The engineering domain has witnessed myriad innovations, yet within the array of technological advancements, the composite floor deck cold bending machine stands as a crucial player in modern construction. This specialized equipment has not only revolutionized the way composite decks are shaped but has also elevated building efficiency, structural reliability, and economic feasibility.
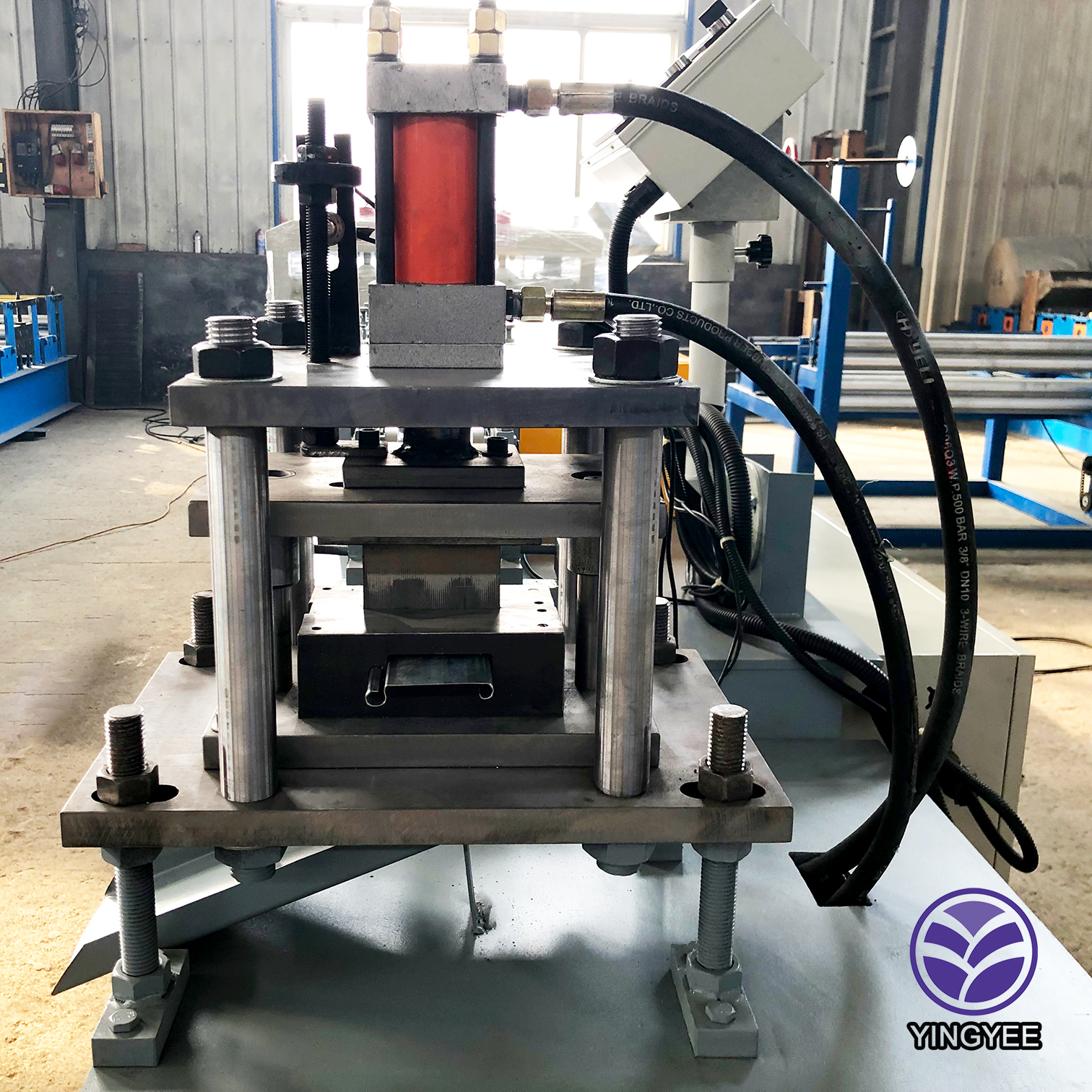
At the heart of its functionality, the composite floor deck cold bending machine is engineered to precision, sculpting deck materials into specific shapes without the need for heat. This cold bending process ensures that materials retain their inherent strength and elasticity, qualities often compromised by thermal processes.
This is pivotal for structural components like floor decks, which must support vast loads while enduring environmental pressures.
From a practical standpoint, one notable advantage of this cold bending machine is its adaptability across various project scales. Whether employed in high-rise buildings or expansive industrial facilities, this machinery provides uniformity in deck production, enhancing overall architectural coherence. This adaptability extends to materials it handles—accommodating a diverse range, from galvanised steel to other composite structures.
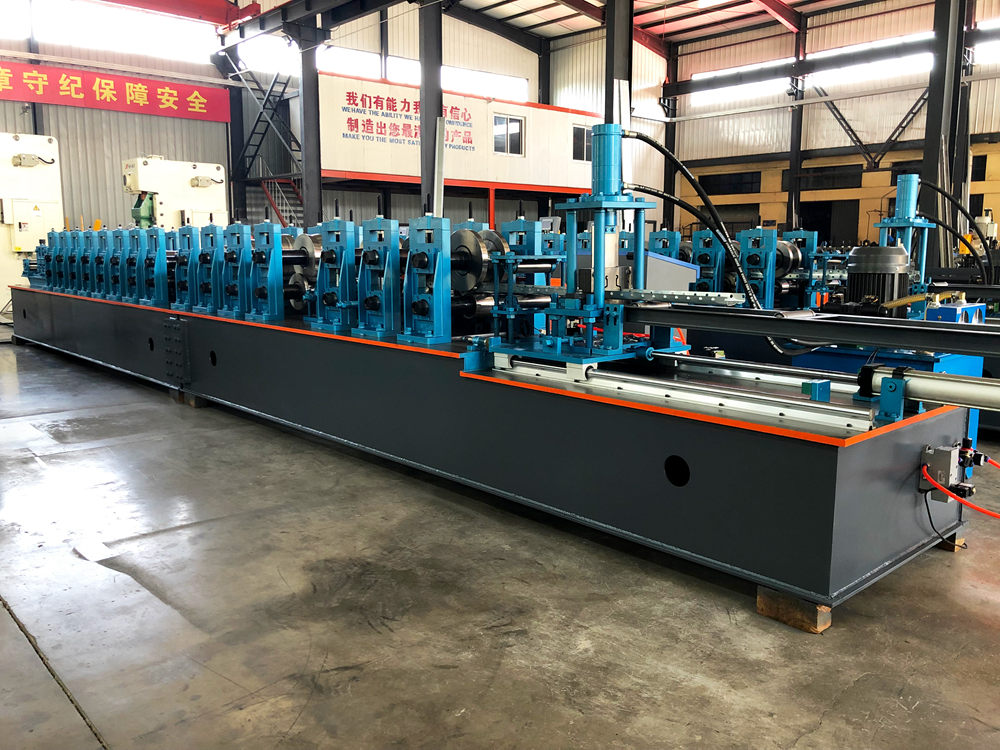
In terms of expertise, operating a composite floor deck cold bending machine demands a synergy of skill and comprehensive understanding of material behavior. Professionals in this field require training to interpret bending specifications accurately, ensuring decks meet precise structural requirements. Certification programs for operators often include modules on machine maintenance, safety protocols, and material science, fostering an environment of professionalism and trust.
The authoritative stance of manufacturers in this niche is underscored by ongoing research and development. By frequently upgrading machine components and software, manufacturers enhance precision and operational efficiency. For instance, the integration of CNC (Computer Numerical Control) technology has allowed refined control over the bending process, reducing material wastage while ensuring exact adherence to design blueprints. Such continuous advancements in machine technology not only bolster the reliability of composite floor decks but also cement the authority of these machines in the construction sector.
composite floor deck cold bending machine
Trustworthiness is further solidified by strict adherence to industry standards and rigorous quality control processes. Machines are regularly inspected for compliance with international safety and efficiency regulations, which in turn guarantees that construction outputs meet the highest standards of durability and safety. Collaborations with engineering bodies and participation in industry expos further validate their credibility, as they align machine specifications with industry expectations.
Investing in a composite floor deck cold bending machine also unfolds an economically sustainable dimension for construction companies. Reduced production timelines and minimized material wastage directly translate into lower project costs. Additionally, the longevity of decks produced through cold bending techniques means reduced maintenance expenses over the life span of a structure. This cost-effectiveness not only appeals to a firm's bottom line but also enhances competitive market positioning.
Finally, the guiding principle behind the design of these machines is sustainability. By minimizing energy consumption and maximizing material efficiency, companies that utilize these machines contribute to environmentally responsible construction practices. This aligns with global trends towards green building certifications, benefiting not only the environment but also company reputation and project value.
In conclusion, the composite floor deck cold bending machine is indispensable in sophisticated construction landscapes, offering an ensemble of benefits that span structural integrity, economic savings, and environmental sustainability. Its precise engineering and pivotal role in shaping reliable, cost-effective components make it a cornerstone in modern structural engineering. As the industry leans into a future of innovation and eco-conscious practices, these machines are sure to remain at the forefront, reshaping not just decks but the very blueprints of modern architecture.