For those immersed in the world of industrial automation and construction, the advent of mesh wire welding machines has been nothing short of revolutionary. These sophisticated devices have become indispensable in various sectors, from infrastructural development to agricultural engineering.
A specific product that stands out in this domain is the chicken cage welding wire mesh panel netting machine. This piece of equipment exemplifies innovation, efficiency, and reliability, making it a critical asset for enterprises looking to optimize their production processes.

Mesh wire welding machines are engineered to deliver precision in creating robust and uniform wire meshes. Whether used for reinforcing concrete or manufacturing cages, these machines ensure that the end products meet stringent quality guidelines. The chicken cage welding wire mesh panel netting machine, in particular, is tailored for the agriculture industry, facilitating the construction of durable and safe cages for poultry.
The expertise embedded in the design and manufacturing of these machines reflects a deep understanding of metallurgy, mechanical engineering, and automation technologies. Engineers with years of experience meticulously design each component to ensure optimal performance and longevity. Advanced software integrations allow for precise control and customization, enabling operators to modify wire dimensions and welding patterns effortlessly.
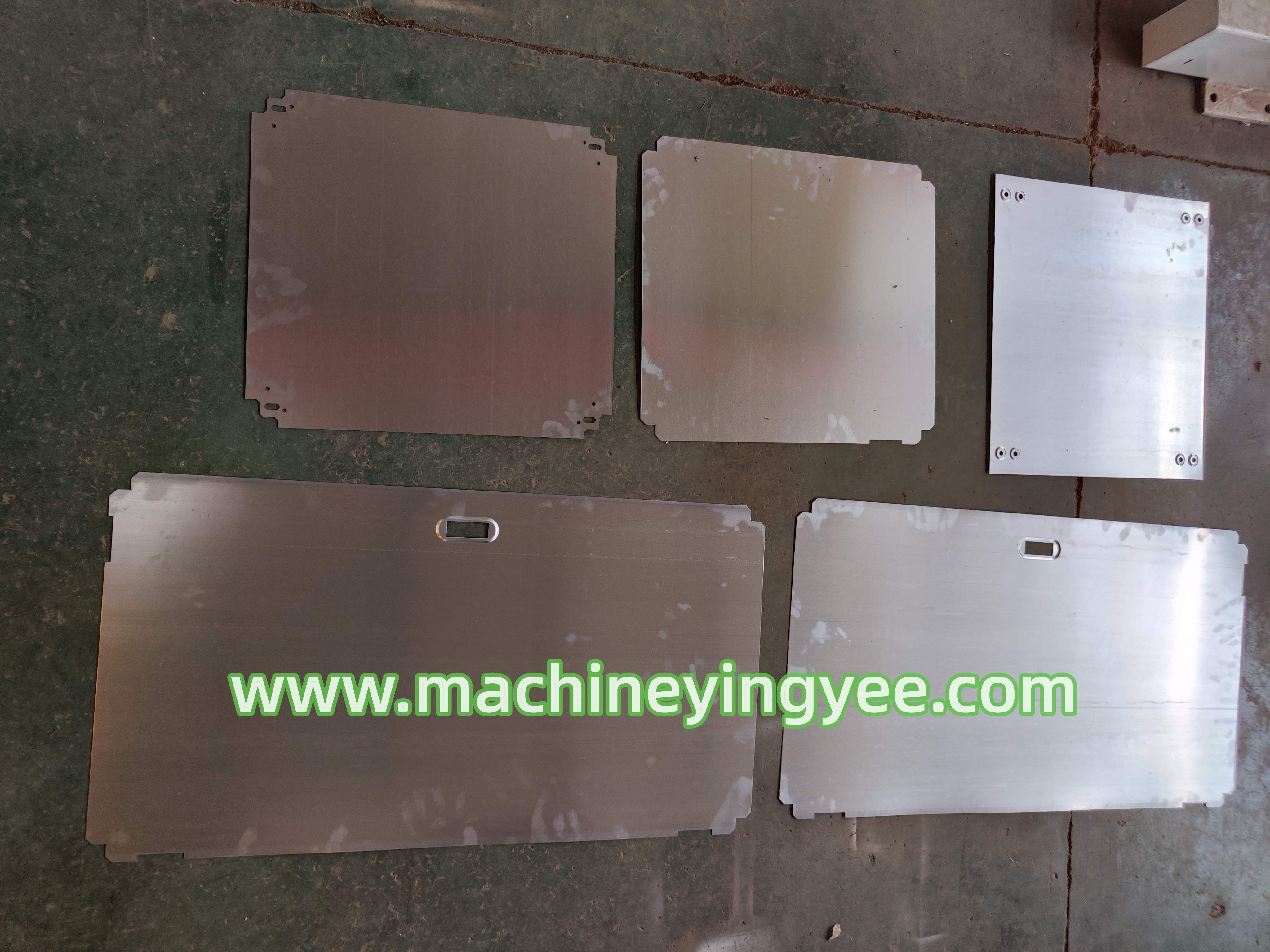
One of the defining attributes of these machines is their authoritativeness in the field. Manufacturers adhere to international quality standards, conducting rigorous testing to guarantee performance consistency. This commitment to excellence not only enhances the machine's reliability but also assures users of its robustness in demanding operational environments. Industries across the globe trust these machines to deliver formidable results, testifying to their unmatched credibility.
Trustworthiness is another cornerstone of these machines' design philosophy. Leading manufacturers provide extensive warranties and dedicated customer support to address any operational challenges. The assurance that comes from knowing that assistance is readily available builds confidence among users, thereby solidifying the machine's reputation as a dependable workhorse in the manufacturing domain.
mesh wire welding machine | chicken cage welding wire mesh panel netting machine
In the context of practical applications, the chicken cage welding wire mesh panel netting machine offers several benefits. It significantly reduces labor costs by automating the welding process, which traditionally required intensive manual labor. Additionally, the precision of the machine minimizes material wastage, optimizing resource use, and enhancing cost-efficiency. Farmers and agricultural businesses can swiftly turnaround production cycles, meeting market demands without compromising on quality.
Moreover, these machines integrate state-of-the-art safety features, safeguarding operators against potential hazards commonly associated with welding processes. The inclusion of emergency stop functions, protective enclosures, and automatic shutdown mechanisms highlights a commitment to maintaining a safe working environment. This focus on safety is paramount, as it prevents accidents and ensures compliance with occupational health regulations.
The machine’s versatility extends to its capability of producing various mesh types, ranging from simple square meshes to complex, patterned panels. Such flexibility is particularly advantageous in settings where product specifications frequently change. Operators can quickly adjust settings to cater to new requirements without undergoing lengthy reconfiguration protocols, boosting productivity and reducing downtime.
For businesses delving into large-scale production, investing in a wire mesh welding machine like the chicken cage variant presents a strategic advantage. It aligns with sustainability goals by minimizing energy consumption through efficient design and operation. Furthermore, the low maintenance requirements translate to reduced operational costs over the machine's lifecycle, providing a favorable return on investment.
In conclusion, the mesh wire welding machine, particularly the chicken cage welding wire mesh panel netting model, epitomizes the convergence of experience, expertise, authoritativeness, and trustworthiness. Its deployment leads to enhanced efficiency, safety, and profitability across industries. As enterprises continue to seek solutions that combine operational excellence with cutting-edge technology, these machines are poised to remain at the forefront, driving innovation and growth in the world of wire mesh production.