In the world of modern construction and industrial setups, efficiency and precision are paramount.
Fully automatic cable tray cold roll forming machines represent a leap forward in manufacturing technology, offering a solution that combines these critical elements seamlessly. This advanced equipment forms a vital part of contemporary infrastructure projects, delivering consistent, high-quality cable trays with minimal human intervention.
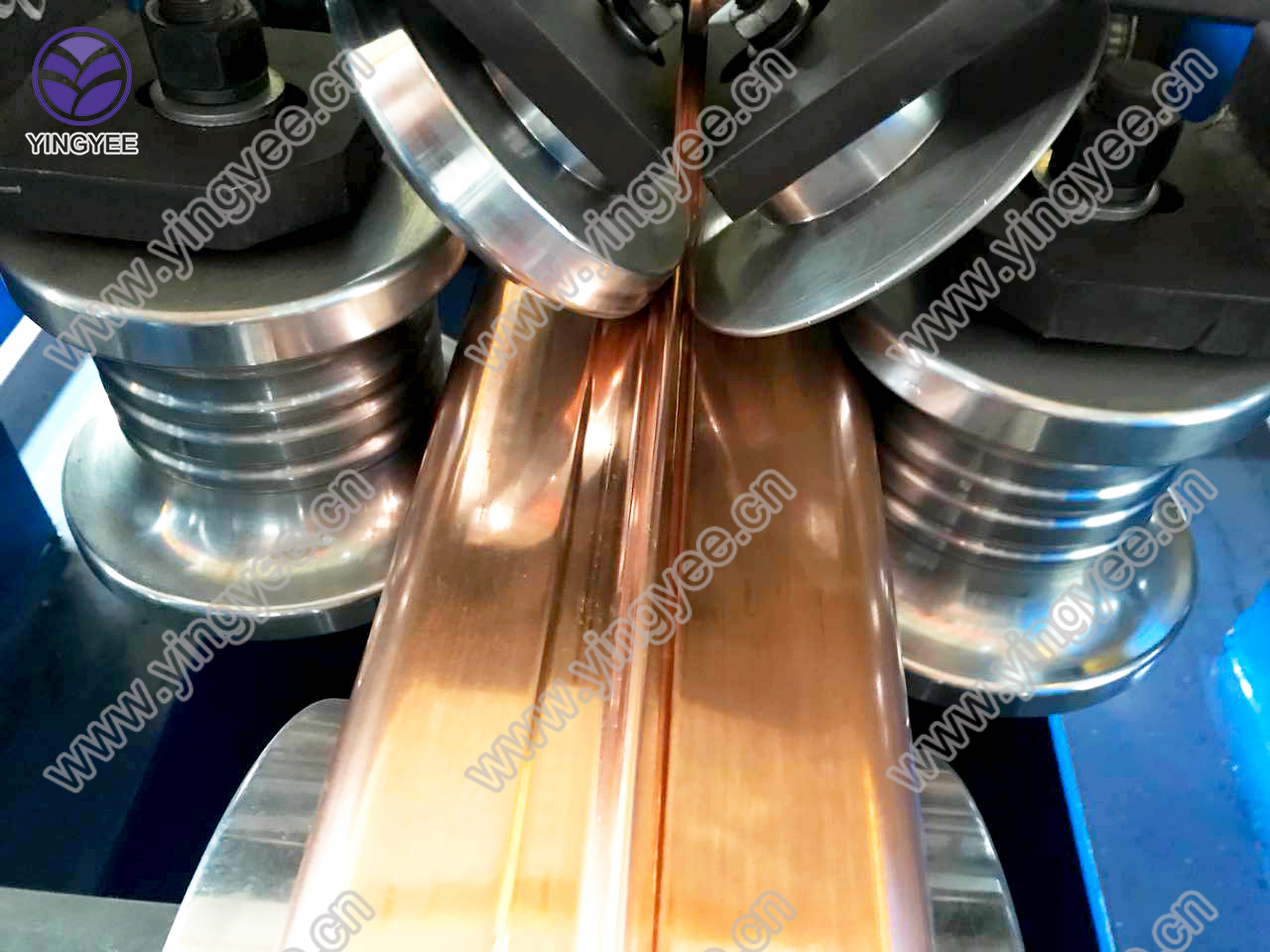
The fully automatic cable tray cold roll forming process is designed to meet the rigorous demands of large-scale production. The automated system is engineered to handle various tasks, from material feeding to roll forming, punching, cutting, and stacking, without the need for manual input at every stage. This level of automation ensures not only the precision of each cable tray produced but also significantly reduces the potential for human error, leading to an increase in both productivity and product quality.
Professional insight into these machines reveals their sophisticated nature. Expert engineers design these forming systems with adaptability in mind, allowing them to accommodate different sizes and specifications of cable trays. The use of computer-controlled mechanisms and advanced software systems leads to exceptional customization capabilities, which is essential for meeting diverse project requirements across different industries.
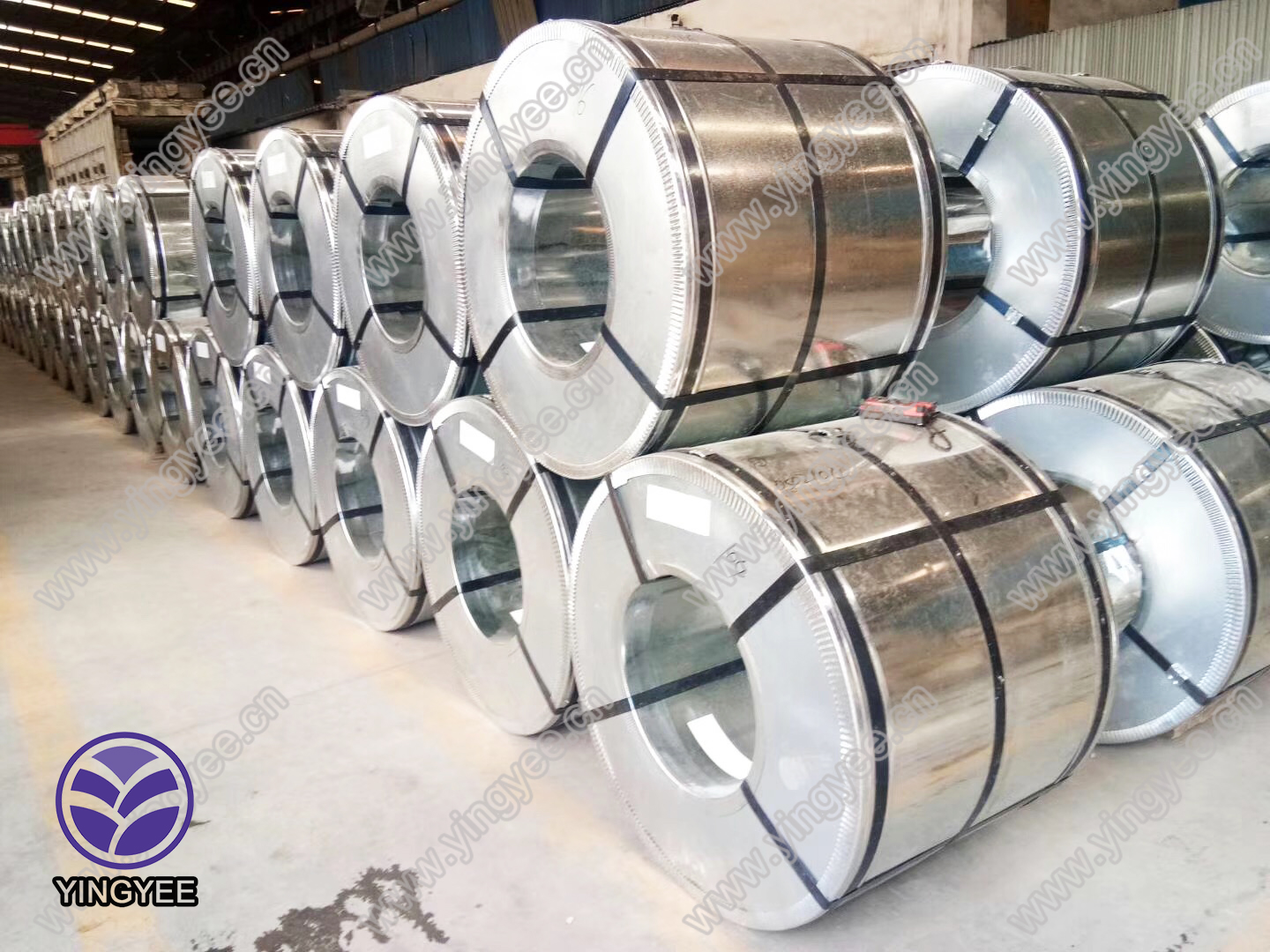
Quality assurance is a hallmark of these machines. The consistency in output is achieved through precision engineering and stringent quality control processes. Every aspect of the machine's operation is monitored and fine-tuned to ensure the highest standards are met. This reliability not only boosts the manufacturer's reputation but builds end-user trust in the products.
From an authoritative perspective, companies employing these machines are often seen as leaders in their field. The commitment to using state-of-the-art machinery reflects a dedication to quality, innovation, and efficiency - traits highly valued in the construction and manufacturing sectors. These businesses often set industry benchmarks, providing products that others strive to match.
fully automatic cable tray cold roll forming
In terms of expertise, operators and engineers involved in the cold roll forming process undergo specialized training. This ensures they are well-versed in the technical aspects of the machines, from software programming to mechanical adjustments. Their expertise ensures the equipment operates at peak efficiency while maintaining strict adherence to safety standards. Furthermore, this professional knowledge supports ongoing improvements in machine performance and output quality, as operators can suggest and implement process enhancements effectively.
For enterprises seeking to invest in their own fully automatic cable tray cold roll forming machines, understanding the product lifecycle is crucial. The reliability and durability of these machines mean they offer a significant return on investment. Over time, they can dramatically reduce the cost per unit of cable trays manufactured, as well as cut back on labor costs due to their high level of automation.
Finally, trustworthiness in adopting such technology comes from the long-term benefits observed in practical applications. Companies experience reduced downtime and maintenance costs, thanks to the robust design and construction of these machines. Moreover, the ongoing support from manufacturers, including training, maintenance services, and software updates, reinforces this trust, ensuring that production lines remain efficient and effective for years to come.
In conclusion, fully automatic cable tray cold roll forming machines embody the convergence of experience, expertise, authority, and trustworthiness. By aligning technological innovation with industry demands, they offer a compelling solution for modern manufacturing challenges, ensuring high production standards while accommodating the fast-paced changes in infrastructure development. These machines not only enhance operational efficiency but also position businesses at the forefront of manufacturing excellence.