The High Frequency Tube Mill A Revolutionary Step in Precision Manufacturing
In the world of precision manufacturing, the quest for improved accuracy and efficiency is never-ending. The advent of the high frequency tube mill has been a significant breakthrough in this pursuit. This innovative machine tool incorporates advanced technology to deliver unparalleled precision and productivity in the fabrication of tubular products.
At its core, the high frequency tube mill operates on the principle of electromagnetic induction heating. This process involves passing an alternating current through a coil that surrounds the metal tube, inducing eddy currents within the material. These currents generate heat as they encounter resistance from the tube's molecules, causing the metal to quickly reach its forging temperature. This rapid heating method ensures a uniform temperature distribution across the tube's surface, which is crucial for maintaining consistent material properties during deformation.
One of the primary advantages of the high frequency tube mill is its energy efficiency. Compared to traditional furnace heating methods, induction heating targets only the material being processed, reducing energy waste and lowering production costs. Additionally, the speed at which the tube can be heated and cooled down significantly shortens the overall cycle time, increasing throughput without sacrificing quality.
The precision control afforded by the high frequency tube mill is also noteworthy. The machine's sophisticated computer numerical control (CNC) system enables operators to input exact specifications for each tube, ensuring repeatable results with minimal deviation The machine's sophisticated computer numerical control (CNC) system enables operators to input exact specifications for each tube, ensuring repeatable results with minimal deviation
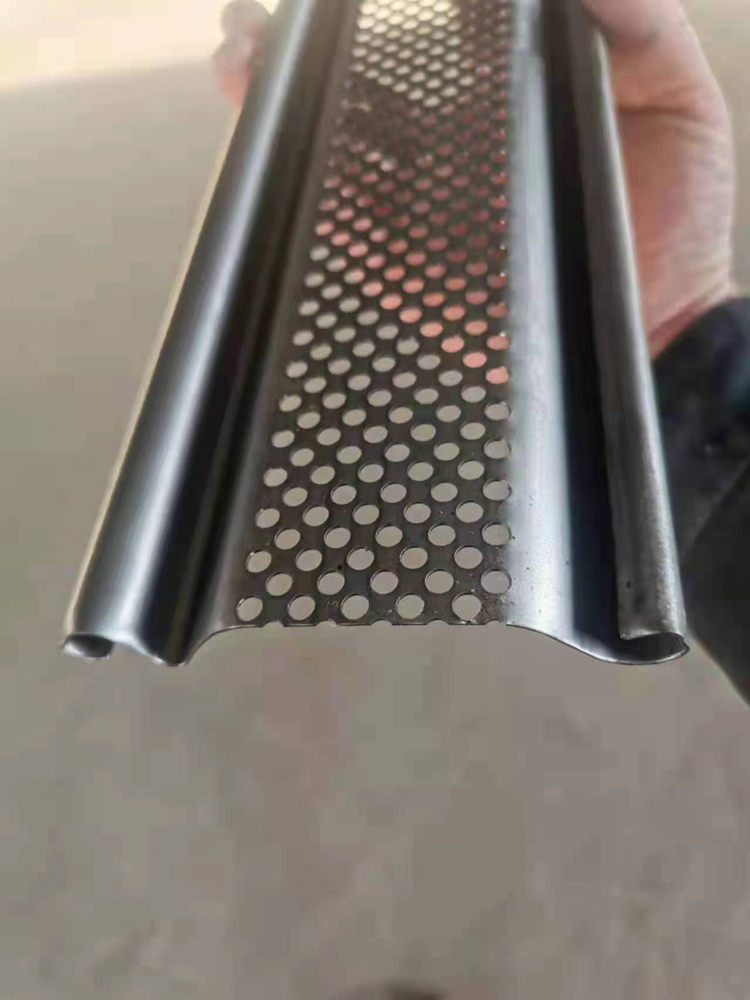
The machine's sophisticated computer numerical control (CNC) system enables operators to input exact specifications for each tube, ensuring repeatable results with minimal deviation The machine's sophisticated computer numerical control (CNC) system enables operators to input exact specifications for each tube, ensuring repeatable results with minimal deviation
high frequency tube mill. From diameter to wall thickness, every parameter can be finely tuned to meet stringent industry standards.
Furthermore, the high frequency tube mill opens up possibilities for complex geometries and alloys that were once challenging to work with. Its ability to handle high-temperature materials and create intricate shapes expands the design envelope for engineers, fostering innovation in industries ranging from automotive to aerospace.
However, like any technology, the high frequency tube mill requires skilled operators and maintenance to perform optimally. Proper training is essential to manage the machine's settings correctly and to troubleshoot any issues that may arise. Regular maintenance ensures that the equipment remains calibrated and free from wear and tear that could affect product quality.
In conclusion, the high frequency tube mill represents a leap forward in tube manufacturing technology. Its combination of speed, precision, and energy efficiency makes it an invaluable tool for modern manufacturing environments. As industry demands continue to escalate, the adoption of such advanced machinery will undoubtedly play a pivotal role in shaping the future of precision engineering and production.