In the dynamic world of industrial manufacturing, understanding the intricacies of a zinc making machine is crucial for those seeking to harness the material's benefits. These machines are at the cornerstone of producing zinc, an element vital for numerous applications ranging from galvanization to die-casting. Through both advanced technology and expert engineering, zinc making machines transform raw zinc ore into a purified and usable form.
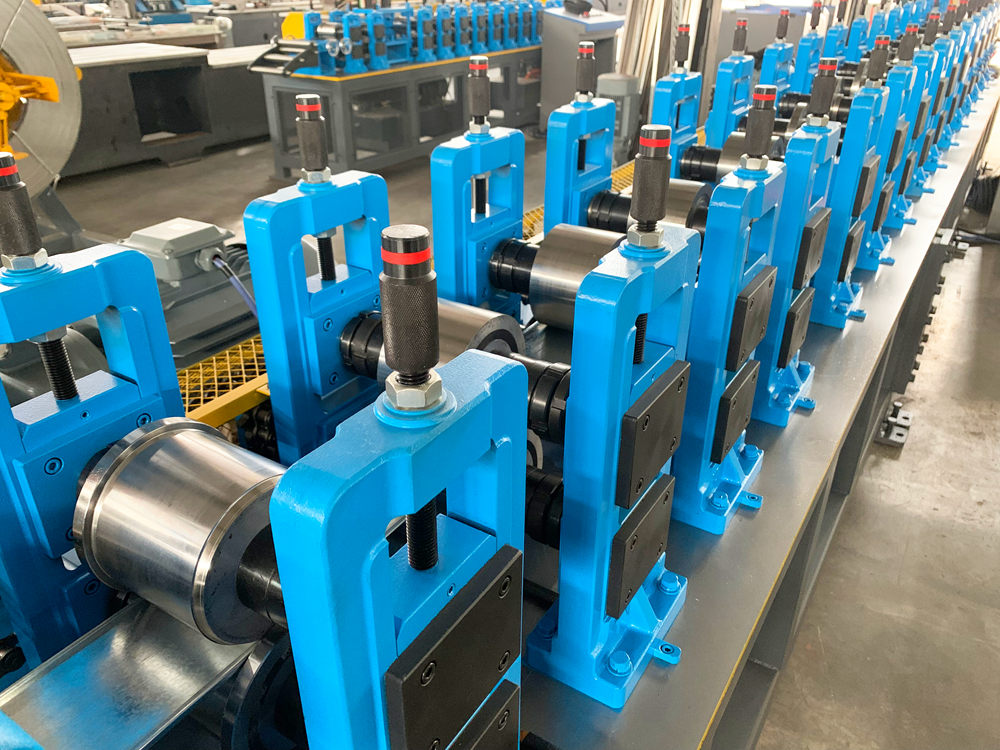
The process begins with the meticulous selection of high-quality zinc ore, which sets the foundation for the final product. The ore undergoes a crushing and milling process to reduce particle size, ensuring optimal results in subsequent steps. Expertise in metallurgy ensures that this preliminary phase is executed precisely, safeguarding against impurities that could compromise quality later.
At the heart of a zinc making machine is the smelting furnace, an area where experience and technological advancement converge to refine the material. Temperatures inside the furnace must be meticulously controlled to facilitate the safe and efficient conversion of zinc concentrate into molten metal. Sophisticated automation systems monitor these temperatures, offering reassurance and precision that underscore the machine's authority in metallurgy.
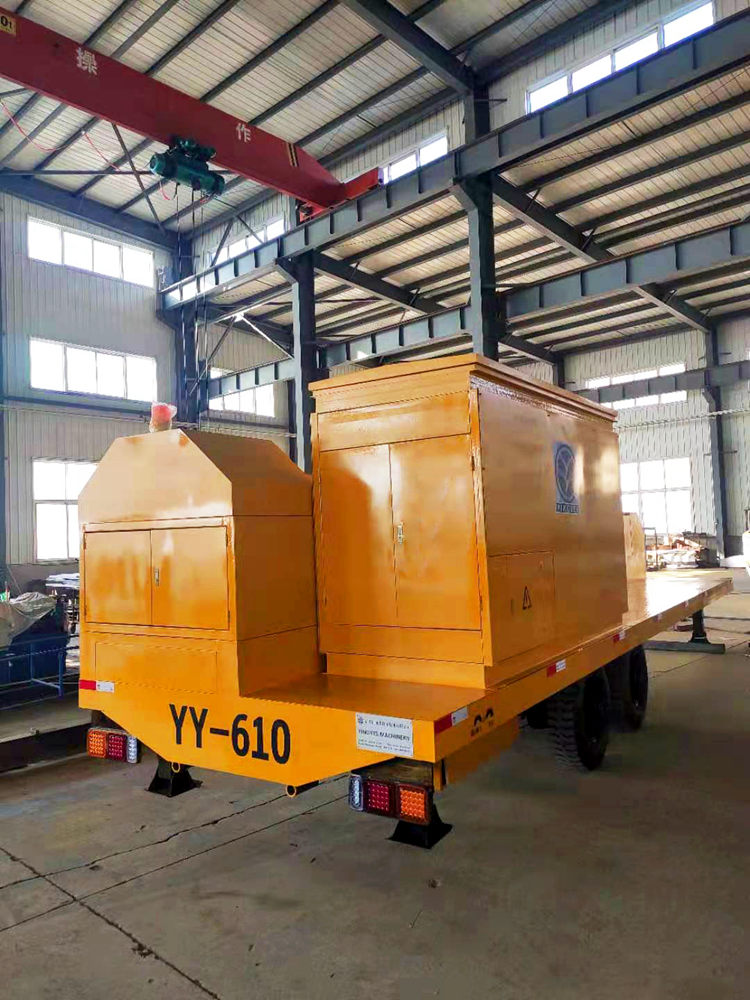
Environmental consideration plays a critical role as well, underscoring the thought leadership behind the design of modern zinc making machines. The inclusion of emission control systems not only showcases a commitment to ecological responsibility but also builds trust with stakeholders and regulatory authorities. Such systems effectively minimize the release of sulfur dioxide, a byproduct of zinc smelting, ensuring that operations remain within environmental compliance.
zinc making machine
Furthermore, industry experts advocate for machines equipped with energy-efficient technologies. These innovations reduce overall operational costs and enhance the sustainability profile of zinc production, offering users a blend of economic viability and environmental stewardship. This expertise-driven design not only reflects the authority of the machinery but also bolsters the credibility of businesses that employ it.
Maintaining this equipment demands a deep understanding of both mechanics and metallurgy, a domain where trustworthiness and expertise intertwine.
Regular maintenance ensures longevity and optimal performance. Skilled technicians, certified and knowledgeable, are pivotal, offering insights and servicing that elevate machine reliability.
For businesses that aim to excel in the zinc production space, partnering with reliable manufacturers and service providers becomes essential. These entities encapsulate the experience, expertise, and authority needed to navigate the complexities of zinc production. Vetting partners based on their technological advancements, commitment to quality, and track record in the industry becomes an implicit demonstration of trustworthiness.
In conclusion, zinc making machines stand as a testament to human ingenuity and industrial prowess. Their role in transforming raw materials into valuable commodities is underscored by technological advancements, expert engineering, and a steadfast commitment to sustainable practices. Through these machines, businesses not only contribute to industry but also adhere to global efforts for a more sustainable future, making them a vital asset in modern manufacturing.