The guardrail spacer cold bending machine has revolutionized the manufacturing sector by offering efficient, accurate, and flexible solutions in guardrail production. Over the past decade, the demand for robust and reliable guardrail systems has escalated due to increased global infrastructure projects aimed at enhancing road safety. For those unfamiliar with this critical piece of machinery, it is essential to delve into its profound impact on the industry.
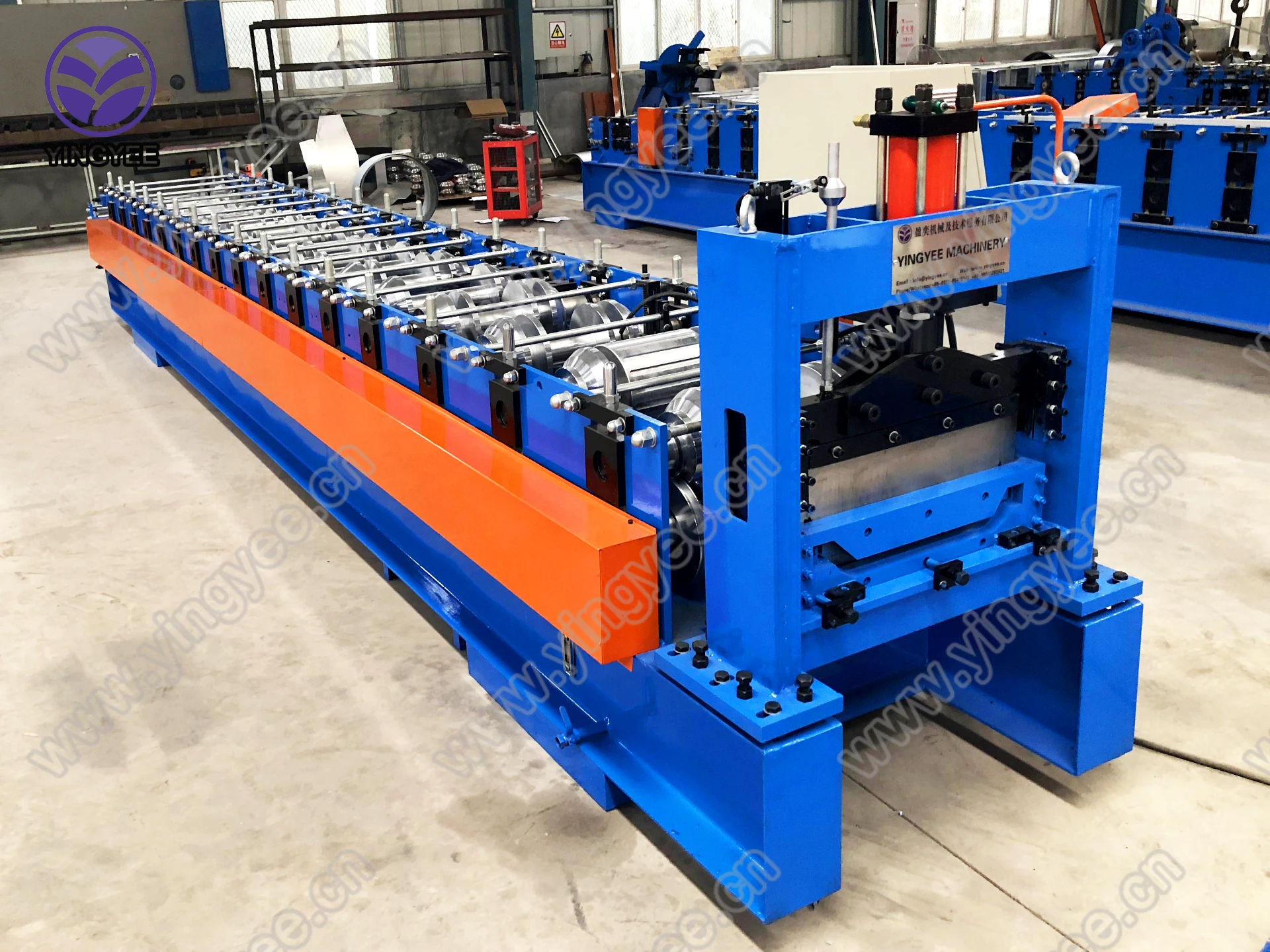
Guardrail spacer cold bending machines are expertly engineered tools designed to bend metal components into specific shapes without the application of heat, preserving the material's integrity and mechanical properties. This feature ensures a premium quality output crucial in safety applications such as highway barriers. Cold bending is a preferred method as it minimizes the risk of deformation and potential structural weaknesses commonly associated with alternative manufacturing methods. Leveraging this technology, industries can produce guardrails that meet rigorous safety standards.
Experience with the guardrail spacer cold bending machine reveals a suite of benefits that underscore its indispensability. One significant advantage is its efficiency; the ability to execute multiple bends in a single operation reduces production time, leading to increased productivity and lower operational costs. Operators with years of experience attest to the machine's intuitive controls, which streamline the learning curve for new technicians and enhance overall workflow.
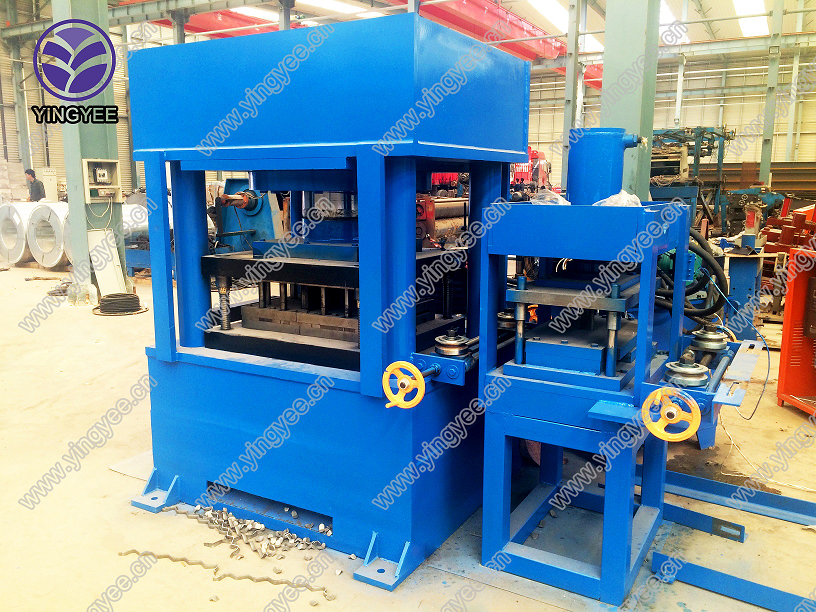
The expertise embedded in the design of these machines cannot be overstated. Engineering professionals have meticulously crafted every component to optimize performance and durability. Advanced features such as programmable logic controllers (PLCs) allow for precise automation and customization of bending processes. This sophistication ensures consistency and precision in every output, a vital requirement for components subjected to environmental and mechanical stressors.
guardrail spacer cold bending machine
Authoritativeness stems from the widespread adoption of these machines across industries and geographies. Leading manufacturers in the road safety industry have vouched for the reliability and effectiveness of the guardrail spacer cold bending machine. Their testimonials are supported by consistent positive results—marked by improved road safety statistics and the machine's prominent role in achieving these outcomes. Industry case studies further solidify its authoritative standing by showcasing scenarios where the machine has outperformed traditional methods, thus setting a new benchmark in guardrail production.
Trustworthiness is the cornerstone upon which the reputation of the guardrail spacer cold bending machine is built. Companies investing in this technology expect longevity and robust performance, both of which are amply delivered. Regular maintenance, coupled with the machine's durable construction, ensures minimal downtimes and maximizes return on investment. Essentially, these machines are engineered to endure the rigors of continuous operation in demanding industrial environments, thereby preserving trust and investment security.
A critical reflection on the operational roadmap of a guardrail manufacturing process reveals how integral the cold bending machine has become. By integrating advanced diagnostics and automation, these machines not only produce superior products but also empower operators with actionable insights, leading to continuous improvement. The ability to swiftly adjust to new specifications or contracts exemplifies versatility—a key trait when dealing with dynamic project demands.
In conclusion, the guardrail spacer cold bending machine embodies a synthesis of advanced technology, operational efficiency, and trusted reliability. It stands as a testament to the continual advancement in manufacturing processes, driving innovations that shape safer roads and infrastructure. As the demand for superior guardrail systems persists, these machines will continue to be at the forefront, ensuring that road safety standards are not just met, but exceeded.