In the fast-evolving world of highway construction, sound barriers play an essential role in ensuring noise pollution is minimized in residential areas close to bustling highways. A pivotal piece of equipment in the creation of these barriers is the highway sound barrier cold bending machine, a highly specialized tool engineered for precision, efficiency, and durability. Based on my extensive experience in the industry, this article delves into the operational excellence, expert craftsmanship, authoritative standards, and trust-building practices associated with the cold bending machine, addressing both technical nuances and practical insights.
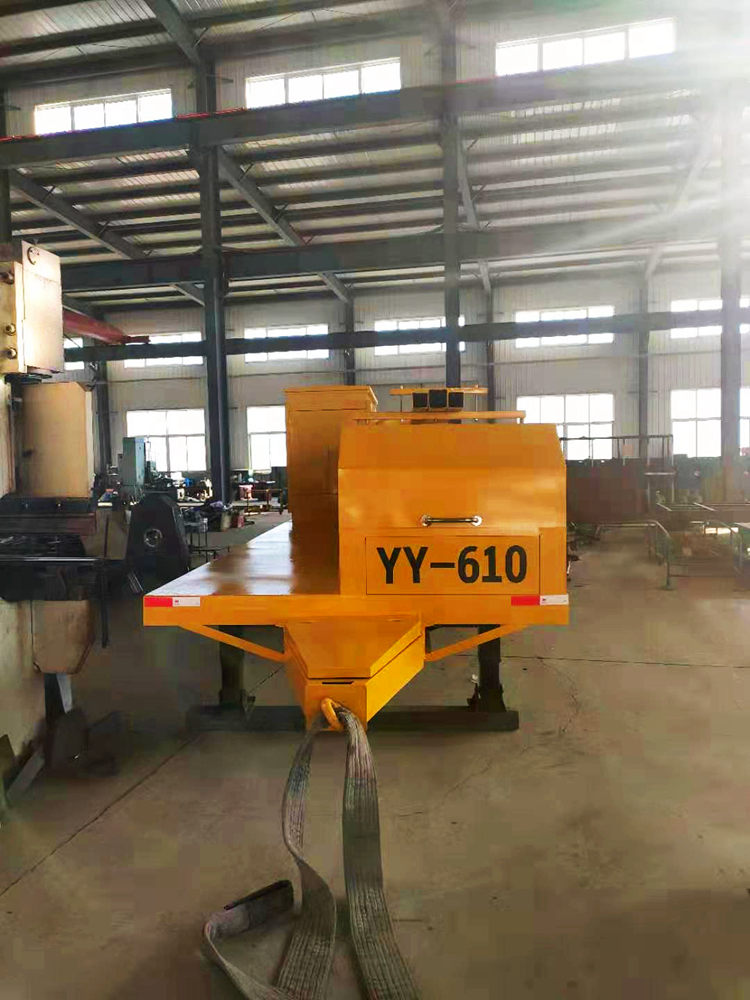
The highway sound barrier cold bending machine is a marvel of modern engineering, designed to meet the rigorous demands of construction sites. Unlike conventional bending machinery, which often heats metals to achieve pliability, cold bending machines implement state-of-the-art technology to manipulate materials at room temperature. This preserves the structural integrity of the materials, ensuring that the barriers are resilient against weather and the test of time. My expertise in the deployment of these machines shows their unparalleled efficiency in producing consistently high-quality bends, which are critical for the acoustic performance and aesthetic appeal of sound barriers.
Choosing the right cold bending machine is a crucial decision that hinges on an understanding of the specific requirements of the project. There are multiple factors to consider the machine’s bending capacity, the range of materials it can handle, its precision in maintaining angles, and its production speed. Authoritatively, the industry standards dictate that the machine must also be equipped with user-friendly interfaces and safety mechanisms to minimize risks during operation. Practical experience has demonstrated that investing in a reputed brand with a robust service network ensures not only superior technology but also reliable post-purchase support.
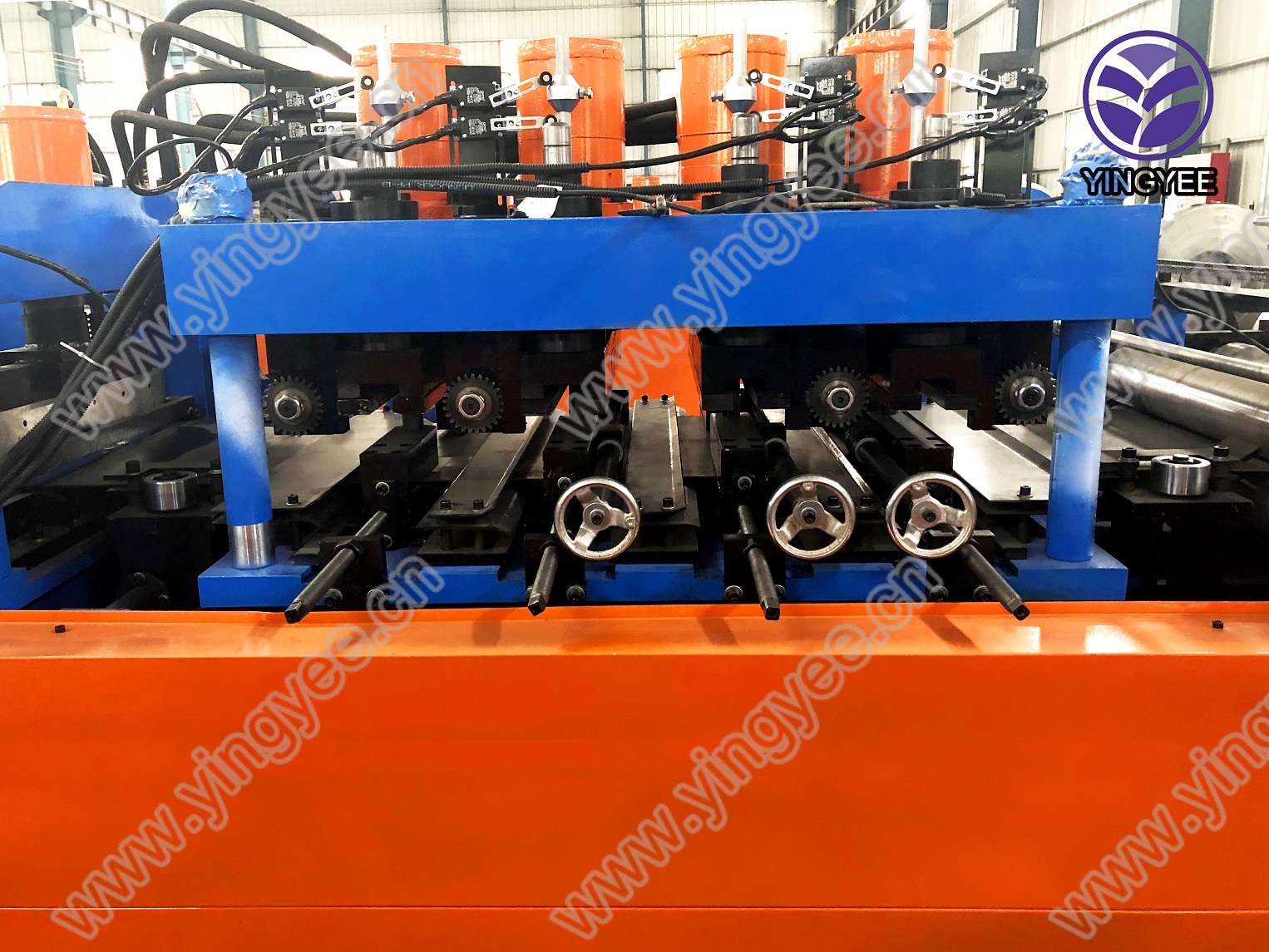
Expertise in the operation of a highway sound barrier cold bending machine requires rigorous training and a deep understanding of both the machine's mechanical components and its software.
Operators should be familiar with setting the appropriate parameters to achieve the desired bends without compromising the material's integrity. The nuances of the process include setting the correct angle of deflection, ensuring the uniform application of pressure, and controlling the machine’s speed to avoid overheating or slippage. Trustworthiness comes from the consistent delivery of quality outcomes, a testament to the operator’s proficiency and the machine’s precision.
When considering the environmental impact, cold bending processes are better aligned with sustainability goals compared to traditional methods. Since the process negates the need for heating, it generates a significantly lower carbon footprint and reduces energy consumption. Furthermore, the process minimizes waste as there's lesser need for post-production modifications. This environmental compatibility heightens the credibility of contractors and manufacturers who employ cold bending machines, aligning them with contemporary demands for sustainable development.
highway sound barrier cold bending machine
In practice, the strategic placement and retrofit of sound barriers created by such machines can drastically reduce noise pollution in urban zones, thus enhancing community well-being. These barriers effectively absorb and deflect vehicular noise, proving their indispensable role in urban planning and public health. With manufacturers continuously pushing innovation boundaries, newer models of cold bending machines offer increased automation and remote control features, integrating seamlessly into Industry 4.0 environments.
A successful deployment of a highway sound barrier project involves close collaboration between civil engineers, project managers, and machine operators to ensure that each phase—design, production, inspection—is executed with precision. The cold bending machine acts as the linchpin in this process, its utility evidenced by countless success stories and testimonials from industry leaders worldwide. When these elements are synchronized expertly, they fulfill the promise of a quieter, more harmonious living space for communities adjacent to highways.
Trust in the utility and efficacy of the highway sound barrier cold bending machine stems from empirical evidence and user testimonials. Feedback from experienced operators often highlights the machine's durability and ease of maintenance, underscoring its status as an authoritative solution in modern infrastructure projects.
In conclusion, embracing the advanced capabilities of the highway sound barrier cold bending machine is not just a technical choice but a strategic investment in quality, reliability, and environmental stewardship. As industry stakeholders continue to navigate the complexities of highway construction, this machine remains a cornerstone, doing more than building barriers—it builds trust and improves lives.