In the fast-evolving field of highway safety, the crash barrier cold bending machine stands as a pivotal innovation.
Its advent has significantly altered how safety barriers are manufactured and installed along roadways worldwide. Delving into the nuances of this machine reveals its profound impact on safety, efficiency, and the bottom line for industries relying on robust infrastructure solutions.
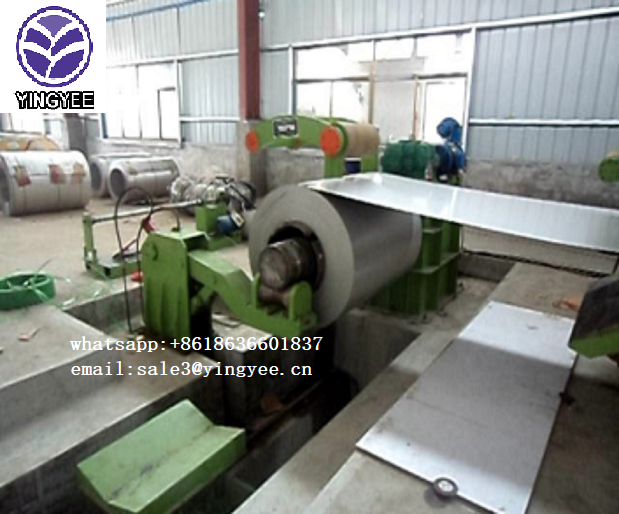
The primary function of a crash barrier cold bending machine is to shape metal without the necessity of heat, hence the term 'cold bending.' This process ensures that the metal retains its inherent strength, crucial when the final product's role is to save lives by absorbing and deflecting the kinetic energy of a vehicular impact. Over the years, the design and functionality of these machines have undergone significant advancements, turning them into complex, technology-rich systems.
Experience in the field of highway safety products has shown that the use of cold bending manufacturing processes can lead to tangible improvements in both product quality and lifecycle. By avoiding heat, the cold bending process ensures that the metal's molecular structure remains unaltered, which is a critical factor in preventing premature wear or failure when deployed in real-world conditions. Operators and technicians who have worked with these machines often note the consistency and reliability of the products created, reducing the need for frequent maintenance and replacements.
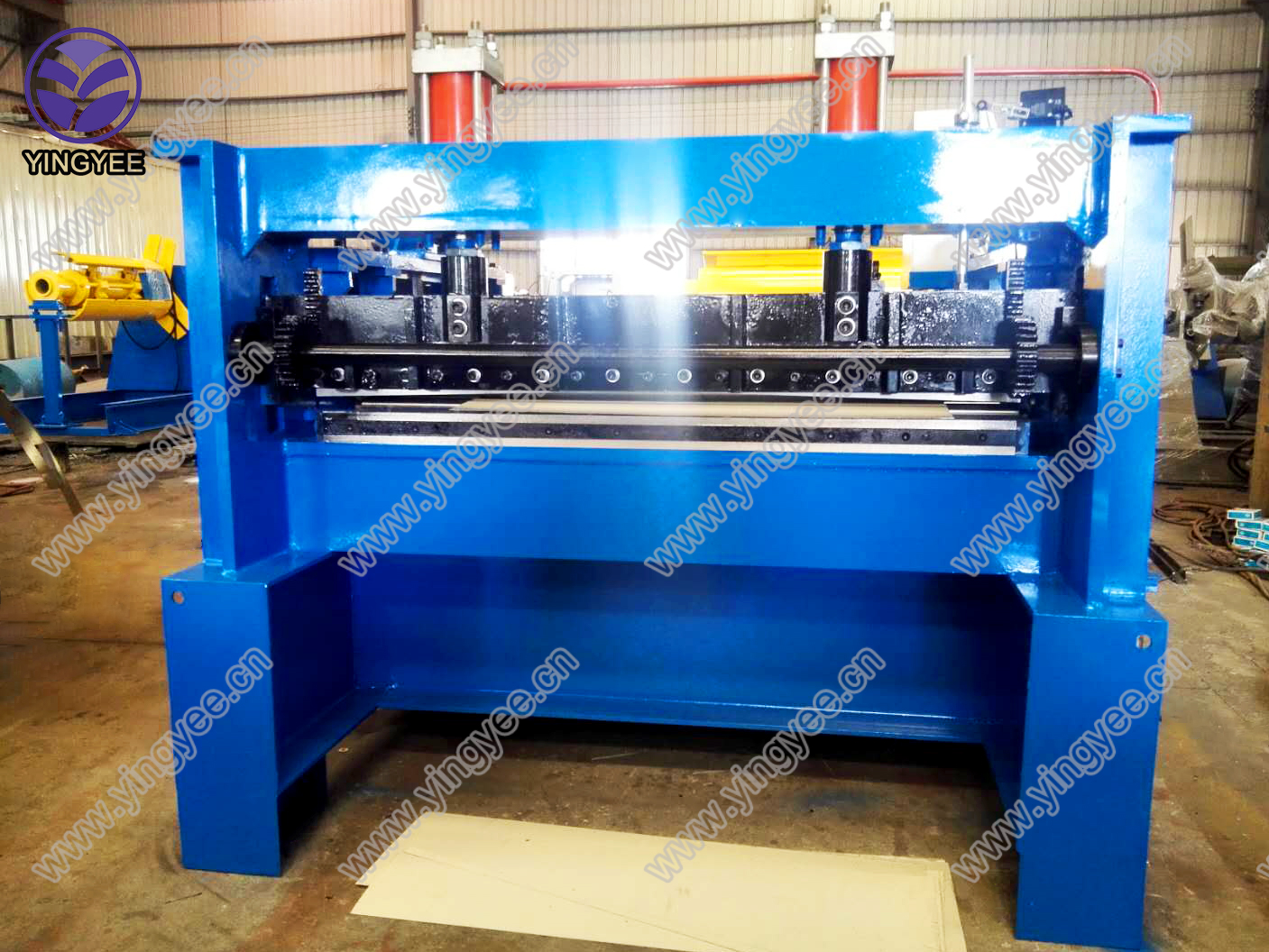
Expertise in deploying crash barrier cold bending machines hinges on understanding the intricacies of both the machinery and the materials being used. Machines today incorporate sophisticated CNC (Computer Numerical Control) technologies, allowing for precise manipulation of materials. This precision results in barriers that are tailored to exact specifications, an essential factor in ensuring that they perform their protective roles as expected. Professionals skilled in operating these machines are highly sought-after, as they bring knowledge that helps optimize machine settings, minimize waste, and maximize the efficiency of the production process.
crash barrier cold bending machine
Authoritativeness in this domain is bolstered by the stringent compliance standards that crash barrier cold bending machines must meet. Globally, road safety standards dictate specific parameters for strength, flexibility, and impact resistance, among other factors. Only machines and products that meet these rigorous standards can be deemed suitable for installation on public roads. Manufacturers that operate within these parameters not only ensure compliance but also enhance their reputation as leaders capable of delivering reliable safety solutions. Innovations in this space often stem from collaborative efforts with research institutions and ongoing investments in R&D, ensuring that products are not just meeting but exceeding current standards.
Trustworthiness is the cornerstone of any safety-related product, and for crash barrier cold bending machines, it manifests in the dependability of the end product. Companies reputed for their reliable machines often have extensive portfolios showcasing their deployment in major infrastructure projects. Testimonials from satisfied clients, documented case studies, and a history of efficient product rollouts are powerful indicators of a company's trustworthiness. Further, the longevity of a manufacturer in the market speaks volumes about their ability to adapt to changing technologies and regulatory landscapes while consistently managing to protect lives and assets.
Prospective buyers of crash barrier cold bending machines should prioritize these factors when considering potential vendors. A thorough evaluation of the vendor's market standing, coupled with insights into their manufacturing and quality assurance processes, is vital. Furthermore, partnerships with companies offering comprehensive after-sales support can greatly enhance user experience, ensuring that the machines function optimally throughout their operational lifespan.
In conclusion, the role of crash barrier cold bending machines in modern infrastructure projects cannot be overstated. These machines bring together cutting-edge technology and essential safety features that contribute immensely to public safety on the roads. For stakeholders involved in infrastructure development, understanding the capabilities and benefits of these machines is crucial for making informed decisions that will impact safety and efficiency both today and in the years to come. As technology continues to push the boundaries of what's possible, the continued evolution of crash barrier cold bending machines will likely yield even greater improvements in road safety measures globally.