In the ever-evolving field of metal fabrication, cold bending stands as a pivotal technique known for its efficiency and precision. As with any specialized service, pricing is a significant concern both for providers and their clients. Understanding the elements influencing the cost of cold bending is crucial for manufacturers, architects, engineers, and procurement professionals seeking high-quality results without unnecessary expenditure.
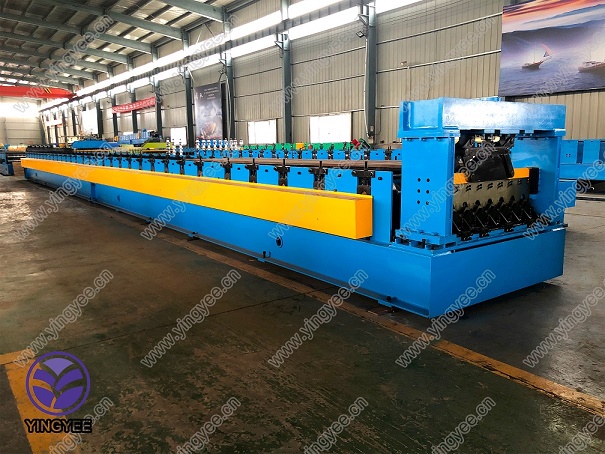
Cold bending, unlike its hot counterpart, involves shaping metal at room temperature. This process maintains the material's structural integrity and properties, which is beneficial for various applications including construction, automotive, and aerospace industries. The expense associated with cold bending hinges on several factors, making it essential for stakeholders to possess a comprehensive grasp of these elements to ensure cost-effectiveness while maintaining quality standards.
Material choice stands at the forefront of cost considerations.
Different metals react uniquely to the bending process. For instance, stainless steel tends to be more expensive than carbon steel due to its durability and resistance to corrosion. The thickness and tensile strength of the metal further influence the pricing. Thicker and harder materials require more energy and sophisticated machinery to bend, escalating operational costs.
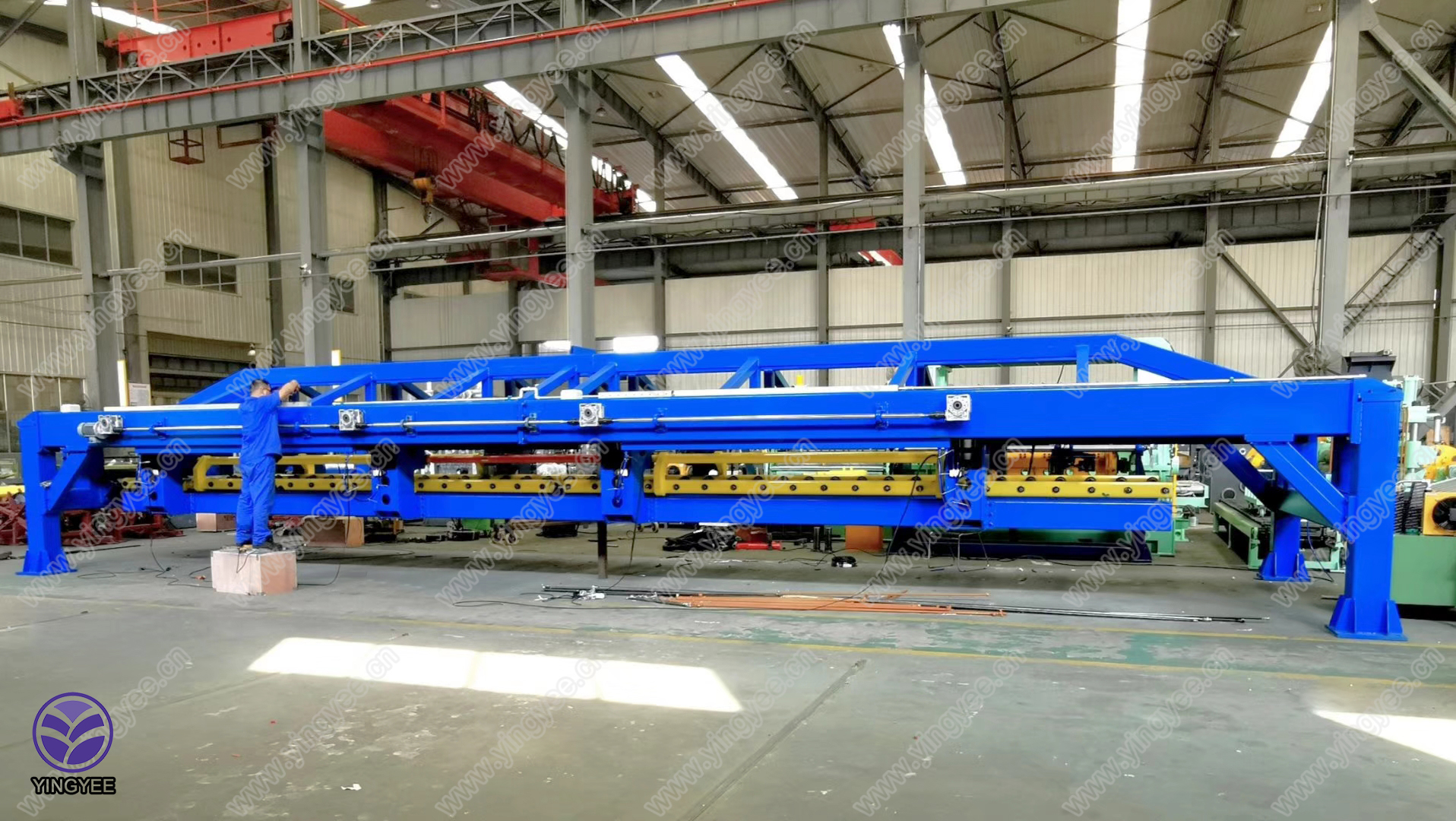
The complexity of the bending project is another crucial determinant. Simple bends may be achieved with basic tooling, while intricate designs necessitate advanced equipment and skilled operators. Customization often requires additional tooling and programming input, which can elevate the overall cost. Moreover, if a project demands high precision and tight tolerances, expect the need for high-quality machines and experienced operators, which further contributes to cost.
Volume also plays an integral role in determining price points. Bulk projects benefit from economies of scale; the cost per unit is reduced as the volume of production increases. Conversely, limited-run productions may incur higher per-unit costs due to the setup time and resource allocation involved, which are not spread over a large quantity of products.
cold bending price
The expertise and reputation of the service provider cannot be overlooked. Companies with a well-established track record and a reputation for excellence often command higher fees due to their proven reliability, quality outcomes, and professional certifications. Such providers typically invest in the latest technology and ongoing staff training, ensuring efficiency and precision in project delivery.
Geographical location is another cost factor. Facilities located in regions with high labor costs or stringent regulatory requirements may charge more compared to those in areas where operational costs are lower. It is crucial for clients to weigh these geographic considerations against potential logistical challenges, such as shipping time and costs, when selecting a provider.
To ensure a trustworthy transaction and outcomes, clients should conduct thorough research, seek multiple quotes, and verify the credentials of service providers. An informed decision balances quality, cost, and reliability, leading to successful project completion without undue financial expenditure.
In conclusion, navigating the pricing landscape of cold bending requires a nuanced understanding of material characteristics, project complexity, production volume, provider expertise, and geographic implications. By thoroughly evaluating these factors, stakeholders can make informed decisions that align with both their budgetary constraints and performance requirements, ultimately optimizing their investment in metal fabrication services.