In the rapidly evolving world of industrial manufacturing, the IBR roof sheet forming machine stands out as a pivotal tool that shapes the way we approach roofing solutions. With its impressive capabilities and innovative design, this machine not only enhances the efficiency of production but also sets a benchmark for durability and quality in the roofing industry.
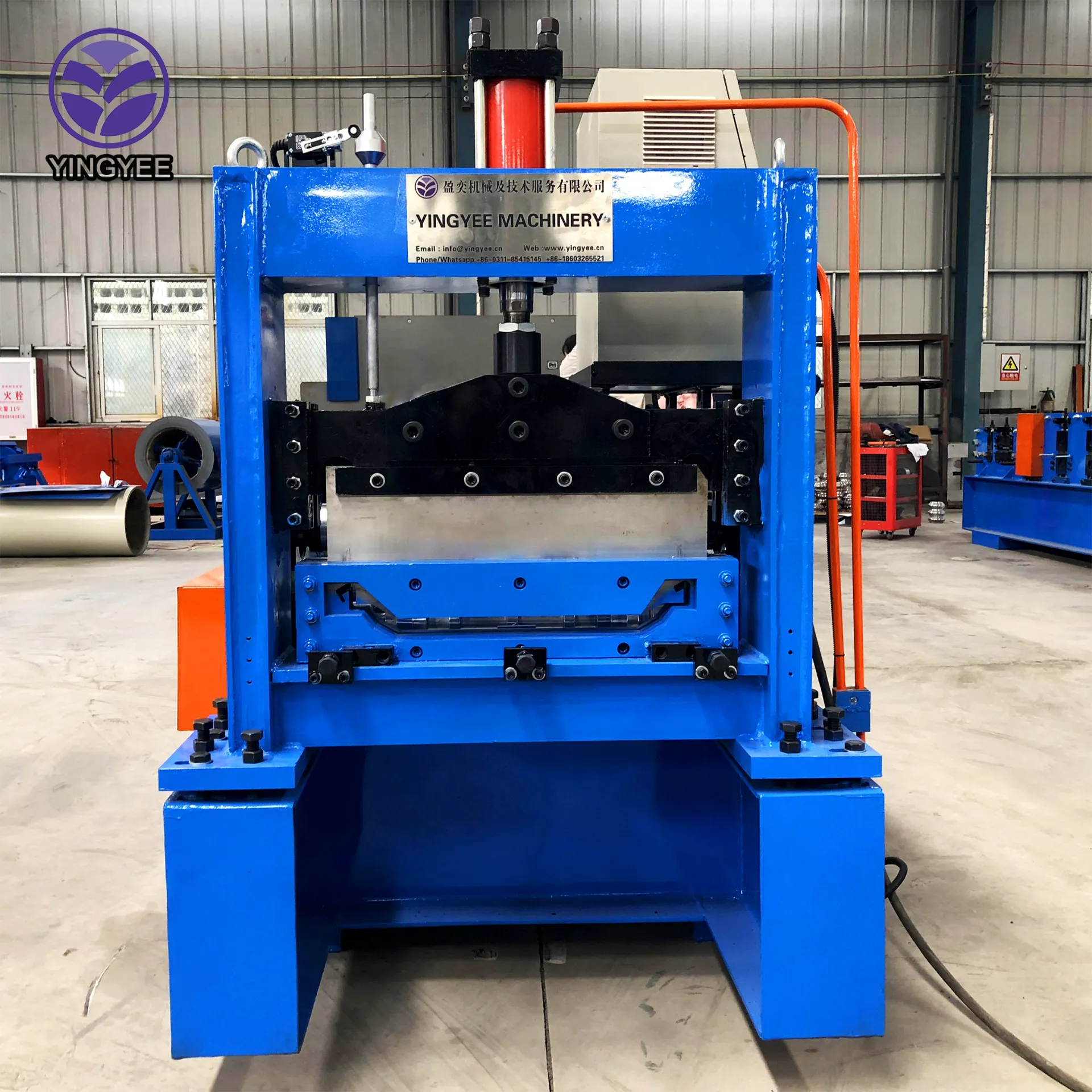
As an expert in the field with years of hands-on experience, I've witnessed firsthand the transformational impact of integrating an IBR roof sheet forming machine into production lines. This machine excels in converting coils of steel into perfectly profiled IBR sheets, which are renowned for their structural strength and aesthetic appeal. This transformation process is crucial in a market that demands both functionality and superior design.
From a professional standpoint,
one of the most remarkable features of the IBR roof sheet forming machine is its adaptability. Whether for small-scale operations or large manufacturing setups, its versatility allows operators to customize profiles and dimensions to meet specific client requirements. This adaptability is not just about varying sizes but also involves the machine's ability to process different materials, including galvanized steel and even coated materials, without compromising on the quality or finish of the final product.
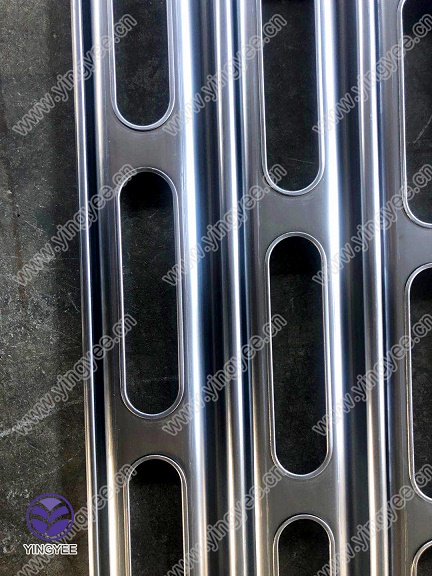
Authority in the manufacturing industry is reinforced by the repeated success stories stemming from the use of such machines. Companies leveraging these machines have reported a significant reduction in material wastage, which not only contributes to cost efficiency but also supports sustainable manufacturing practices. The precision and reliability afforded by these machines ensure that each sheet produced adheres to global standards of roofing excellence.
ibr roof sheet forming machine
Experience has proven that operating and maintaining an IBR roof sheet forming machine does not require excessive expertise, which is a testament to its user-friendly nature. Training sessions provided by manufacturers often encompass all necessary skills, enabling operators to quickly adapt and maintain high production standards. This ease of use can be attributed to well-designed control systems that often include automated settings for different profiles and thicknesses, further minimizing the margin for error.
Trust in the IBR roof sheet forming machine is earned through consistent and reliable performance across various demanding situations. Its robust build is engineered to withstand the rigors of daily use, ensuring longevity and reduced downtime. Regular maintenance, advised by manufacturers, typically suffices to keep these machines operational for years, confirming their status as a dependable asset for any business in the roofing industry.
Furthermore, the integration of modern technologies, such as computerized control and advanced material feeding systems, has enhanced the capability of these forming machines. Such innovations not only streamline the production process but also facilitate seamless integration with existing production systems, further asserting the machine's authoritative position in contemporary manufacturing contexts.
In conclusion, the IBR roof sheet forming machine is more than just a tool—it's a bridge to the future of efficient and sustainable roofing solutions. Its blend of adaptability, reliability, and advanced technological integration makes it an indispensable part of modern manufacturing practices. For businesses aiming to excel in the competitive arena of roofing materials, investing in an IBR roof sheet forming machine represents a commitment to quality, efficiency, and innovation. With these attributes securely in place, companies are well-positioned to meet both current demands and anticipate future trends in the roofing industry.