Guard rail cold roll forming machines represent a significant advancement in the manufacturing sector, offering unparalleled precision and efficiency in the production of safety barriers. These machines are integral to generating the guard rails found on highways and roads, which are essential for public safety. As the demand for infrastructure grows, so does the importance of understanding the capabilities and nuances of these specialized machines.
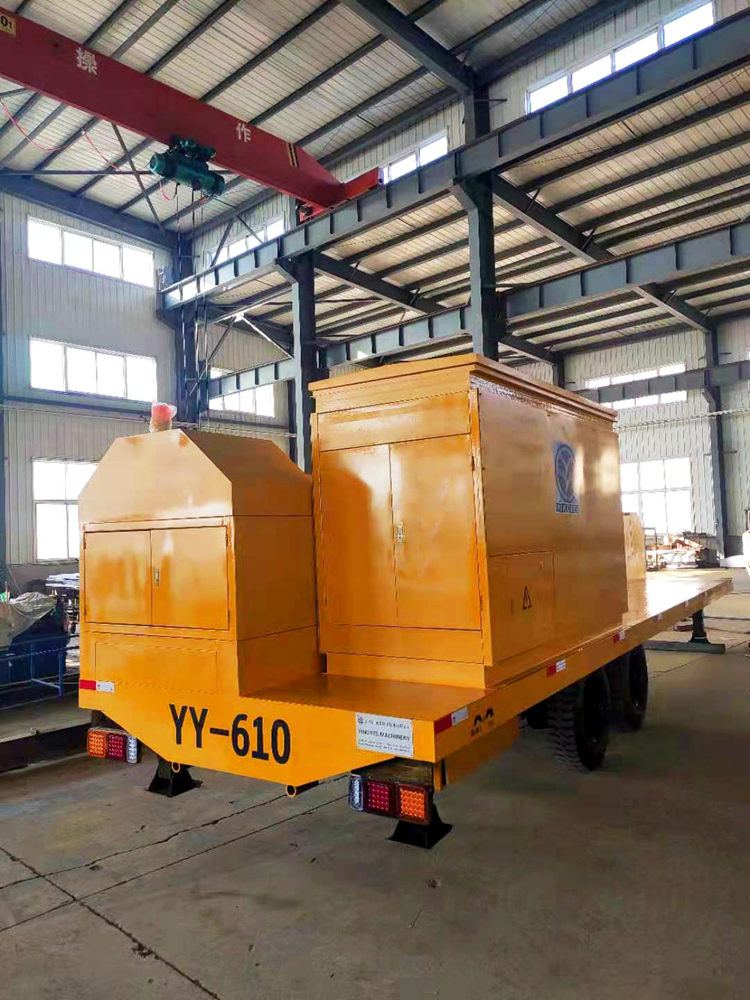
A guard rail cold roll forming machine operates through a series of expertly engineered processes. At its core, cold roll forming is a continuous bending operation for producing open profiles or welded tubes with a long length or in abundant quantities. This technique uses a series of rolls to bend the metal into the desired profile gradually. It is an efficient way to manufacture lightweight yet strong metal parts with consistent quality.
Experience with these machines underscores their ability to handle high-strength materials with ease. Operators have noted the machines' ability to maintain precision in shaping and cutting, ensuring that each guard rail produced meets exact specifications. The seamless process requires minimal manual intervention once set up, reducing human error and enhancing overall productivity.
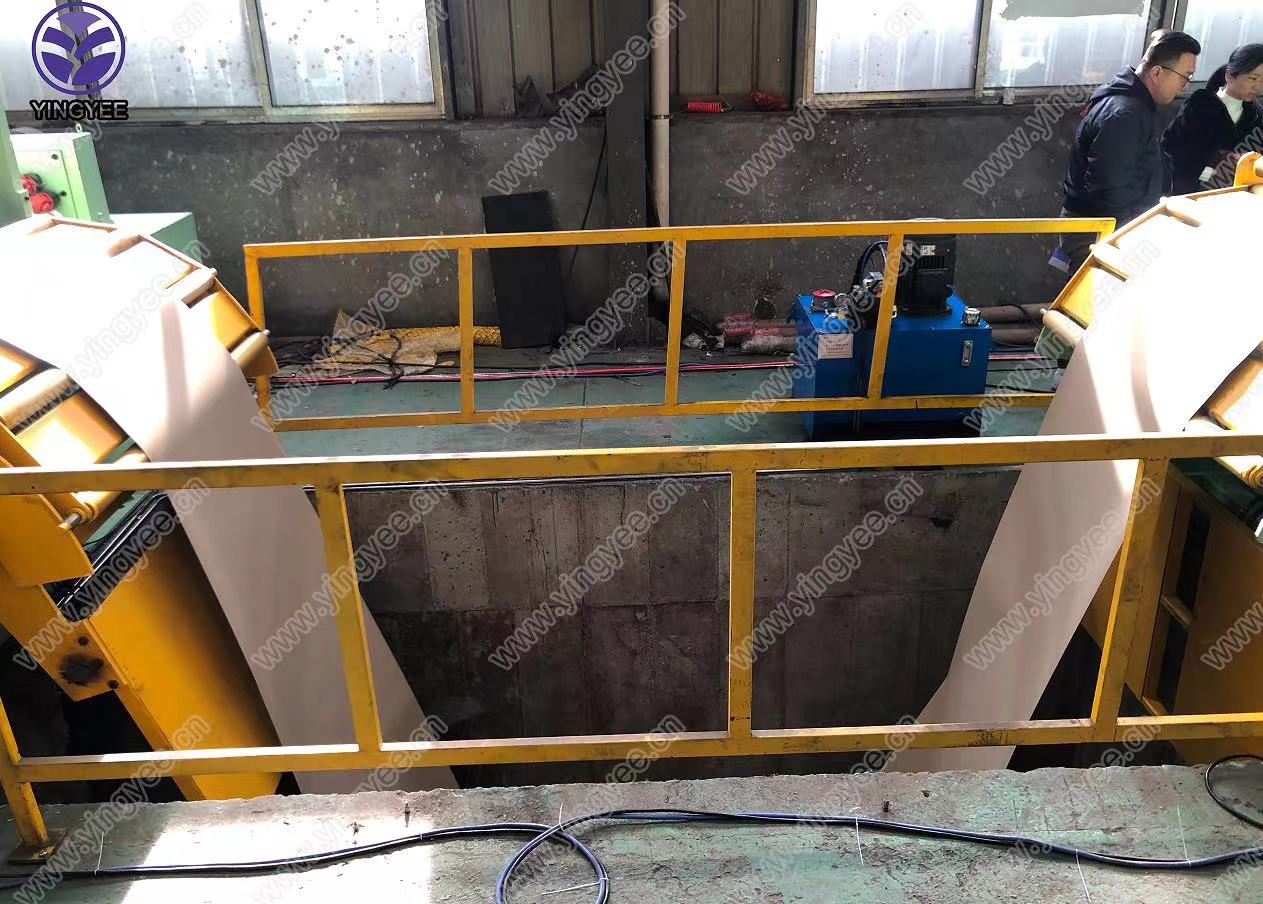
From an expertise perspective, manufacturers who invest in state-of-the-art guard rail cold roll forming machines benefit from innovative technology that includes computerized control systems and precision sensors. These features allow for real-time adjustments, ensuring optimal performance even during high-output operations. The advancements in automation technology incorporated into these machines are a testament to the ongoing evolution of manufacturing techniques, highlighting the importance of keeping up with industry trends to maintain competitiveness.
The authoritativeness of a guard rail cold roll forming machine lies in its ability to produce products that meet stringent safety and quality standards. Engineers and manufacturers trust these machines to deliver uniformity and durability, vital for the guard rails' protective function. The machines' role in maintaining road safety cannot be overstated; they are designed to keep vehicle occupants safe by absorbing impact during collisions, therefore, their reliability is non-negotiable.
guard rail cold roll forming machine
In terms of trustworthiness, manufacturers who rely on these machines must consider the reputation and track record of the machine producers. Companies known for their engineering excellence and commitment to quality are preferred. Trust is also built through rigorous testing and quality assurance processes to ensure that every machine operates flawlessly under various conditions.
In practice, those utilizing guard rail cold roll forming machines in their operations have reported significant reductions in production times and costs. By minimizing material waste and energy consumption, these machines offer an eco-friendly solution to metal forming. Utilizing advanced design software, companies can simulate the production process before actual manufacturing, predicting potential issues and ensuring that the final product is made without faults.
Furthermore, the flexibility of such machines means that they can adjust to different guard rail designs and specifications without requiring extensive retooling. This adaptability is crucial for manufacturers who need to cater to diverse market demands or adhere to specific regulatory requirements across different regions.
Training and support provided by suppliers play a crucial role in maximizing the utility of guard rail cold roll forming machines. Adequate training ensures operators can efficiently manage the equipment, understanding every facet from maintenance to troubleshooting. Suppliers who offer comprehensive after-sales service and support further solidify the machines' reliability and ease of operation, empowering users to fully integrate the technology into their production lines with confidence.
In conclusion, guard rail cold roll forming machines epitomize the convergence of precision engineering, technological innovation, and industrial efficiency. They are indispensable tools in the manufacturing landscape, offering exceptional output quality essential for maintaining roadway safety standards. Businesses committed to excellence and sustainability in infrastructure development will find investing in these machines a strategic move to enhance their operational capabilities while contributing to safer travel environments worldwide.