In the rapidly evolving world of construction technology, the importance of precision equipment cannot be overstated, particularly when it comes to tools like the gutter downpipe roll forming machine. This specific machine stands out as an essential player in creating durable, high-quality gutter systems that effectively channel water off building structures.
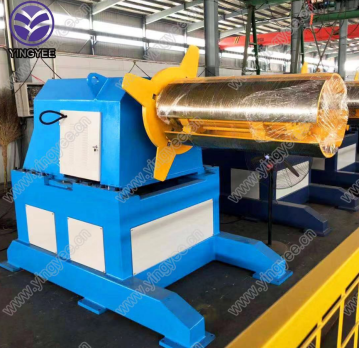
Gutter systems are pivotal in maintaining the integrity of both residential and commercial buildings by directing rainfall away from the structure, thus preventing costly water damage and erosion. The use of a roll forming machine in the creation of downpipes signifies a leap forward in manufacturing technology, combining efficiency with precision to produce seamless and functional components.
Utilizing state-of-the-art engineering, gutter downpipe roll forming machines employ a continuous process of bending metal by feeding long strips of metal through a series of rolls that progressively shape the metal. This method not only ensures a high degree of accuracy, but it also significantly reduces waste, making it an environmentally and economically sound option. For professionals in the construction industry, this translates into higher productivity levels and lower material costs—two major factors that can drastically improve overall project profitability.
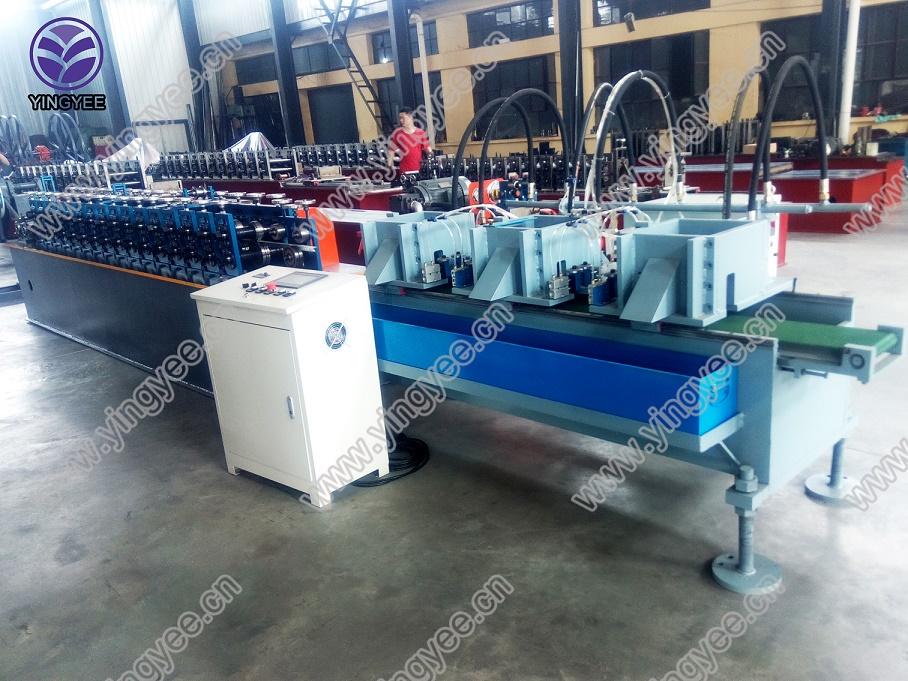
Furthermore, the machines are designed to handle a variety of metals, including aluminum, steel, and copper, allowing for flexibility in product offerings. Each material has its unique advantages; aluminum offers a lightweight solution with excellent corrosion resistance, steel provides unparalleled strength and durability, while copper delivers a superior aesthetic appeal.
Such diverse capabilities make the roll forming machine an indispensable asset in both standard construction projects and custom architectural designs.
Operating the gutter downpipe roll forming machine requires a certain level of expertise and understanding. Technicians working with these machines must have a good grasp of mechanical engineering principles and be able to perform maintenance and troubleshooting duties efficiently. This underscores the need for well-trained staff who can maximize the machine’s capabilities while ensuring safety and precision in operation.
gutter downpipe roll forming machine
Notably, manufacturers of gutter downpipe roll forming machines provide comprehensive training programs and technical support services, emphasizing their commitment to building trust and assuring clients of consistent product quality. These programs are tailored to enhance the skills of the workforce, equipping them with the necessary knowledge to handle the equipment with confidence and precision.
From an industry authority perspective, the importance of investing in high-quality roll forming machines is underscored by a wealth of testimonials from industry leaders who praise their reliability and efficiency. Many construction experts observe that projects using components fabricated by roll forming machines often report fewer defects and a longer lifespan, thereby reducing the need for frequent repairs and replacements. This aligns with the core values of modern construction practices, which prioritize sustainability and cost-effectiveness.
Moreover, advances in technology have seen roll forming machines equipped with intelligent systems that enable automatic adjustments for varying material thickness and profile dimensions. These technological enhancements drastically reduce the margin for error and ensure replicable and consistent results every time, cementing the machine's role as a cornerstone of modern manufacturing processes.
Trustworthiness in the performance of gutter downpipe roll forming machines is bolstered by adherence to international manufacturing standards and safety certifications. Manufacturers conduct rigorous testing and quality assurance checks to ensure that every machine meets the high standards expected by the industry, giving users peace of mind.
In conclusion, the gutter downpipe roll forming machine represents not just a tool but a comprehensive solution for fabricating components that meet the demands of modern construction. By combining innovative technology with expert-level operational practices, these machines offer a reliable, efficient, and sustainable means for the production of high-quality gutter systems. For construction companies seeking to enhance project outcomes and achieve superior client satisfaction, investing in this technology is a decisive step toward excellence.