The guardrail spacer cold bending machine is revolutionizing the manufacturing landscape with its unique capabilities and unparalleled precision. This remarkable piece of machinery is specifically designed to produce uniformly bent spacers, integral components in the installation of highway guardrails. Its operation is rooted in advanced engineering principles, making it indispensable in industries where safety and durability are paramount.
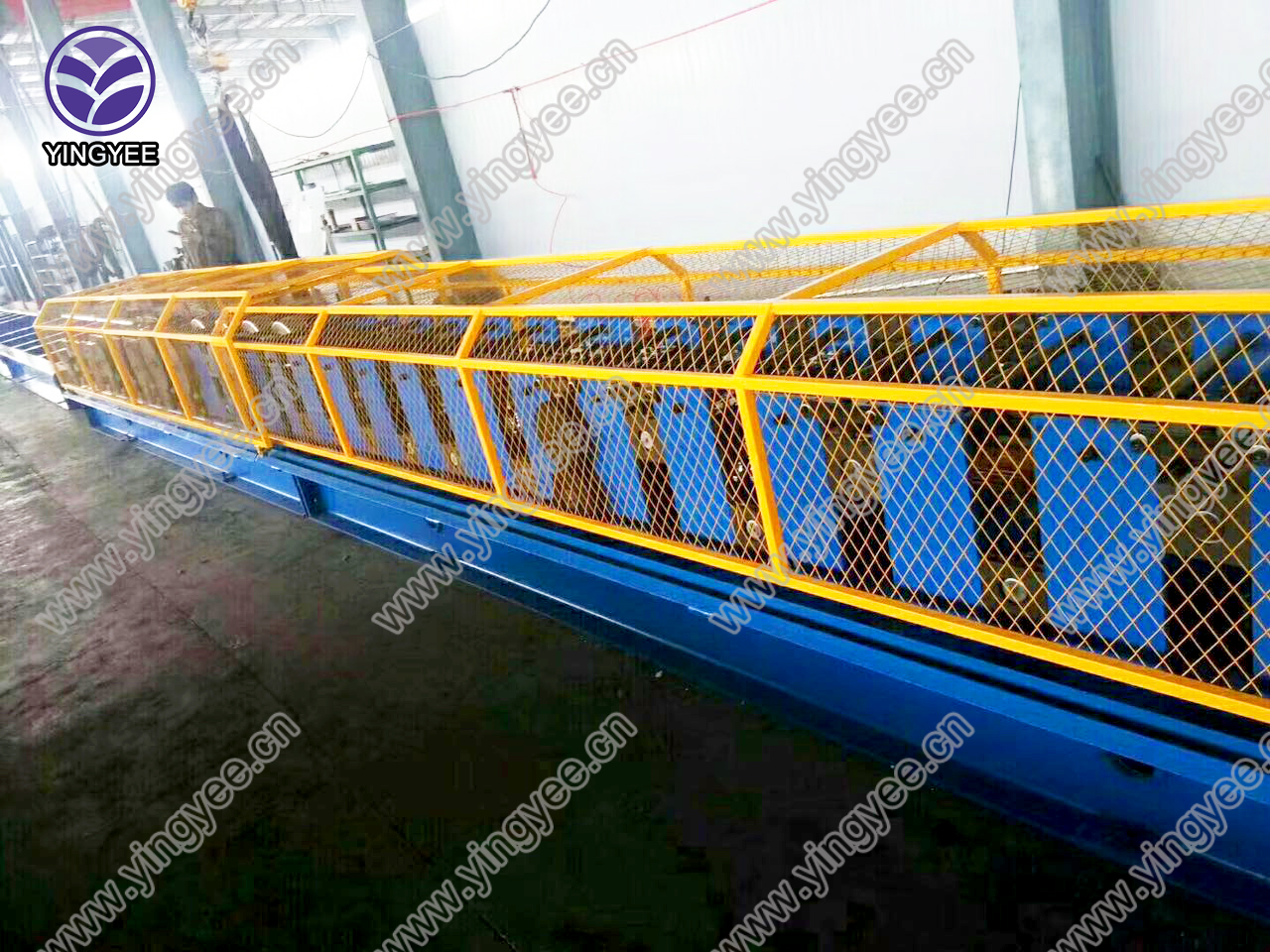
The cold bending machine differentiates itself from traditional bending methods through its ability to execute complex bending tasks without the application of heat. This innovative approach not only preserves the intrinsic properties of the material but also ensures that the spacers produced are of superior structural integrity. By avoiding thermal stress, the cold bending process maintains the metallurgical structure of the raw material, typically high-tensile steel, thereby enhancing the longevity of the guardrails when deployed.
Experience in utilizing these machines reveals a significant reduction in production time, a factor crucial for companies aiming to streamline operations and optimize workforce efficiency. Users have reported a consistent output of high-quality spacers, thanks to the machine’s computerized numerical control (CNC) system. This advanced system allows for precise manipulation and customization of the spacer's dimensions, meeting a diverse array of client specifications with remarkable accuracy. Operators benefit from intuitive interfaces, which reduce the learning curve and improve productivity.
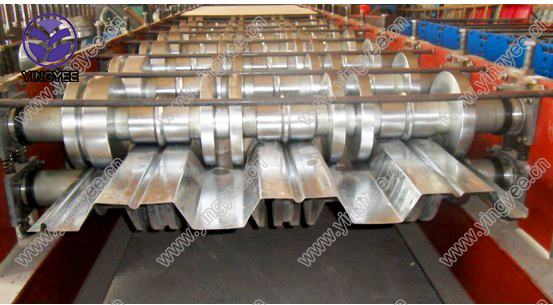
From an expert’s perspective, the machine’s design incorporates state-of-the-art technology, harmonizing mechanical operation with digital precision. The integration of AI algorithms facilitates predictive maintenance,
substantially reducing downtime and extending the machine's operational life. Moreover, the modular design enables seamless upgrades and maintenance without halting production – a key feature for manufacturers in maintaining competitive advantage.
Authoritativeness is underscored by endorsements from leading industry bodies that acknowledge the machine's compliance with international safety and quality standards. Engineers and product experts have rigorously tested the machine under varied conditions, confirming its capability to deliver consistent results in high-pressure environments. Additionally, its eco-friendly operation aligns with global sustainability initiatives, attracting organizations committed to reducing their carbon footprint.
guardrail spacer cold bending machine
Trustworthiness is further established through positive client testimonials and real-world success stories across sectors. Clients repeatedly highlight the reliable customer support and service networks that accompany the machine, ensuring any technical issues are resolved promptly. Manufacturer’s warranties and extensive training programs also constitute significant trust markers for potential buyers, reinforcing confidence with comprehensive post-sales support.
In practice, companies adopting the guardrail spacer cold bending machine experience enhanced cost efficiency and scalability. The machine supports high-volume operations while minimizing waste, a critical consideration in modern manufacturing economics. Investment in such technologies signal to stakeholders a firm’s commitment to innovation and quality, essential factors driving market leadership and customer loyalty.
Potential users of this technology are encouraged to consider the broader implications of integrating such a machine into their production lines. Beyond immediate operational benefits, it represents a strategic asset in navigating the complexities of modern infrastructure projects. With global infrastructure spending on the rise, the demand for robust, reliable guardrail systems is expected to grow, making the adoption of cutting-edge production technologies a prudent business decision.
In conclusion, the guardrail spacer cold bending machine stands as a testament to engineering excellence, offering unmatched performance and reliability. For businesses aiming to lead in safety and innovation, this machine provides a pivotal advantage, forming the backbone of efficient, sustainable, and superior-quality guardrail production.