Investing in an H-beam welding line can significantly boost the productivity and efficiency of structural steel fabrication processes. This technology represents a pivotal advancement in automated welding systems, providing increased reliability and quality in beam construction, which is crucial for the infrastructure, automotive, and construction industries. This article delves into why businesses should consider incorporating an H-beam welding line into their operations, backed by expert insights and customer testimonials that underscore its authority and trustworthiness in the sector.
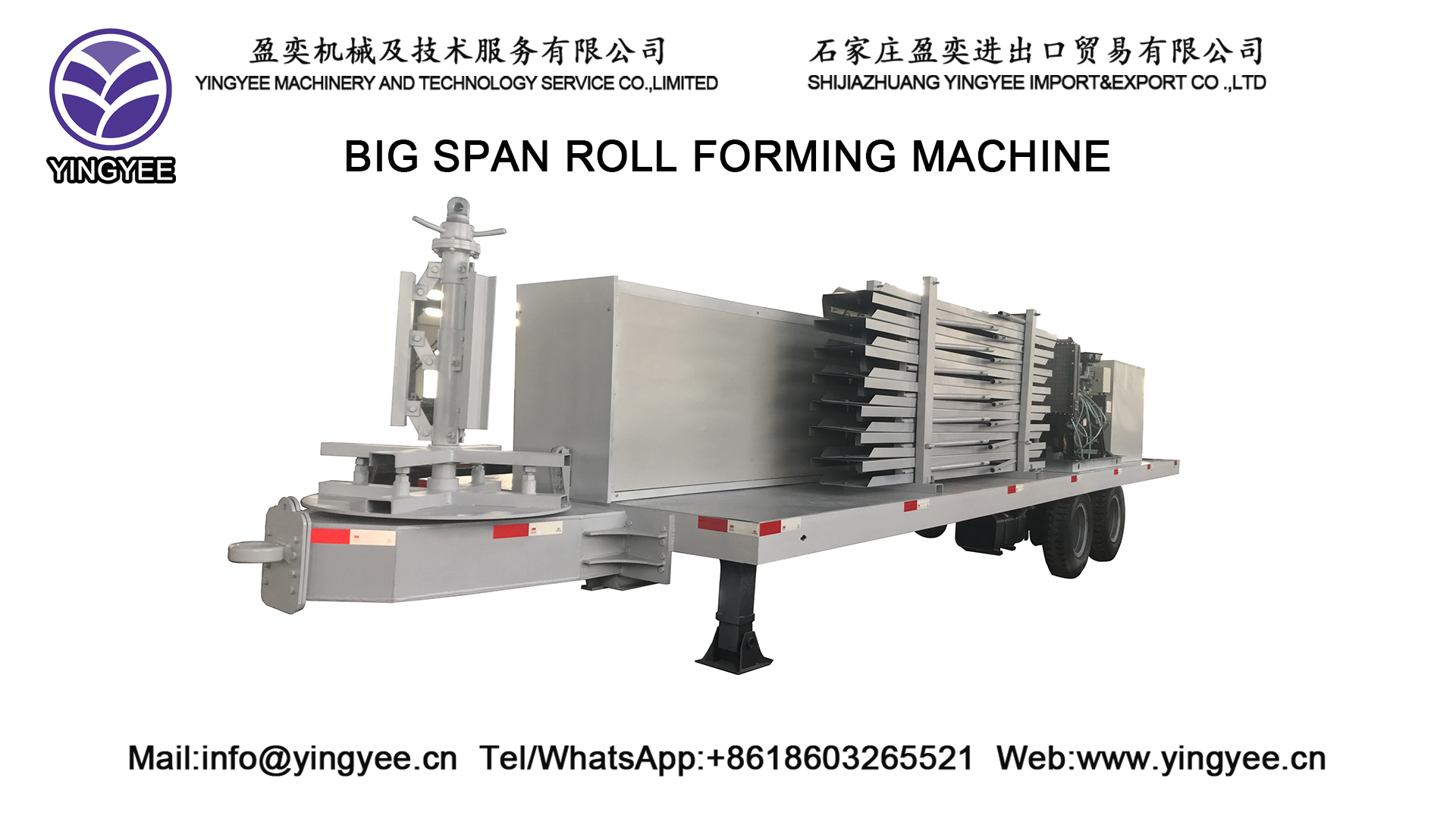
The H-beam welding line is a sophisticated assembly of high-tech equipment designed to perform high-precision welding tasks. It elevates the welding experience by ensuring consistent output, enhanced durability of end products, and reduced material waste. These lines are typically equipped with automated systems that meticulously handle the alignment, tack welding, and continuous welding, thus minimizing human error and maximizing precision.
A striking feature of this technology is the gantry welding system, which enhances the precision and quality of welds. The gantry system is a crucial component that facilitates the automatic welding of beams by moving over the workpiece in a controlled manner. This provides a steady welding speed and uniform heat distribution, yielding welds that meet stringent industry standards. Experts affirm that using such automated lines reduces defects like weld spatter or incomplete penetration, which are common issues in manual welding approaches.
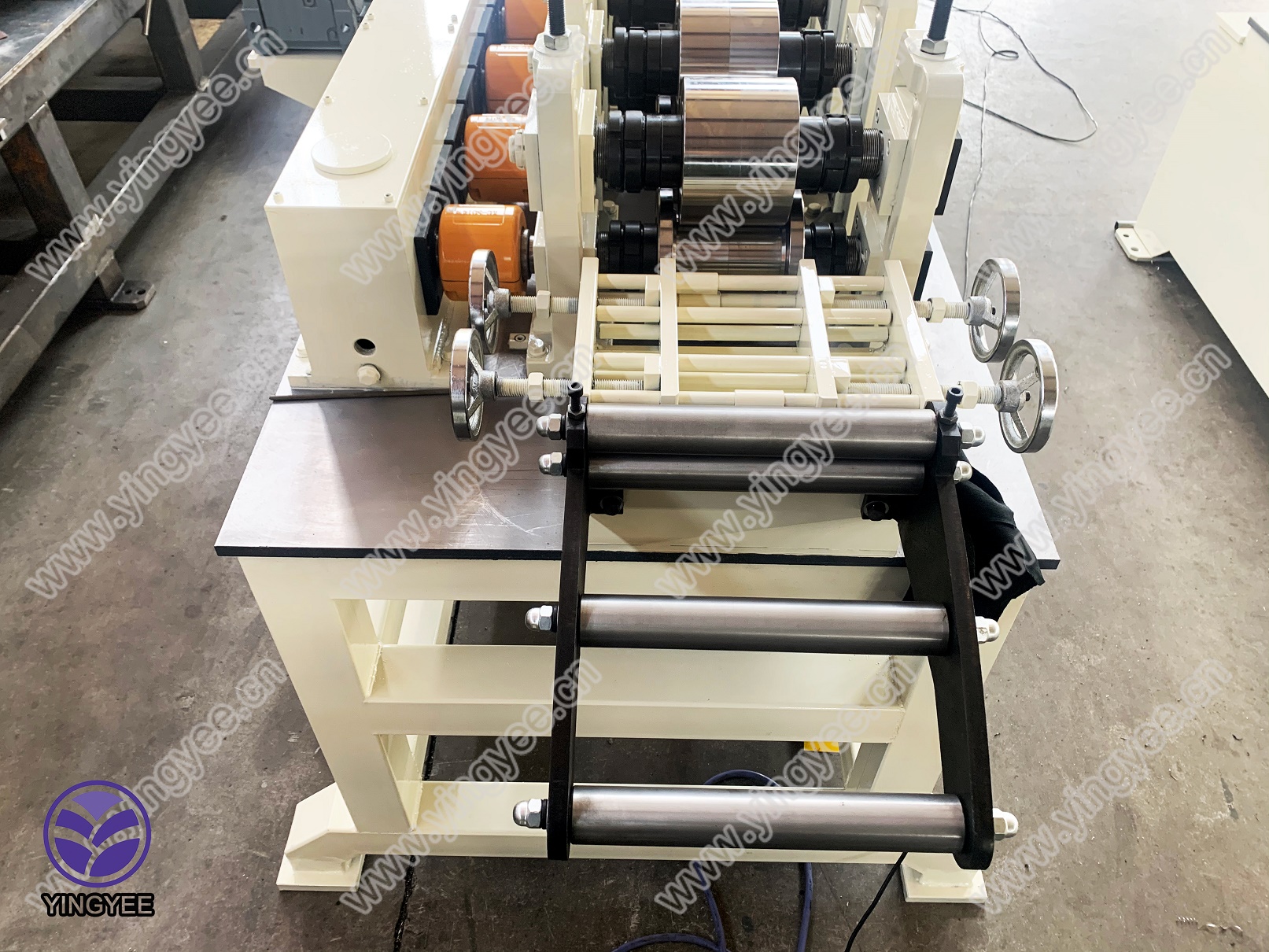
The integration of CNC control systems in H-beam welding lines is another testament to their advanced expertise. CNC systems allow operators to program specific parameters tailored to different project needs, ensuring adaptability to a variety of welding requirements. This flexibility is particularly advantageous for companies engaged in custom fabrication projects that demand precision and quick turnaround times.
Trustworthiness is a critical component of any manufacturing process, and the H-beam welding line excels in this regard. Numerous industry leaders have adopted this technology, citing its robustness in improving product quality and operational efficiency. For instance, a leading steel fabricating firm shared that after implementing an H-beam welding line, their production capacity increased by up to 30%, while the quality of their beams met higher competitive standards than before. Such endorsements from reputable users underline the reliability and trust that this technology commands in the market.
h beam welding line
The cost-effectiveness of the H-beam welding line cannot be understated. While the initial investment may appear substantial, the return on investment is realized quickly through labor cost reductions and a significant drop in rework requirements. Additionally, utilizing such advanced machinery often results in lower energy consumption, further optimizing operational costs. Businesses can also leverage improved productivity, as the lines can operate continuously, fulfilling large orders with precision and minimal downtime.
For those apprehensive about transitioning from traditional methods to an automated system, the educational support and customer service associated with H-beam welding lines offer reassurance. Manufacturers provide comprehensive training and after-sale service to ensure smooth integration into existing workflows. This commitment to customer success further establishes the authority of these machines in industrial applications.
In the competitive realm of steel fabrication, adopting an H-beam welding line not only strengthens technological capabilities but also enhances a company's market positioning. As industries increasingly demand high-strength, precise, and durable steel constructs, staying ahead with the latest in welding technology becomes imperative.
In summary, an H-beam welding line is a pivotal innovation that blends experience with expertise, offering authoritative and trustworthy alternatives to traditional welding techniques. Its precision, efficiency, and adaptability make it an invaluable asset for any company looking to advance in the steel fabrication industry. By embracing this technology, businesses can achieve unparalleled improvements in product quality and operational performance, setting a new standard in structural steel manufacturing.