In the realm of modern construction and manufacturing, innovation and precision define the success of any structure. One tool that exemplifies this is the steel downpipe roll former making machine. This apparatus not only transforms how drainage systems are manufactured but raises the bar in quality and efficiency.
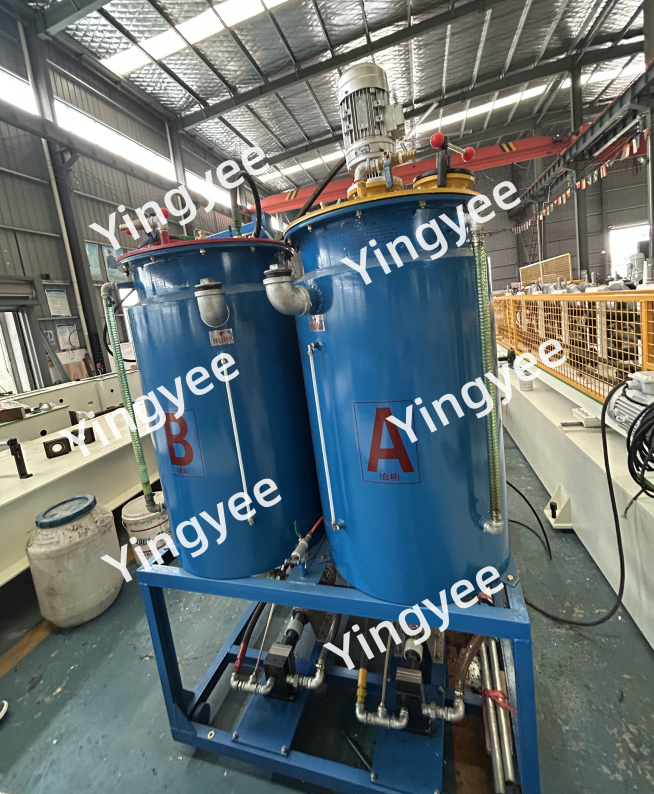
Steel downpipe roll forming machines are indispensable in producing high-quality downpipes used in both residential and commercial buildings. Constructed to handle various thicknesses and widths of steel, these machines are the backbone of gutter manufacturing. They work by feeding steel coils through a series of roll stations, where each station incrementally alters the shape of the metal until a fully formed downpipe emerges.
Experience with these machines has shown that they offer remarkable consistency in product output. As noted by industry veterans, utilizing a steel downpipe roll former significantly reduces the margin for error compared to manual methods. These machines are engineered with precise calibrations, allowing for flawless adjustments and ensuring that every length of downpipe produced meets stringent quality standards. Users appreciate this reliability, which translates into minimized material waste and cost savings.
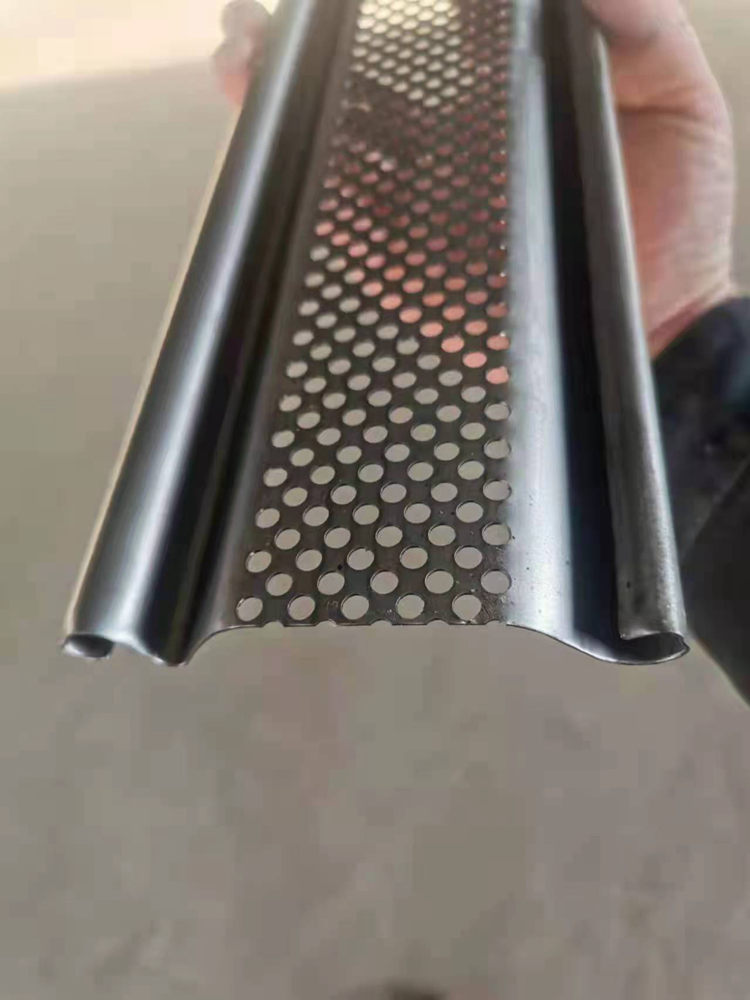
The expertise involved in the design and operation of a steel downpipe roll former is a testament to engineering excellence. Each component, from the de-coiler to the cutting system, is crafted to perform specific functions that enhance the overall production process. Engineers continuously refine these machines by incorporating advanced technologies such as computer numeric control (CNC) systems, which provide operators with a user-friendly interface while managing complex configurations automatically.
Professionals in the field recognize the authoritative advancements that steel downpipe roll formers bring to metalworking. This authority stems from the machine's ability to create downpipes with enhanced structural integrity. The roll forming process produces sections that are strong and durable, traits essential for components exposed to weather elements. Furthermore, these machines are capable of crafting downpipes with smooth finishes, eliminating the need for additional sanding or polishing and thus reducing production time.
steel downpipe roll former making machine
Central to the trustworthiness of steel downpipe roll formers is their durability and longevity. Manufactured from top-grade materials, these machines are designed to withstand the demanding environment of high-volume production facilities. This reliability is supported by comprehensive maintenance protocols and regular updates from manufacturers, ensuring that operators are well-equipped to keep their machines in optimal condition.
While the advantages of steel downpipe roll forming machines are numerous, choosing the right model for a specific application requires careful consideration. Factors such as production volume, material specifications, and space constraints play a pivotal role in decision-making. Manufacturers provide tailored solutions to meet diverse client needs, offering customization options that align machine capabilities with business objectives.
A noteworthy aspect of these machines is their adaptability to evolving industry standards. Whether responding to new environmental regulations or integrating sustainable materials, steel downpipe roll formers can be configured to maintain compliance without compromising quality or efficiency. This adaptability marks a significant shift towards greener production techniques that reduce environmental footprints while maintaining competitive advantages in the market.
The steel downpipe roll former making machine is an exemplary illustration of how technology continues to revolutionize production methods in the construction industry. By investing in this machinery, manufacturers position themselves at the forefront of innovation, ensuring they deliver superior products that set new benchmarks in quality and reliability. Through ongoing development, these machines not only meet the existing demands of the industry but also anticipate future trends, revolutionizing operations and inspiring confidence among stakeholders.