The Significance of Strut Channel Roll Forming in Modern Construction
In the realm of construction and engineering, the process of strut channel roll forming holds a significant position due to its versatility and efficiency. This specialized manufacturing technique is an integral part of metal fabrication, particularly in creating structural support systems for various applications.
Strut channels, also known as C-channels or slotted metal framing, are widely used in architectural and industrial settings for their strength and adaptability. They serve as a backbone for supporting pipes, wires, and other mechanical equipment, providing a robust and reliable framework. The roll forming process is the key to producing these channels with precision and consistency.
Roll forming is a cold-forming process where a strip of metal is passed through a series of consecutive roller dies, gradually shaping it into the desired cross-section. In the case of strut channels, this results in a 'C' shaped profile with slots along the length for easy attachment of accessories. The process is highly automated, allowing for high-speed production and customization, making it ideal for mass manufacturing.
The advantages of strut channel roll forming extend beyond just efficiency. It offers a cost-effective solution compared to traditional methods like cutting and welding, as it reduces material waste and labor costs It offers a cost-effective solution compared to traditional methods like cutting and welding, as it reduces material waste and labor costs
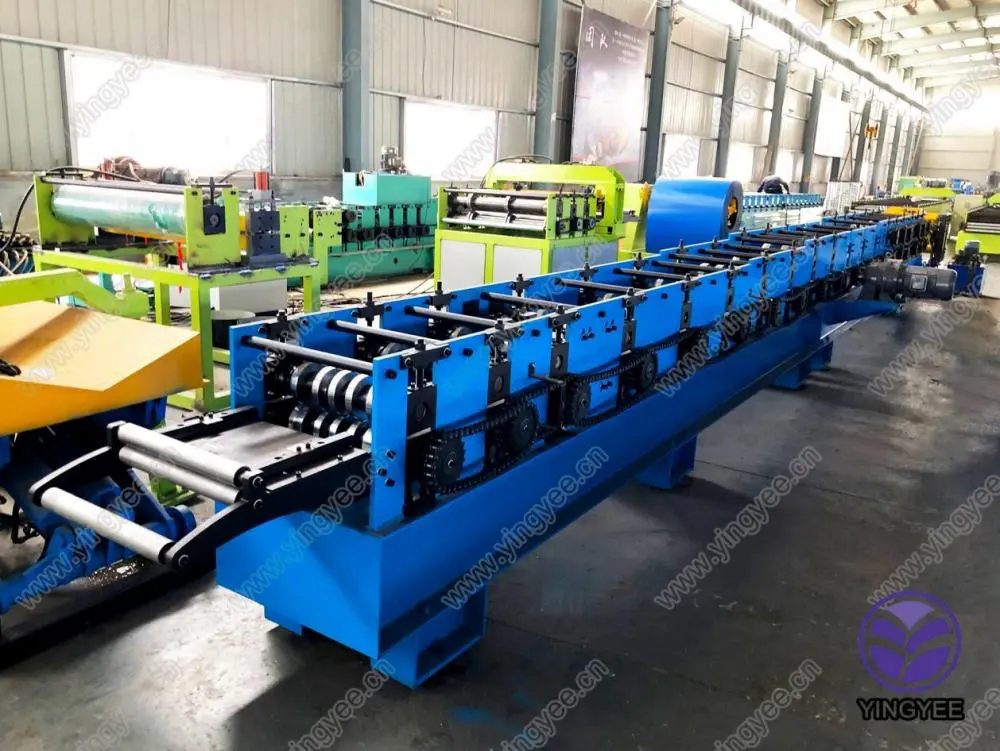
It offers a cost-effective solution compared to traditional methods like cutting and welding, as it reduces material waste and labor costs It offers a cost-effective solution compared to traditional methods like cutting and welding, as it reduces material waste and labor costs
strut channel roll forming. Moreover, the uniformity achieved through roll forming ensures that strut channels meet stringent quality standards, enhancing overall structural integrity.
Furthermore, the roll forming process allows for a wide range of materials to be used, from mild steel to aluminum and stainless steel, catering to diverse project requirements. The formed channels can also be galvanized or powder-coated, providing additional protection against corrosion and enhancing their aesthetic appeal.
In addition to standard strut channels, roll forming technology enables the creation of custom profiles, such as Z-channels, U-channels, or even non-standard shapes for specialized applications. This flexibility makes strut channel roll forming an indispensable tool in modern construction, from commercial buildings to infrastructure projects and even in the automotive and aerospace industries.
In conclusion, strut channel roll forming is more than just a manufacturing technique; it is a transformative process that drives innovation in construction and engineering. Its ability to produce strong, adaptable, and cost-effective strut channels has solidified its place as a cornerstone in contemporary building practices. As technology continues to advance, we can expect even greater precision, efficiency, and possibilities from strut channel roll forming in the future.