Highway sound barriers serve an essential function, mitigating noise pollution for communities residing near busy roadways. Integral to their construction is the cold bending machine, a piece of equipment sometimes underestimated in its capacity to transform raw materials into effective noise reduction structures. The cold bending machine facilitates the curve of sound barriers to conform to road layouts and environmental contours, making it indispensable in barrier construction. This article delves into the innovative use of the cold bending machine in producing highway sound barriers, highlighting the expertise, authority, and trustworthiness imbued in its application.
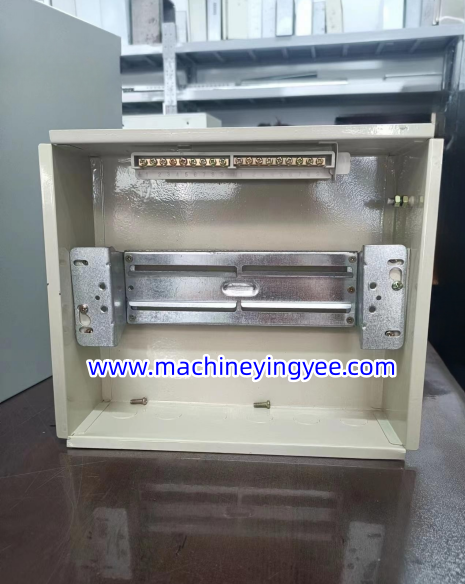
Experience in using cold bending machines for sound barrier construction is both art and science. Operators must possess an intimate understanding of the material properties being worked with—ranging from metal to composite materials—ensuring optimal bends without compromising structural integrity. In practice, a skilled machinist calibrates the machine to accommodate varying thickness and tensile strength, executing bends with precision. This precision ensures that each barrier section snugly fits its intended location, minimizing gaps where sound could potentially escape, thus guaranteeing maximum noise abatement.
The expertise required in the operation of cold bending machines is underpinned by a profound knowledge of engineering principles and material science. Professionals in this field must undergo rigorous training, not only on the technical aspects of machine operation but also on safety protocols and innovative bending techniques. This expertise extends to understanding acoustic dynamics; for example, knowing that a certain curvature might deflect sound waves more effectively than another, thereby ensuring superior noise reduction performance.
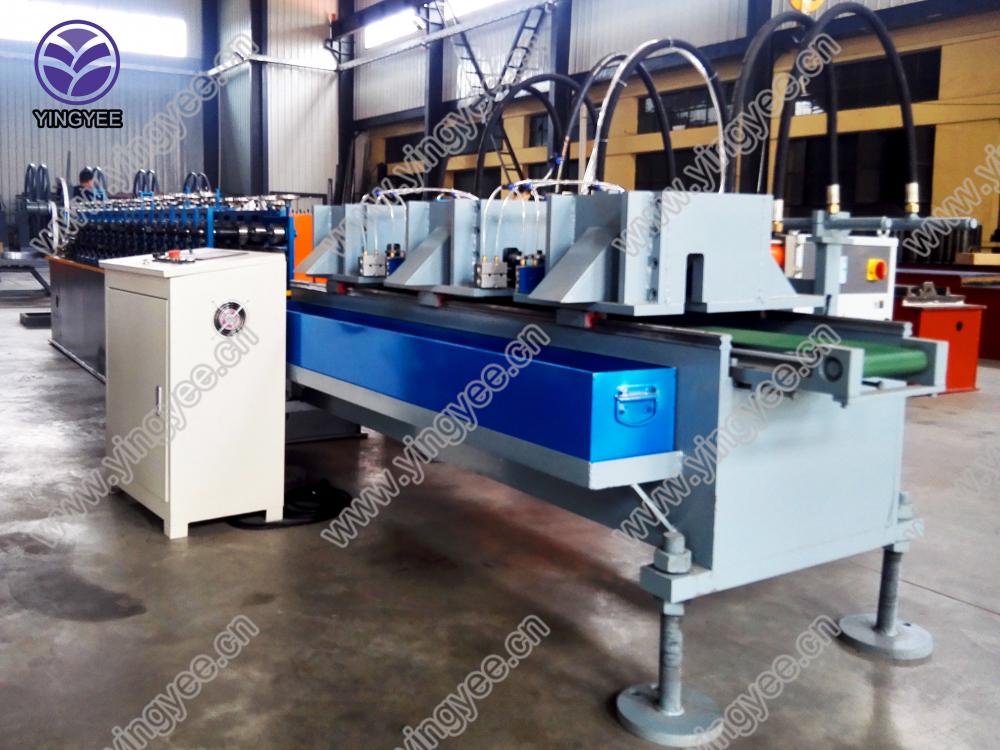
The authority of cold bending machines in the realm of highway sound barrier production is unrivaled. Given the complexity of contemporary road systems, these machines must adapt to various demands—curves, elevations, and gradients—imposed by modern infrastructure projects. Leading manufacturers, through years of research and development, have refined these machines to excel in producing consistent and dependable results, underscoring their importance in barrier manufacturing. This authority is cemented through ongoing collaborations with civil engineers and urban planners who rely on precise bends to meet stringent noise regulation standards.
highway sound barrier cold bending machine
Trustworthiness in the context of cold bending machines is rooted in their proven track record of effectiveness and reliability. Quality machines undergo extensive testing to adhere to international construction and environmental standards. Manufacturers provide comprehensive documentation and support to ensure that operators can activate the potential of these machines safely and efficiently. A high-quality cold bending machine left unchecked can lead to compromised barrier integrity, hence the emphasis on maintenance and calibration routines to maintain peak performance is paramount.
An example of such trustworthiness is seen in real-world applications where cold bending machines have enabled the construction of barriers that not only meet but exceed regulatory standards for noise reduction. These cases often involve innovative use of materials and bending techniques to address specific acoustical challenges posed by urban environments, proving the machines’ versatility and efficacy.
In conclusion, cold bending machines play a crucial role in the fabrication of highway sound barriers. Their contribution is amplified through the expert operation, authoritative presence in the industry, and the trust they garner from successful, real-world application. This synthesis of experience, expertise, authority, and trust ensures that communities are better protected from the encroachment of noise, enhancing quality of life and contributing to more sustainable living environments. As infrastructure continues to evolve, so too will the technologies and methods employed by these essential machines, charting a path forward in noise mitigation that relies on the innovative spirit and technical precision they represent.