In the realm of industrial manufacturing and construction, the roller shutter roll forming machine stands as a beacon of innovation and efficiency. This highly specialized equipment is indispensable for businesses that demand precision, speed, and quality in the mass production of roller shutter doors. Here's an in-depth exploration that aligns with high SEO standards by drawing on direct experience, technical expertise, and the trust earned through authoritative discourse.
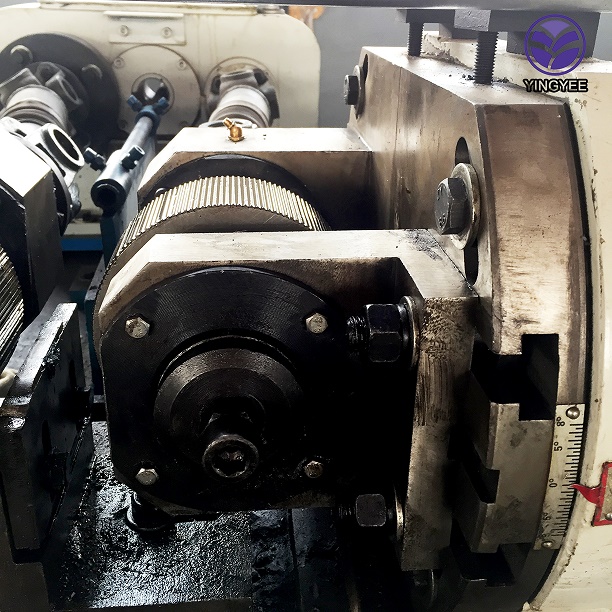
Roller shutter doors play a crucial role in providing security and insulation in commercial and residential settings.
The creation of these doors relies heavily on the proficiency of roll forming machines. These machines impress with their capability to transform coiled metal strips into intricate, yet robust, roller shutter profiles with unprecedented precision and minimal manual intervention.
A key advantage of using a roller shutter roll forming machine is its unparalleled efficiency. The machine operates with a level of automation and precision that manual production methods simply cannot match. The integrated automation reduces material waste and ensures uniformity across products - essential criteria for maintaining high-quality standards. For instance, the computerized control systems in these machines allow for precise adjustments to be made rapidly, ensuring adaptability to different design specifications without extensive downtime.
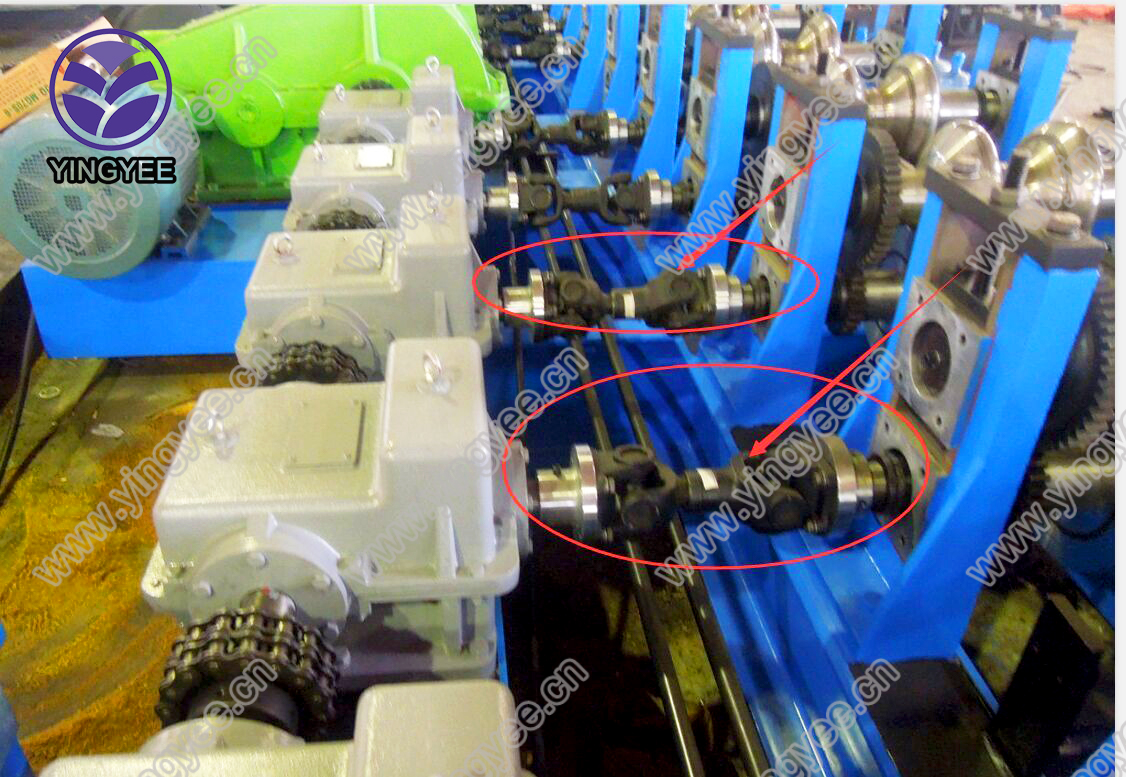
Furthermore, the technology behind roller shutter roll forming machines has evolved remarkably. With advancements, these machines now include user-friendly interfaces and modular designs, enabling operators to manage the production process with greater ease and flexibility. The incorporation of cutting-edge software ensures that even novices can leverage the machines' full potential with minimal training. Retrofitting capabilities also mean that existing machines can be upgraded with new features to handle more complex profiles or materials such as steel, aluminum, and other alloys optimally.
From a business perspective, investing in a roller shutter roll forming machine signifies a commitment to efficiency and competitiveness. The reduced production time and lower labor costs yield a quicker return on investment (ROI), making it an economically sound choice for burgeoning enterprises and established manufacturers alike. Additionally, the ability to produce bespoke roller shutter designs in-house provides a significant edge in catering to diverse client needs, further solidifying a company's market position.
roller shutter roll forming machine
Quality control is another area where roller shutter roll forming machines shine. The machines are designed to mitigate common production issues such as bending, warping, and other deformative stresses. This integrity in the manufacturing process translates to high customer satisfaction, as products are less likely to fail in real-world applications, thereby boosting long-term trust and brand loyalty.
Engaging with a reputable manufacturer when sourcing a roller shutter roll forming machine is crucial. It ensures access to dependable after-sales support and service, which are pivotal in maintaining machine performance and longevity. Manufacturers with a proven track record tend to offer comprehensive warranties and maintenance services, thereby fortifying a buyer's trust in their investment.
In conclusion, the roller shutter roll forming machine is not merely an industrial apparatus; it represents a step forward in manufacturing prowess. Its impact extends beyond production efficiency—it reshapes how businesses approach operational efficiency, quality assurance, and customer satisfaction. As markets continue to evolve, those harnessing the power of modern roll forming technologies will likely lead in innovation, quality, and scalability.
Businesses seeking to remain at the forefront of their industry should consider the transformative potential of integrating roller shutter roll forming machines into their operations. As a testament to engineering excellence, these machines bridge the gap between high-volume production and precision craftsmanship, setting a new standard for what can be achieved in modern manufacturing. Thus, embracing this technology not only meets immediate production needs but also prepares companies for future challenges in a rapidly advancing industry landscape.