The modern construction industry has evolved significantly, with efficiency, precision, and innovation at the forefront of every project. A prime example of this evolution is the stud and track, drywall, C channel, main channel,
and wall angle cold roll forming machines. These machines are instrumental in streamlining construction processes, ensuring structural integrity, and maintaining cost-effectiveness, making them indispensable tools for any serious builder.
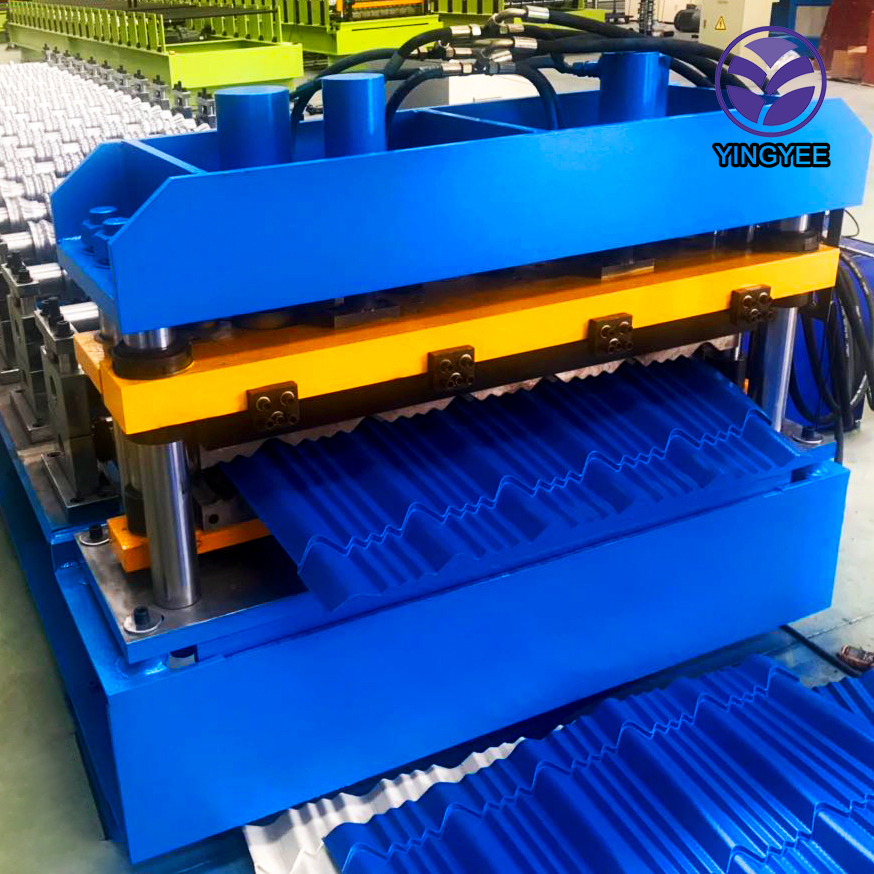
Cold roll forming is a continuous bending operation in which sheet or strip metal is plastically deformed along a linear axis. Having emerged as a technology preferred for its precision and high flexibility, these machines transform raw metal into precisely shaped profiles that are vital for the construction industry. The prowess of this machinery lies in its ability to seamlessly produce consistent, durable, and high-quality components that are critical in drywall installations, among other applications.
The application of stud and track systems in construction cannot be overstated. These integral frameworks support drywall structures, offering a reliable foundation for internal walls and partitions. Using a cold roll forming machine tailored to produce studs and tracks, manufacturers can produce high volumes of standardized components with optimal efficiency and minimal waste. These machines can handle various dimensions, gauging the specific needs of a project, thus allowing for custom production runs when necessary. As a result, users can significantly reduce material costs while also enhancing structural integrity—a crucial consideration for any construction endeavor.
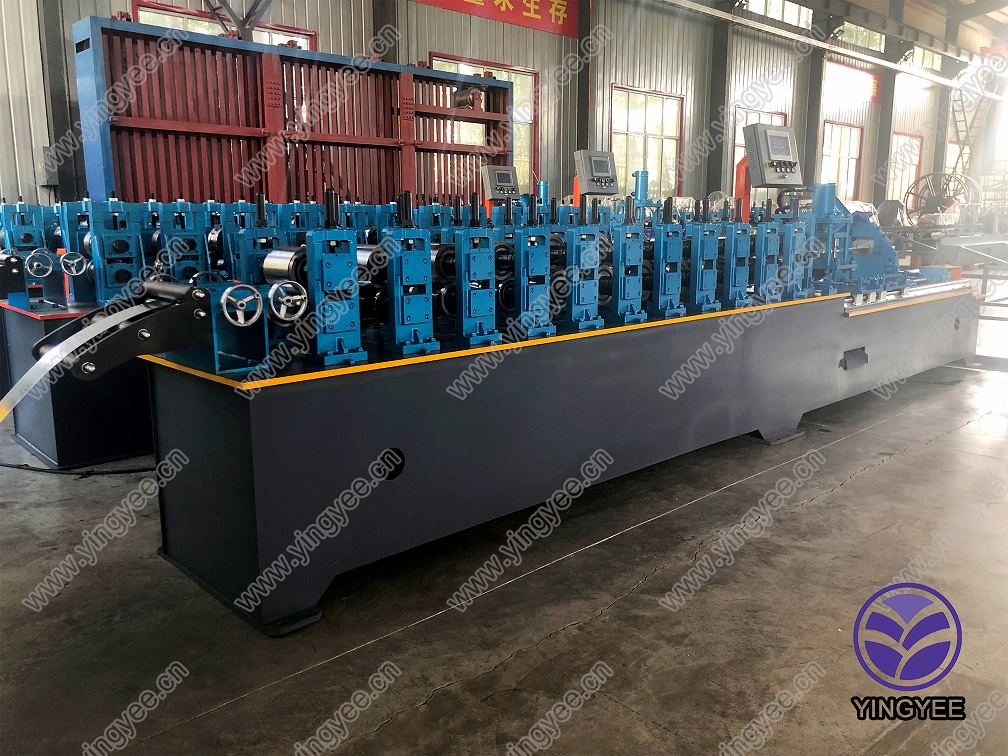
Expertly manufactured C channels and main channels play a pivotal role in building and architectural applications. Their robust design ensures that they can withstand substantial loads, making them ideal for use in framing systems. The precision of cold roll forming machines means that these channels can be fashioned to exact specifications, enabling architects and builders to rely on these components for intricate and demanding projects. The benefit of using a cold roll forming machine is the high level of customization available, allowing users to determine the specific configurations required for their projects, thus ensuring both efficacy and compliance with relevant building standards.
Wall angles, another vital component in the drywall construction arsenal, benefit immensely from cold roll forming technology. Wall angles provide the necessary support edges for suspended ceiling grids, ensuring square and level ceilings. By using a cold roll forming machine, you can produce wall angles that meet stringent dimensional tolerances and design criteria, essential for maintaining the aesthetic and functional integrity of interior spaces. The capability of these machines to output a large quantity of uniform pieces translates into substantial cost savings and enhanced project timelines—a compelling advantage for contractors.
stud and track/drywall/c channel/main channel/wall angle cold roll forming machine
Ensuring the proficiency of your operation with cold roll forming machines requires understanding the mechanics and components of the machines themselves. Typically, they include decoilers, leveling systems, punching devices, cutting units, and the roll forming stations themselves. Each component plays a crucial role in the quality and efficiency of production, underscoring the importance of routine maintenance and periodic upgrades where necessary.
The expertise required to operate cold roll forming machines extends beyond basic mechanical skills. It encompasses an in-depth understanding of material properties, foundational knowledge of how changes in tooling can affect the final product, and the ability to interpret complex design blueprints. As the industry continues to advance, staying abreast of technological developments and undergoing regular training becomes ever more essential. In doing so, operators and builders alike can leverage these machines to their full potential, ensuring optimal output quality.
When selecting a cold roll forming machine for your needs, consider factors such as the machine’s speed, flexibility, and capacity to integrate with other systems. Additionally, supplier reliability, warranty terms, and after-sales service are equally essential factors. Partnering with a reputable and experienced manufacturer will inevitably enhance your project’s success, providing robust, reliable machinery backed by a comprehensive support network.
The future of construction technology undoubtedly lies in improved automation and precision capabilities. Cold roll forming machines will continue to be at the heart of this progression, supporting increasingly complex architectural designs while promoting efficient and sustainable construction practices. For those aiming to achieve a competitive edge in the field, investing in this technology is not just an option—it’s a necessity. Embrace the innovation that cold roll forming machines offer and transform your building projects with efficiency, precision, and the unwavering assurance of quality.