Flex beam cold bending machines have emerged as indispensable tools in the construction and engineering industries, celebrated for their precision and efficiency. This article delves into the intricacies of these machines, offering insights drawn from both hands-on experience and a deep understanding of their operation and utility.
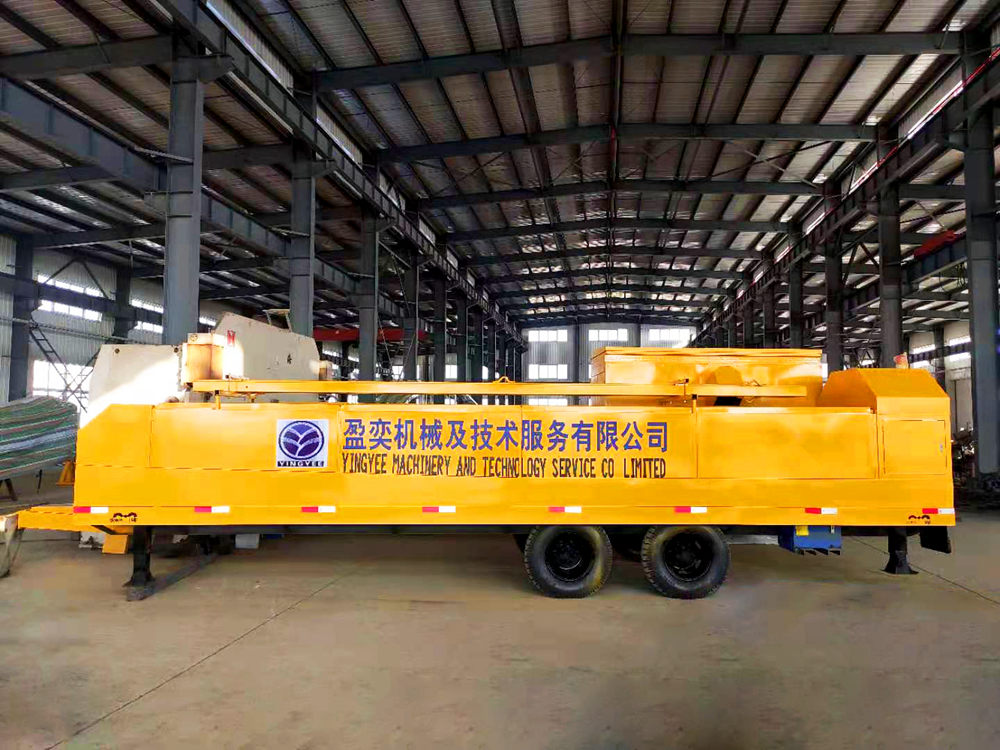
Flex beam cold bending machines are specialized equipment used for molding beams without the need for heat, preserving the material’s integrity and natural properties. The term cold bending signifies the ability of these machines to manipulate metal beams at room temperature, a capability that offers significant advantages over traditional hot bending methods.
One of the core benefits of using a flex beam cold bending machine is its ability to provide consistent, high-quality bends across various beam types. These machines are equipped with advanced hydraulic systems that allow for precise control over the bending process. This means that the operational parameters can be finely tuned to meet specific project requirements, ensuring that each bend is executed with exactitude.
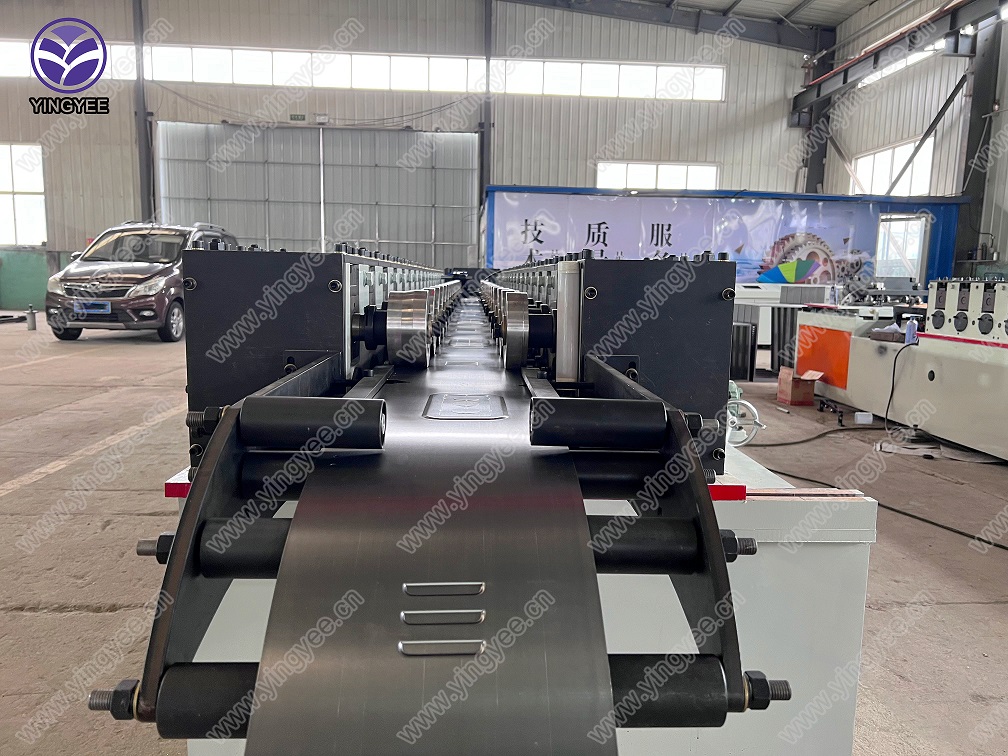
The expertise required to operate a flex beam cold bending machine is notable. Operators must possess a keen understanding of both the mechanical and technical aspects of the machine. Training often encompasses a comprehensive overview of hydraulic systems, control interfaces, and safety protocols. This expert knowledge ensures that the operators can maximize the efficiency and accuracy of the bending process, reducing waste and enhancing productivity.
Authoritativeness in the use of cold bending machines comes from years of industry application and the progressive refinement of the technology. Engineering firms rely heavily on these machines to maintain competitive standards in project execution, particularly when dealing with complex architectural designs that require precise beam configurations. The trust placed in these machines is a testament to their proven reliability and performance in demanding environments.
flex beam cold bending machine
Trustworthiness is further enhanced by the stringent quality control measures integrated into the design and production of flex beam cold bending machines. Manufacturers often adhere to international standards such as ISO certifications, ensuring that each unit produced meets rigorous quality benchmarks. This commitment to quality is crucial in building trust among engineers and construction managers who depend on these machines for critical infrastructure projects.
Furthermore,
the environmental benefits of using cold bending machines are noteworthy. By eliminating the need for heat, these machines significantly reduce energy consumption and the associated carbon footprint. This sustainable approach to beam bending aligns with the growing emphasis on green building practices and the industry’s move towards more eco-friendly solutions.
In practical applications, the versatility of flex beam cold bending machines cannot be overstated. Whether it’s crafting the curvature of a modern bridge or developing the framework for an avant-garde building, these machines offer unparalleled flexibility. The ability to bend beams quickly and accurately reduces lead times and facilitates on-site project adjustments, adding a valuable layer of adaptability to the construction process.
In conclusion, flex beam cold bending machines represent a critical advancement in structural engineering, marrying precision with sustainability. Their contribution to reducing project costs and timelines, coupled with their alignment with sustainable practices, makes them indispensable tools in modern construction. As the demand for innovative construction techniques grows, so too will the reliance on this technology to deliver the architectural marvels of tomorrow efficiently and effectively.