In the evolving world of roadway infrastructure, the importance of ensuring safety through robust and reliable solutions cannot be overstated. A vital component in this context is the road safety barrier cold bending machine, an innovative product that has brought transformative changes to road safety manufacturing processes. With an emphasis on precision, efficiency, and durability, it stands as a testament to cutting-edge engineering and design.

A road safety barrier cold bending machine is specifically designed to produce high-quality, customized road safety barriers that are essential for accident prevention and vehicle restraint systems. With the increasing demand for safer roads, the expertise behind these machines is both sophisticated and paramount, stemming from an in-depth understanding of safety regulations and advanced manufacturing techniques.
Unlike conventional bending machines, the cold bending apparatus does not require heat treatment to shape metal. This advantage not only retains the metal's inherent strength but also allows for faster production cycles while minimizing energy consumption. This process ensures that the structural integrity of the barriers is uncompromised, an essential feature in maintaining the safety standards expected in today’s high-speed traffic environments.
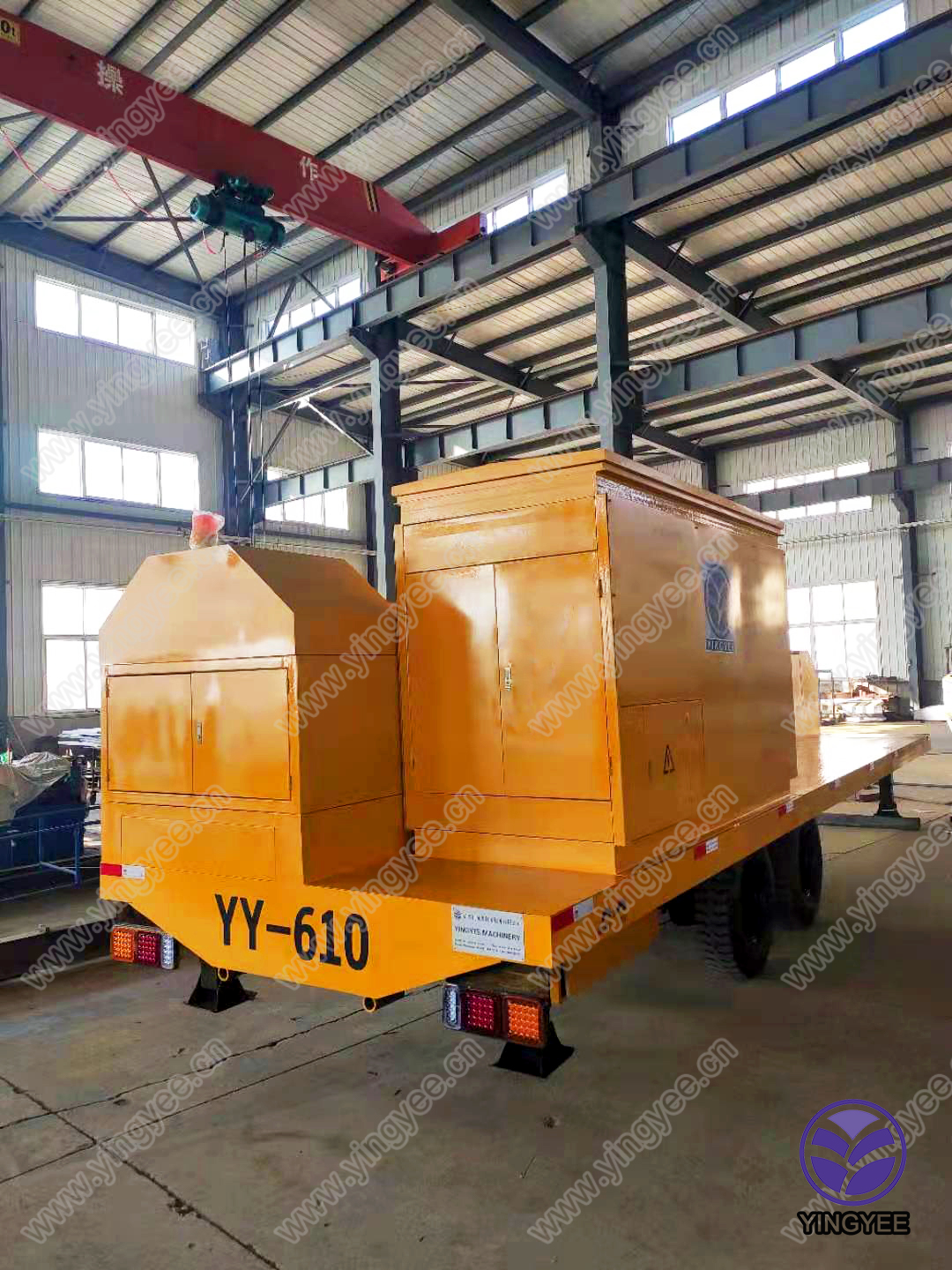
The engineering behind the road safety barrier cold bending machine showcases a convergence of technological prowess and authoritative knowledge in metallurgy and mechanical design. Equipped with computerized controls, these machines allow manufacturers to achieve precise angles and dimensions, accommodating various barrier specifications without extensive manual reconfigurations. This automation leads to increased trustworthiness in product consistency, a critical factor for road contractors and engineers who rely on dependable materials for their projects.
road safety barrier cold bending machine
A notable experience from several global deployments has highlighted the reliability and cost-effectiveness of these machines. For instance, during a highway expansion project in Australia, the deployment of cold bending machines drastically cut down production time, while meeting all necessary safety certifications. This kind of real-world validation underscores the trust placed in these products by industry experts and governmental agencies alike.
Furthermore, sustainability becomes a significant part of the conversation. By optimizing energy use and reducing waste through efficient production methods, the cold bending process aligns with global environmental standards. This is particularly crucial as industries across the board strive to minimize their carbon footprints. Expert operators of these machines can testify to their reduced operational costs and environmental impact, presenting a compelling case for their widespread adoption.
The authoritativeness of the suppliers and manufacturers of these machines is backed by extensive research and international quality standards such as ISO certifications. When businesses and governments consider investing in road safety solutions, the credibility of the manufacturing process and the equipment's compliance with rigorous industry standards become key deciding factors.
In conclusion, the road safety barrier cold bending machine is more than a piece of equipment; it is a critical investment in public safety and infrastructure resilience. As road networks globally are upgraded and expanded, the role of these machines in producing reliable, high-quality barriers will continue to grow. With their unmatched precision, energy efficiency, and adherence to safety standards, they represent the pinnacle of experience and expertise in the safety barrier production field.
This technological marvel not only enhances road safety but also embodies a future where innovation meets responsibility, ensuring safer travels for all.