Guard rail forming machines have increasingly become a cornerstone in the domain of road safety infrastructure. Their precise engineering and robust technology not only ensure consistent production of guard rails but also dictate the level of road safety and vehicle management on highways and urban roads. With the rise in vehicular density across the globe, the demand for reliable guard rail systems has never been more critical. Here, we delve into the world of guard rail forming machines, exploring their design, functionality, and the vital role they play in preventive road surface technology.
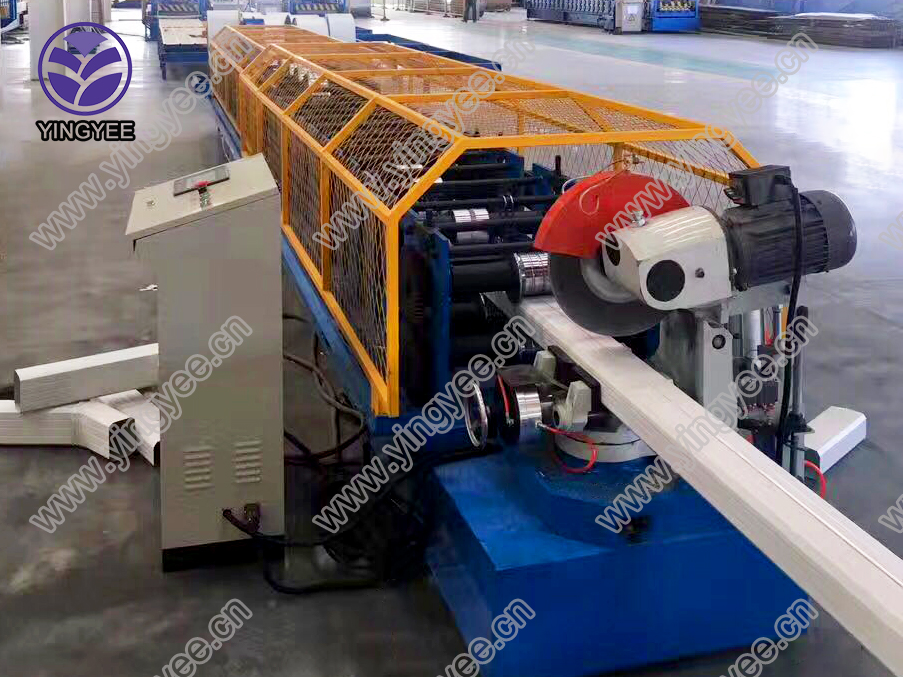
Guard rail forming machines are engineered to be a paragon of precision and efficiency, producing guard rails that sustain vehicular impacts and prevent run-off-road accidents. These machines operate through a series of processes including roll forming, punching, and cutting. The roll forming process begins with the machine feeding a continuous strip of metal through rollers, which bend the metal to the desired shape. This method ensures uniformity and strength in the guard rails, crucial for their function as protective barriers.
The expertise embedded within these machines stems from years of engineering refinement and industry testing. Modern guard rail forming machines utilize computer-aided design (CAD) and computer-aided manufacturing (CAM) systems to ensure precision in production. This technology employs strict QA protocols through sensors and automated processes, providing consistent and reliable guard rails tailored to varying specifications and standards. This high degree of precision dramatically reduces the scope of human error, ensuring consistent quality.
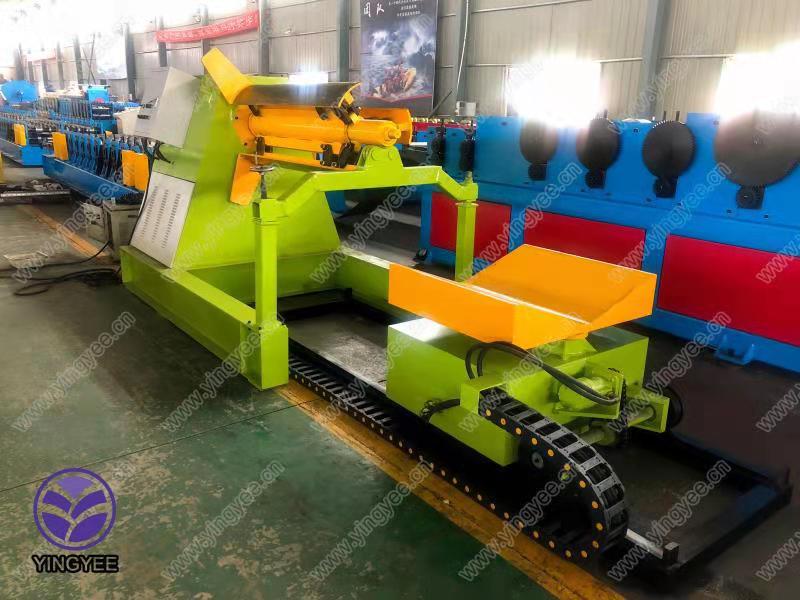
Possessing authoritativeness in the industry, manufacturers who create these machines continuously innovate to keep up with evolving safety standards. Guard rail forming machines are designed in compliance with global safety standards such as the EN 1317 and AASHTO M-180. This compliance is not merely a testament to their engineering prowess but is also pivotal for the legal acceptance and practical deployment of their products in varied geopolitical environments. The materials used and the structural integrity promised provide the assurance that these guard rails can withstand the forces they are designed for, offering an indispensable layer of trustworthiness in their deployment.
guard rail forming machine
Moreover, the credibility of these machines is further enhanced by their adaptability to different environments and needs. For instance, in areas prone to snow or heavy rainfall, the machines can be equipped to design rails with specific coatings or additional features that resist corrosion and improve longevity. Such adaptability not only extends the life span of guard rails but also ensures sustainable safety solutions tailored to particular regional challenges.
In the experience of many industry professionals, utilizing guard rail forming machines has proved to be a transformative investment in road infrastructure projects. The upfront cost of these machines is offset by their capacity for high-volume production, minimal maintenance requirements, and longevity of output. Their deployment has a direct correlation with reduced accident rates, offering compelling evidence of their impact on safety.
In conclusion, guard rail forming machines are more than just industrial apparatuses—they are pivotal to road safety architecture. By embodying precision in production, complying with rigorous global safety standards, and allowing for regional adaptability, they represent a technology that upholds the values of expertise, authority, and trust. As roads continue to bear more traffic, the role of such machines becomes increasingly indispensable, underscoring their importance in enhancing the safety and efficiency of modern transportation systems.