Navigating the world of heavy-duty vehicle maintenance can lead to discovering intricate machinery designed to enhance both productivity and efficiency. One pivotal tool for the manufacturing and repair industry is the semi truck fender cold bending machine. This machine serves the niche market of reshaping and fabricating fenders for large vehicles, providing an essential service in custom automotive fabrication and repair shops.
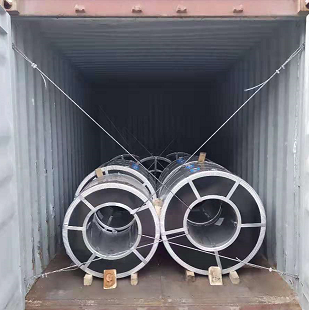
The concept of cold bending, specifically for semi truck fenders, is both innovative and vital for maintaining the structural integrity of large vehicles. These machines are expertly engineered to bend metal without the application of heat, a process that maintains the metal's strength and reduces the risk of weakening or damaging the material through thermal expansion. The advantage of cold bending lies in its ability to produce consistent and precise results, a crucial factor when dealing with safety-critical components like truck fenders.
Experience with these machines reveals a multitude of benefits for businesses focused on heavy-duty vehicle maintenance and customization. For starters, the precision offered by a semi truck fender cold bending machine translates into less waste and more efficient utilization of materials. Operators have reported a significant reduction in production time, as the cold bending process minimizes the need for additional cooling periods and allows for immediate handling of the shaped components.
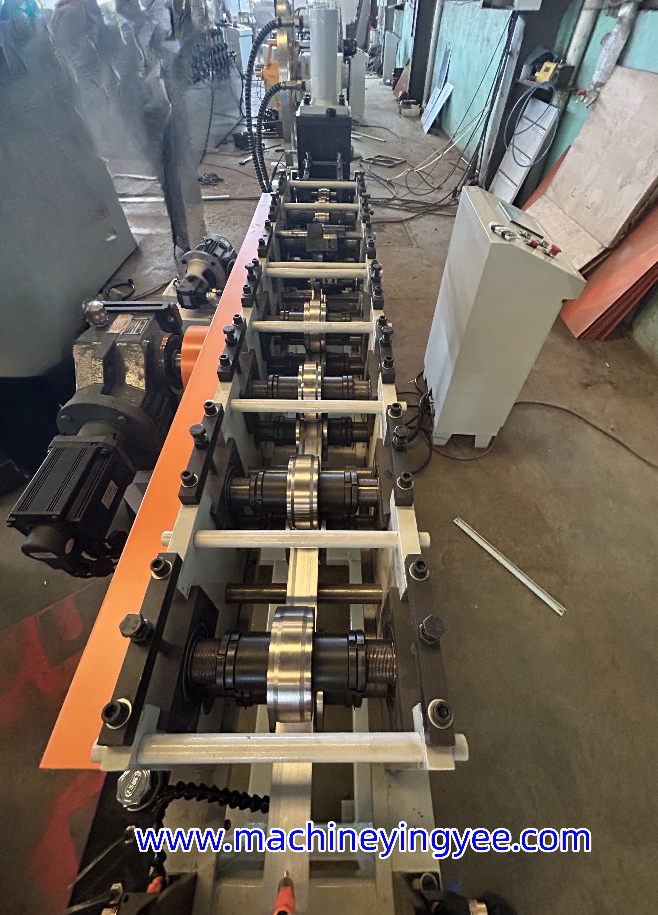
From an expertise standpoint, the beauty of cold bending technology is its relatively straightforward application despite its complex output. With minimal training, skilled technicians can operate these machines, achieving high-level precision that previously required extensive manual labor and experience. The machinery usually includes user-friendly interfaces, making it accessible to both new and seasoned operators.
Furthermore,
the versatility in the types of fenders that can be produced is unmatched. Whether you're looking to create custom fenders for a specific brand or a bespoke design that requires unique specifications, these machines deliver flexibility. Customizations are further supported by digital controls that facilitate exact measurements and replicate designs with impeccable accuracy.
semi truck fender cold bending machine
Industry experts regard semi truck fender cold bending machines as authoritative tools in the field of metal fabrication. Their implementation in shops and factories represents an investment in quality and reliability, both of which are paramount in establishing long-term client relationships. Being able to offer custom, precise solutions for semi truck fenders not only enhances the service profile of a business but also fortifies its reputation as a leader in automotive innovation.
Trustworthiness in this domain comes from the proven durability and reliability of the machines themselves. Industry reviews consistently highlight the longevity of these machines, with many models performing efficiently after years of continuous use. Moreover, manufacturers provide extensive warranties and support services, ensuring that businesses can maintain peak operational capacity with minimal downtime. This dedication to quality assurance further garners trust from operators and clients alike, knowing the products they are engaging with are of top-notch quality.
It's imperative that any purchasing decision is informed by thorough research and consultation with industry experts. When investing in a semi truck fender cold bending machine, businesses should consider factors such as the specific bending capabilities, the range of materials processed, and the overall build quality of the machine. Engaging with previous users or seeking testimonials can also provide actionable insights into the performance and reliability of different models.
In conclusion, semi truck fender cold bending machines represent a confluence of innovation and practicality. Their ability to produce durable, precision-engineered components enhances the operations within the automotive manufacturing and repair sectors. As the demand for bespoke and reliable parts continues to surge, these machines will undoubtedly play a crucial role in driving forward the capabilities and services of businesses worldwide. By investing in such advanced machinery, companies not only elevate their market position but also take significant steps toward a future where precision and customization are at the forefront of automotive design and repair.