Navigating the realm of large span roll forming machines unveils a world of advanced engineering solutions tailored for robust industrial applications. These machines, integral to the production of long, metallic profiles, find profound utility in sectors ranging from construction to automotive manufacturing. To the industrial operator and mechanical engineer alike, understanding the nuances of large span roll forming machines is paramount for optimizing both performance and output.
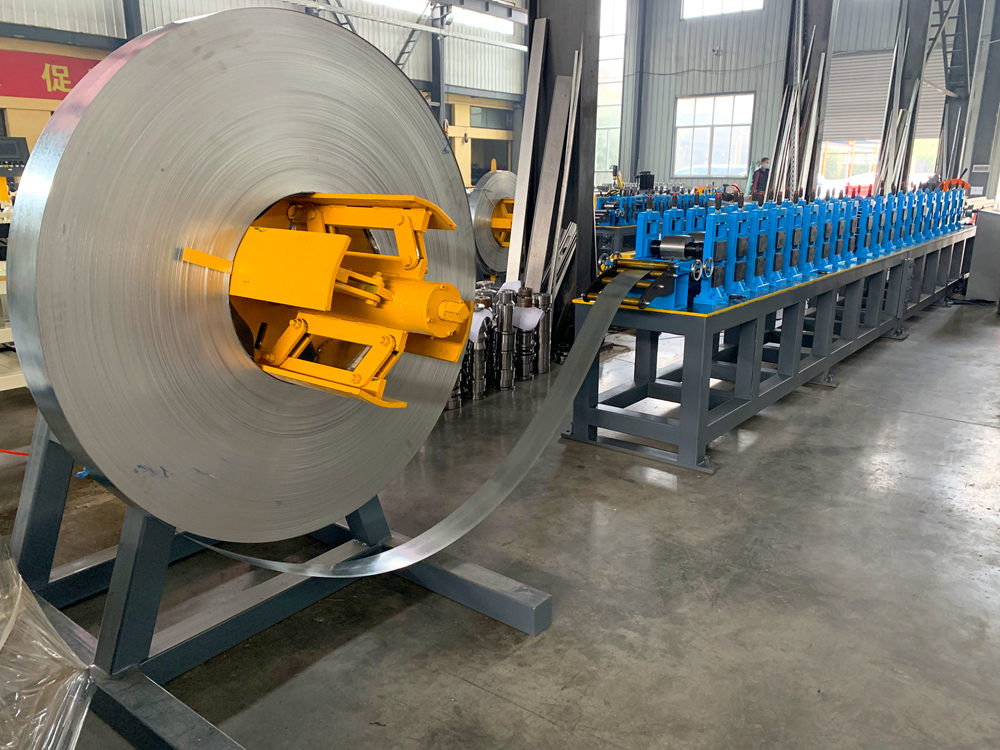
Large span roll forming machines are distinguished by their capacity to handle extensive widths and lengths of metal sheets, typically used to create structural sections, roof panels, and even automotive components. Unlike smaller, conventional roll forming machines, these are designed to accommodate significant material dimensions, which necessitates a sophisticated understanding of mechanical engineering and material science.
In my extensive experience within the mechanical engineering domain, it’s evident that the large span roll forming machine is not only about size but precision. The key to maximizing the efficacy of these machines lies in their setup and calibration. Ensuring the alignment and proper tension of the rollers can drastically affect the quality of the finished product. Misalignments might lead to undesirable stresses and product inconsistencies, which can result in costly downtimes and material waste.
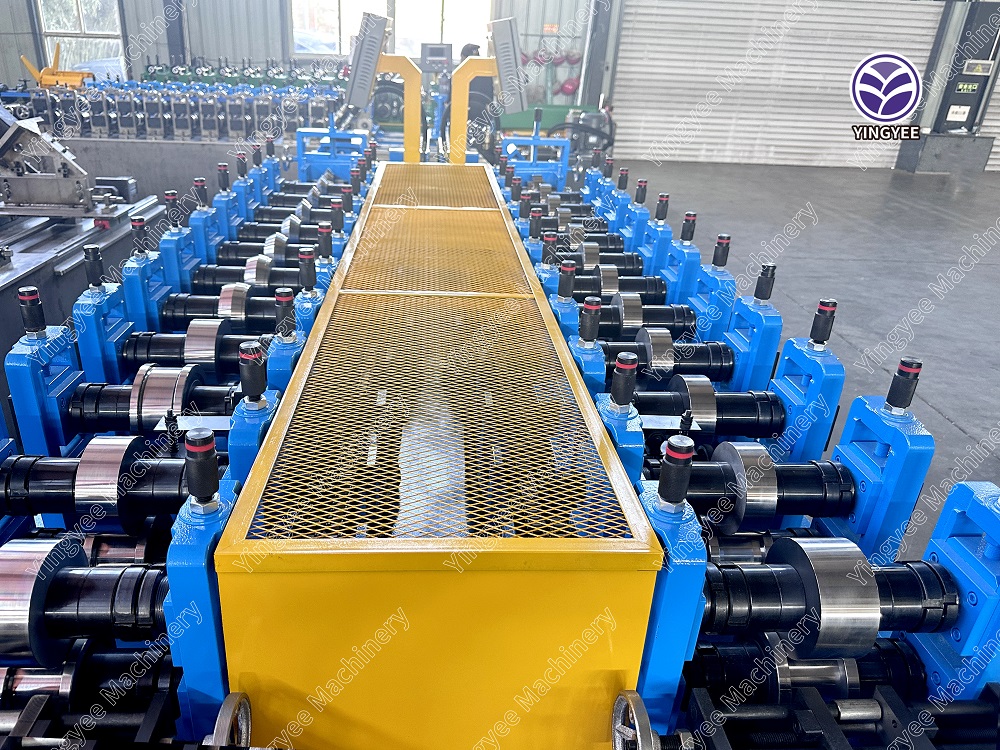
Moreover, expertise in material properties is essential. Different metals behave uniquely under stress and bending; for instance, steel requires distinct pressure compared to aluminum or copper. As an expert, one must be adept at adjusting the machine settings in response to varying material specifications. The correct application of lubricant and understanding its effect on the metal surface can further enhance the machine's efficiency.
large span roll forming machine
Authoritative guidance suggests that regular maintenance and using the latest technological enhancements are crucial. Modern large span roll forming machines are equipped with advanced diagnostics and software for real-time monitoring, which ensures any deviations in operation are swiftly addressed. This highlights the machine’s reliance not only on robust mechanical components but also on cutting-edge software support to maintain operational integrity.
Trust in large span roll forming machines, as with any significant industrial investment, is built over time through demonstrated quality and reliability. Brands that provide comprehensive training for operators and offer accessible service support tend to establish this trust quickly. A well-rounded understanding of both the mechanical aspects and the digital interfaces of these machines can drastically reduce learning curves and enhance operational efficiencies.
Finally,
the economic aspect cannot be ignored. When investing in large span roll forming machines, consider the total cost of ownership rather than the initial purchase price. Energy consumption efficiency, ease of maintenance, and the availability of spare parts play crucial roles in determining the machine's long-term value. In my experience, stakeholders who invest time in evaluating these parameters often enjoy greater profitability and reduced operational risks.
In conclusion, optimizing the use of large span roll forming machines requires a confluence of experience and expertise. A detailed comprehension of material dynamics, coupled with mastery over machine specifics, positions industry professionals to leverage these engineering giants for maximum industrial productivity. As technological advancements continue to evolve, staying informed and adaptable will ensure these machines serve as reliable assets in any industrial framework.