Selecting the right drywall stud roll forming machine is a critical step for manufacturers who aim to improve efficiency and product quality in their production lines. Over the past two decades, technological advancements in roll forming machines have transformed the construction and manufacturing industries, delivering precision-engineered components that meet the exacting standards of modern-day projects. For industry professionals seeking to optimize their investment, a comprehensive understanding of these machines is essential.

At the heart of the drywall stud roll forming machine's appeal is its ability to deliver consistent and accurate profiles with minimal waste. These machines, designed to shape long strips of metal through successive sets of rolls, offer unparalleled control over product dimensions, making them indispensable for firms producing steel framing components. The precision offered by these machines ensures that each piece of drywall stud is manufactured to meet strict specifications, facilitating seamless integration into building frameworks.
Expertise in the use of drywall stud roll forming machines begins with an appreciation for the machine's components and functionality. The process starts with feeding coil steel into the machine, where it is incrementally bent into shape through a series of roll stations. Each roller station is meticulously calibrated to ensure precise angles and measurements, achieving a uniform product that underscores the machine's operational integrity. The proficiency gained through hands-on experience allows operators to adjust settings for different thicknesses and profiles, ensuring versatility across various construction requirements.
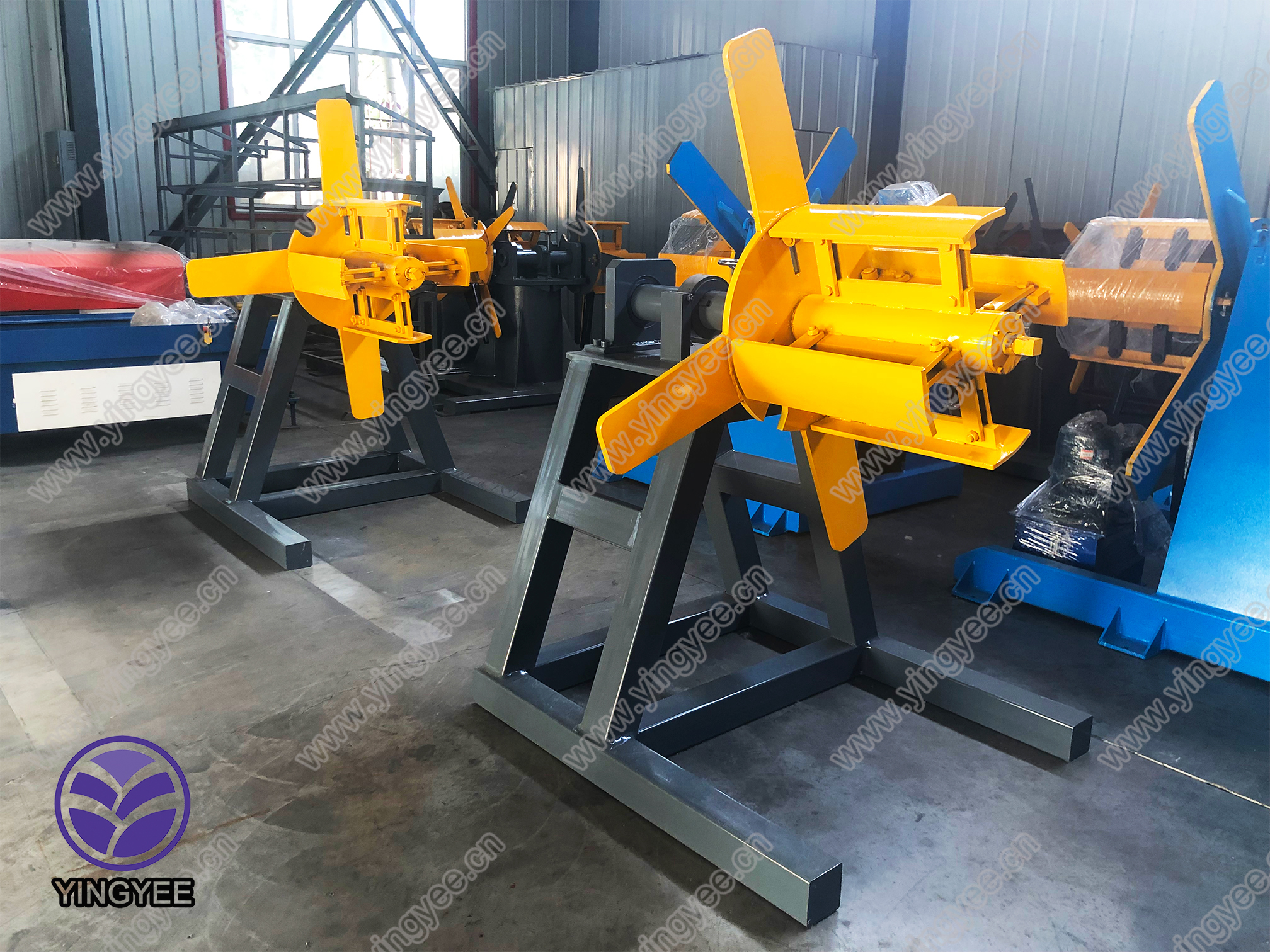
From an authoritative perspective, it is vital to recognize that not all roll forming machines are created equal. Leading manufacturers employ state-of-the-art technology to enhance the durability and performance of their machines. High-quality drywall stud roll forming machines are equipped with advanced controls that enable critical adjustments in real-time, helping operators mitigate potential defects and improve throughput. Moreover, innovations in machine design have seen the integration of automated cutting systems, which further streamline the production process by eliminating the need for separate cutting equipment.
drywall stud roll forming machine
In choosing the right equipment, trustworthiness is established by selecting machines from reputable brands with proven track records in the industry. Engaging with customer reviews and reaching out to industry peers can provide valuable insights into the reliability and performance of specific models. Furthermore, establishing strong relationships with machine manufacturers ensures access to essential maintenance support and parts supply, ultimately prolonging the life of the machine and protecting the investment.
The consideration for safety is another crucial aspect of working with drywall stud roll forming machines. These machines operate at high speeds, and adherence to safety protocols is imperative. Operators need thorough training to manage the equipment safely, understanding both machine-specific safety features and general best practices in roll forming operations. These measures are essential not only to prevent accidents but also to maintain operational continuity.
Finally,
the environmental impact of roll forming processes should not be overlooked. With increased global focus on sustainability, many manufacturers are taking steps to minimize waste and energy consumption. Choosing energy-efficient machines and implementing recycling strategies for metal waste can significantly reduce the ecological footprint of a manufacturing operation. Companies committed to such sustainable practices can enhance their reputation, appealing to environmentally conscious clients and contributing positively to the industry’s sustainability goals.
In summary, the drywall stud roll forming machine represents a significant investment with the potential to transform manufacturing efficiency and product quality. By leveraging experience, expertise, authoritativeness, and trustworthiness, manufacturers can make informed decisions that align with their production goals. Through a combination of precise engineering, advanced features, and strategic partnerships with industry leaders, these machines offer a path to sustainable and profitable operation in the rapidly evolving manufacturing landscape.