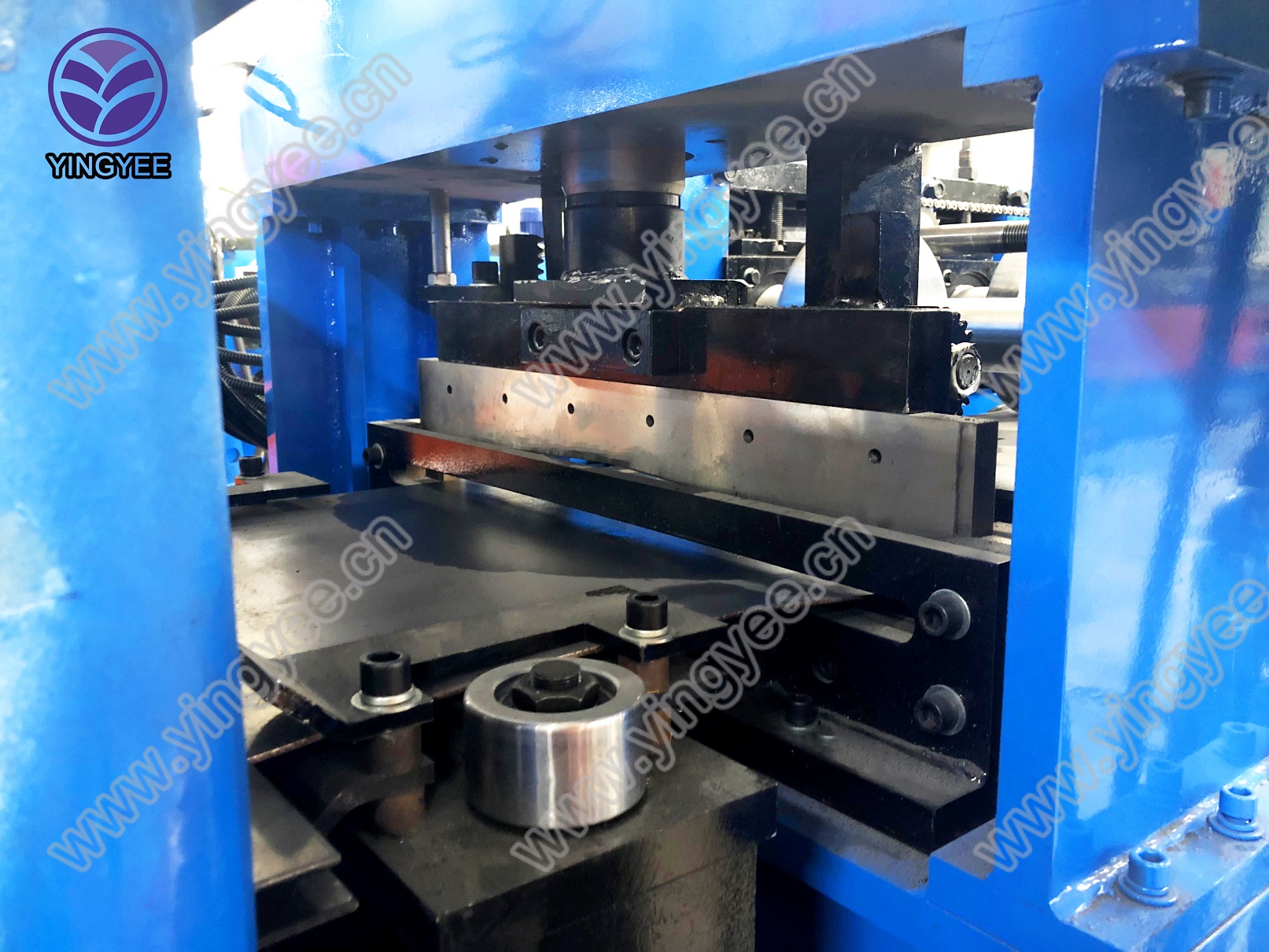
One of the defining attributes of these machines is their ability to produce continuous metal profiles with outstanding accuracy and consistency. Their design caters to the production of long, vertical structures without the need for intermediate welding or bolting, thus minimizing structural weaknesses and enhancing overall durability. This capability aligns with the modern architectural trend that emphasizes sleek, uninterrupted lines, often seen in the latest skyscraper and bridge designs. The products created by these machines offer enhanced load-bearing strengths, which are critical in geographies prone to seismic activities or high wind speeds.
The technology behind vertical large span roll forming machines is rooted in precision engineering and cutting-edge software integrations. Advanced computer controls ensure that each piece rolled from the machine is crafted with microscopic precision, adhering to exacting specification standards required in projects of national and international significance. With user-friendly interfaces, operators can manage complex production requirements with remarkable ease, thus reducing the potential for human error significantly. As industries lean more towards automation, the reliability of such technology plays a crucial role in ensuring uptime and operational consistency.
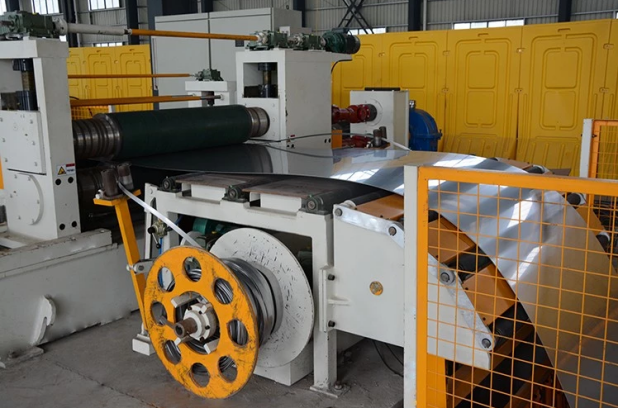
The advent of vertical large span roll forming machines also reflects a significant shift toward sustainable manufacturing practices. Traditional methods often resulted in considerable waste due to off-cuts and erroneous production batches. However, with roll forming technology, materials are utilized more efficiently, aligning with global directives for zero waste and sustainable resource management. Moreover, by reducing the need for secondary processing – which often involves energy-intensive practices like welding and cutting – these machines contribute to a significant reduction in a facility's carbon footprint. As corporations face mounting pressures to demonstrate corporate social responsibility, investing in sustainable technology not only enhances production capabilities but also strengthens brand reputation.
vertical large span roll forming machine
Undoubtedly, selecting the right vertical large span roll forming machine involves weighing several critical factors. Companies must consider the specific materials they frequently work with, as the machine must be capable of handling different metal grades and thicknesses. Another factor is the expected production volume; high-capacity machines are ideal for large orders while ensuring minimal downtime due to maintenance. Furthermore, it is essential to assess the machine's adaptability to emerging technologies and design trends. Machines that offer modular add-ons or software upgrades ensure longevity and relevance amidst rapidly changing industrial landscapes.
Experts in the field consistently emphasize the importance of thorough training and regular maintenance schedules. Even the most advanced machinery requires skilled personnel to ensure optimal performance and longevity. Manufacturers frequently offer comprehensive training programs to familiarize operators with the nuances of machine function and maintenance. A well-maintained machine not only runs efficiently but also minimizes unexpected operational stoppages, thereby safeguarding against financial losses.
In conclusion, vertical large span roll forming machines symbolize a blend of traditional craftsmanship and futuristic technology, reshaping the boundaries of metal forming industries. As they continue to evolve, these machines will undoubtedly play a more pivotal role in meeting the increasing demands for strength, precision, and sustainability in modern manufacturing processes. Investing in such equipment not only amplifies production capabilities but also signifies a commitment to innovation and environmental stewardship, reinforcing a company’s position as a leader in their industry.