In the realm of modern construction and architecture,
the process of metal deck cold bending plays a pivotal role in shaping the infrastructure landscape. A metal deck cold bending machine is an engineering marvel, providing the ability to shape and curve metal decks to meet specific structural demands. With a growing emphasis on sustainable and efficient construction practices, the technology and precision behind these machines have garnered significant attention.
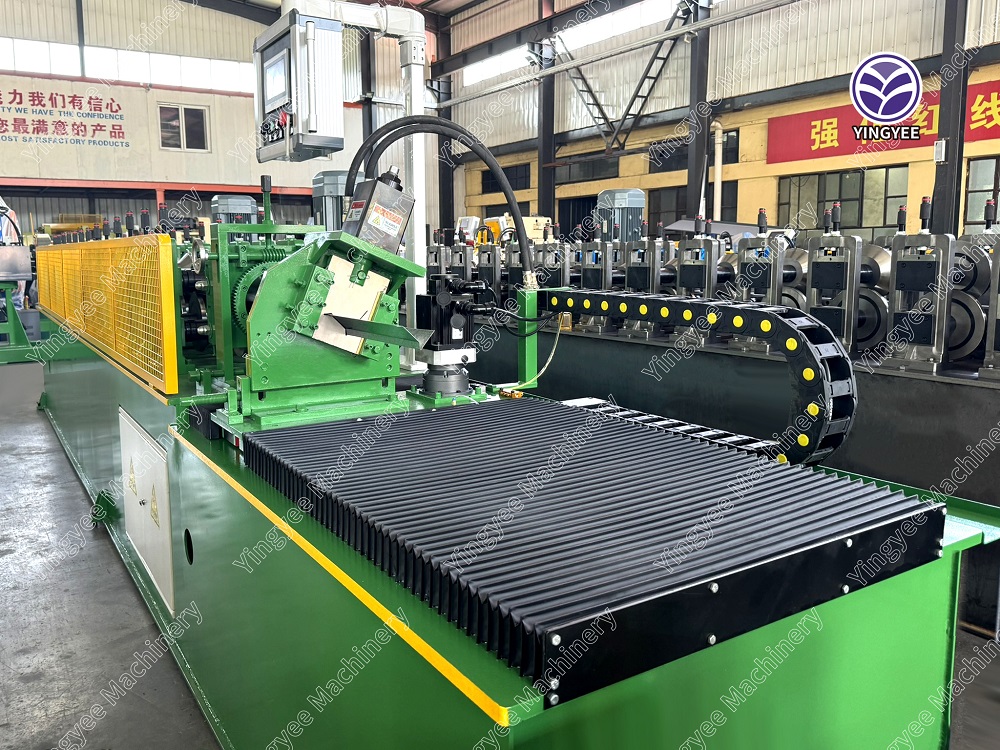
A professionally developed metal deck cold bending machine is essential for contractors aiming to excel in the industry. Its design is a product of extensive engineering research, assuring both longevity and high performance. Crafted with high-grade industrial materials, these machines are equipped to withstand the rigors of heavy workloads while maintaining accuracy and consistency in bending processes. This robust construction is supplemented by state-of-the-art precision control systems which allow operators to achieve exact bending parameters, critical for ensuring that the resultant metal decks meet stringent architectural and structural standards.
Typically, a metal deck cold bending machine operates using an advanced hydraulic system, providing the necessary force to manipulate metal sheets without the need for heating. This cold working process preserves the fundamental properties of the metal, maintaining its integrity and increasing its durability. The hydraulic mechanism, often interwoven with computer numerical control (CNC) technology, offers unparalleled precision. CNC systems facilitate the automation of cycle processes, enhancing production efficiency while drastically reducing the potential for human error. Expertise in programming and operating such machines is indispensable; operators must be versed in handling complex machinery and interpreting technical schematics and specifications.

Professionals utilizing these machines swear by their efficacy in producing components that conform to exact design criteria. These innovations allow for seamless integration into existing systems, adapting various lengths, thicknesses, and profiles to the user's needs, promoting customization and reducing wastage. Moreover, the cold bending technique minimizes the need for post-processing, saving on additional labor and material costs, thereby offering an economically viable solution for large and small-scale construction projects alike.
metal deck cold bending machine
The authority these machines command in the architecture and construction sectors is reflected in the trust industry leaders place in them. Esteemed construction companies prioritize investing in high-quality bending machines from reputable manufacturers renowned for their research, development, and stringent quality assurance protocols. Acquisition of such machinery often comes with comprehensive training and support packages, ensuring that operators are adept and confident in exploiting the full capabilities of the machines.
Industry trust extends beyond the machine itself; it also encompasses the services and maintenance offered by manufacturers. Regular servicing by certified professionals ensures the machinery remains in prime operational condition, minimizing downtime and extending the life of critical mechanical components. This dedication to service propagates user confidence, facilitating long-term partnerships between manufacturers and end-users. Certified pre-owned programs may also be offered, reinforcing trust through assurances of prior usage and excellent maintenance records.
Beyond the immediate technicalities and operational scope, the development and application of metal deck cold bending machines stand as testaments to human resourcefulness and commitment to innovation. As the construction landscape evolves towards more efficient, sustainable practices, the role of these machines is increasingly indispensable. They not only fulfill a practical need but also embody a reliance on advanced technology to push the boundaries of what is structurally possible, for buildings that are more durable, economical, and environmentally harmonious.
In conclusion, investing in a metal deck cold bending machine is more than acquiring a tool; it is an endorsement of an ecosystem of innovation, expertise, and trusted collaboration. It embodies a significant leap toward sustainable architectural advancements, propelled by precision engineering that meets the highest industry standards, promising enduring results and unwavering reliability.