Investing in a cold purling roll forming machine represents a critical decision for manufacturers focused on efficiency and quality in their construction projects. Unlike hot-rolled steel processing, cold purling provides distinct advantages through its ability to produce highly precise and durable steel purlins, which are fundamental to structural frameworks in various building projects.
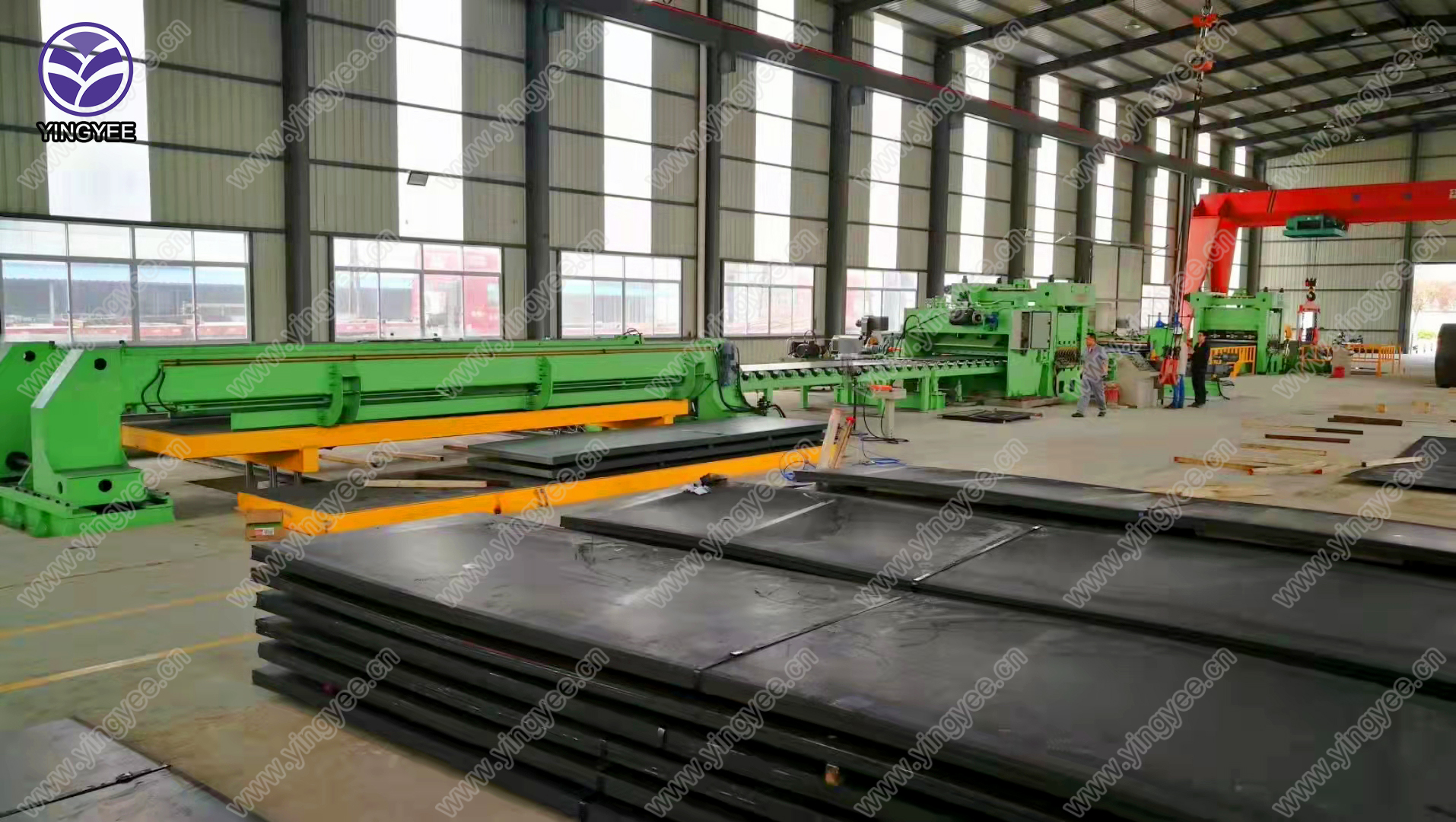
Experience underscores the transformative impact of integrating a cold purling roll forming machine into a manufacturing line. Companies that have embraced this technology report a significant increase in production speed and a drastic reduction in material waste. By utilizing cold roll forming, manufacturers are able to produce consistent profiles with tight tolerances, ensuring that components fit seamlessly during assembly, minimizing construction delays, and enhancing the structural integrity of the project.
In terms of expertise, cold purling roll forming machines harness sophisticated engineering principles to deliver unmatched precision. These machines are designed to handle varying thicknesses and grades of steel, allowing for customization according to project specifications. State-of-the-art advancements in computer-aided design (CAD) and manufacturing (CAM) technologies have been pivotal in enhancing the design capabilities of these machines. By simulating different roll forming processes, engineers are able to optimize the production of profiles in real-time, ensuring the highest quality standards are consistently met.
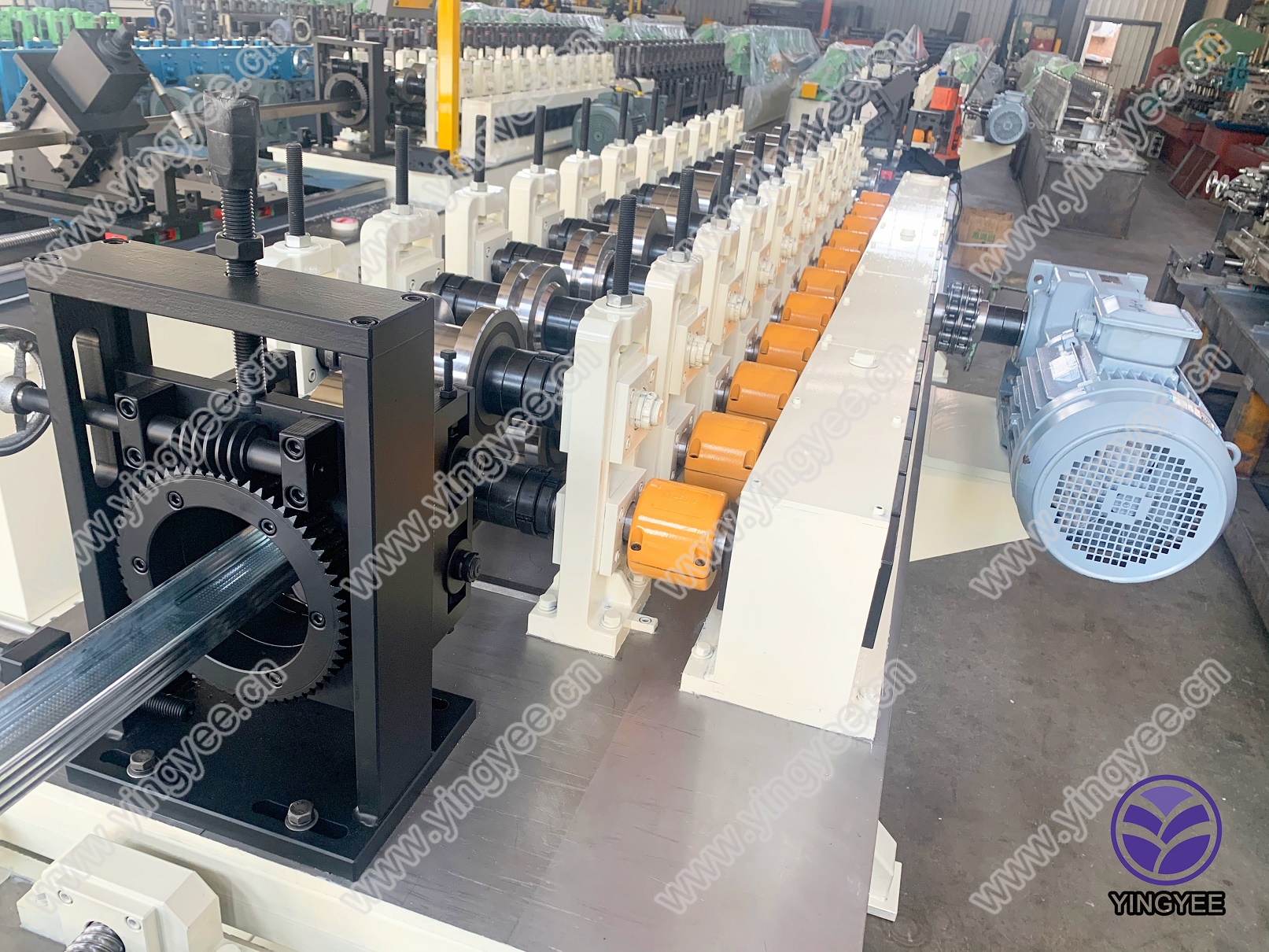
Authoritativeness in the field of cold purling roll forming is bolstered by the machine's compliance with stringent international standards. Acclaimed industry experts often laud these machines for their durability and efficiency. Their ability to accommodate diverse materials and complex geometries without compromising performance is a testament to their engineering excellence. Manufacturers that operate these machines build a reputation for reliability and expertise, frequently becoming leaders in their sectors by offering structurally advanced solutions that stand the test of time.
Trustworthiness, a cornerstone of long-term business relationships, is inherent in the continued usage and endorsement of cold purling roll forming machines by leading corporations worldwide. The machines are not only cost-effective but also demonstrate a high return on investment due to their longevity and minimal maintenance requirements. Automated features have improved operational efficiency, reducing the need for manual oversight and decreasing human error, which contributes to a safer production environment.
cold purling roll forming machine
Strategically investing in a cold purling roll forming machine translates to a competitive edge in the construction and manufacturing industry. It provides the ability to meet tight deadlines without compromising quality, a critical factor for maintaining client trust and securing future contracts. By increasing throughput while maintaining low operational costs, companies can offer more competitive pricing, expanding their market reach and improving profitability.
The lifecycle of a cold purling roll forming machine is enhanced by robust technical support and readily available spare parts. Manufacturers typically offer comprehensive training programs for operators, ensuring the machines are used to their full potential. This focus on education ensures operators are not only familiar with the mechanical operation but also equipped with the troubleshooting skills necessary to maintain productivity even when minor issues arise.
Moreover, sustainability practices are increasingly important in today's manufacturing landscape. Cold purling roll forming machines contribute to eco-friendly manufacturing processes by reducing material waste and providing energy-efficient operations. The precision of these machines reduces the need for extensive post-production finishing, eliminating additional processes that traditionally consume energy and resources.
In conclusion, the adoption of cold purling roll forming machines underscores a commitment to innovation, quality, and efficiency. Companies prioritizing these areas are better positioned to meet evolving industry demands and sustain growth in a competitive market. Reducing downtime and operational costs, maintaining high-quality standards, and offering versatile production capabilities are benefits that transcend traditional manufacturing challenges, setting a new benchmark in the construction and manufacturing sectors.