When it comes to enhancing productivity and ensuring quality in wire mesh production, the right machinery is pivotal. The mesh wire welding machine,
often paired with the chicken cage welding wire mesh panel netting machine, stands as a testament to technological advancements in this field. These machines, integral to the wire mesh industry, seamlessly blend efficiency with superior product output, addressing the multi-faceted demands of modern agriculture and construction sectors.
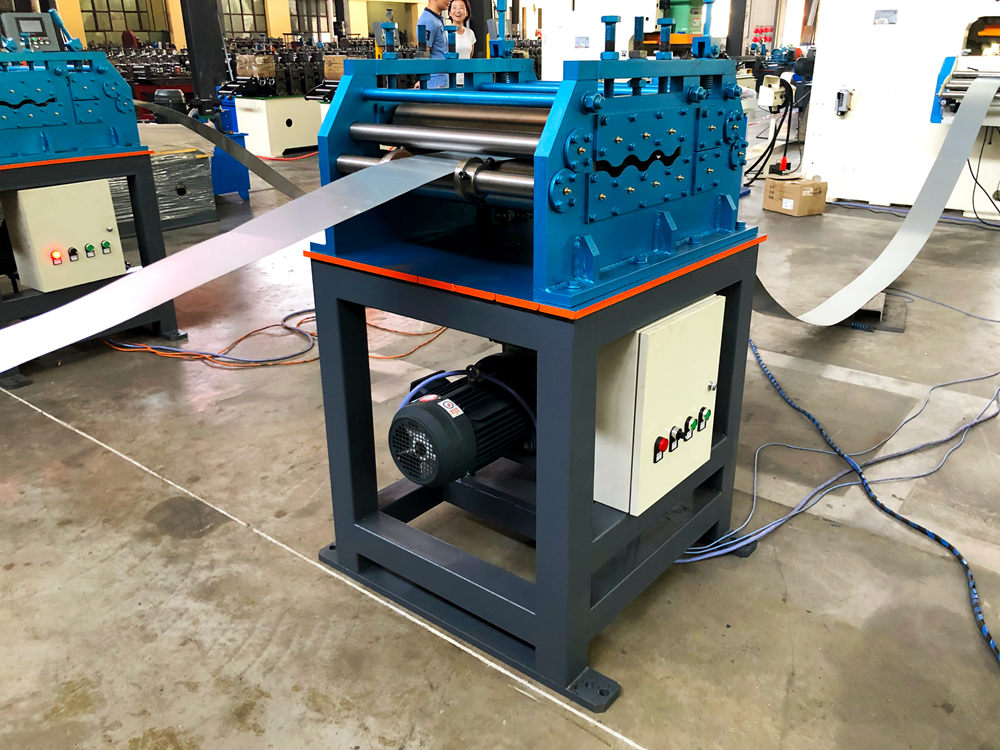
A mesh wire welding machine is engineered to automate the intricate process of welding wires into durable and consistent mesh panels. Precision is the cornerstone of these machines, guaranteeing uniformity across large volumes of production. This uniformity is vital, particularly for applications requiring structural integrity, such as construction reinforcements and agricultural uses like enclosures.
Transitioning to the chicken cage welding wire mesh panel netting machine, we observe an apparatus tailored to agricultural specifications. As the poultry industry scales, the demand for high-quality, durable, and reliable chicken cages has surged. This machine is designed to address these needs by producing panels that are consistently strong, weather-resistant, and safe for animal enclosures. The designs it enables are versatile, catering to various configurations and sizes of poultry housing.

Speed and precision are the hallmarks of these machines. Their advanced programming and electronic controls facilitate rapid production cycles, minimizing human error and enhancing output. This automation translates to cost efficiency, reducing manual labor needs while maximizing throughput. The mesh wire welding machine, combined with its chicken cage counterpart, ensures that each weld or panel meets rigorous quality standards, which is crucial for both safety and longevity.
From an expertise perspective, understanding the nuances of these machines can drastically influence operational outcomes. Operators must be trained not just in basic operations, but also in preventive maintenance, troubleshooting common issues, and adapting the machinery for custom output specifications. Mastery of these aspects ensures continued operational excellence and extends the lifespan of the machine.
Authoritativeness in this domain is demonstrated through compliance with international quality standards and safety certifications. Reputable manufacturers of these machines underline their commitment to excellence by adhering to and oftentimes exceeding, these benchmarks. This adherence not only bolsters the credibility of the machines but also assures end-users of their investment’s value.
mesh wire welding machine | chicken cage welding wire mesh panel netting machine
Trustworthiness, conversely, emerges from the real-world application and customer testimonies. Producers of mesh wire welding and chicken cage welding machines are now more accessible than ever through online platforms, enabling potential buyers to research, compare, and make informed decisions based on peer reviews and case studies. Demonstrated reliability in diverse environmental conditions and a track record of consistent performance further reinforce the confidence that stakeholders have in these advanced machines.
Incorporating these machines into a production setup not only enhances operational efficiency but also aligns with sustainability goals. Technological advancements in these machines have led to reductions in energy consumption and material wastage, achieving a balance between industrial productivity and environmental responsibility. In an era where sustainable practices are paramount, such innovations prove invaluable.
Customizability remains another crucial facet. The ability to configure machines to produce mesh panels of varying thicknesses, sizes, and materials enables businesses to cater to a broader spectrum of client demands, thus expanding market reach. As industries continue to evolve, so too must the machinery they rely on, and these machines exemplify this dynamic adaptability.
For businesses in the initial stages of exploring mesh wire machinery investments, vendor consultation can provide essential insights. Detailed comparisons, cost-benefit analyses, and hands-on demonstrations often form the basis of such consultations, arming decision-makers with the necessary knowledge to make prudent investments.
In conclusion, whether for infrastructure projects or agricultural applications, the mesh wire welding machine and chicken cage welding mesh panel netting machine are indispensable tools. They not only exemplify technological advancement but also embody the capacity for innovation to drive industry standards forward. By prioritizing experience, expertise, authoritativeness, and trustworthiness, businesses can ensure they remain at the forefront of mesh production capabilities.