Cold Bending Machinery Revolutionizing Manufacturing
In the realm of modern manufacturing, cold bending machinery has emerged as a pivotal tool that redefines the way metal components are shaped and formed. Unlike traditional hot bending processes which involve heating materials to high temperatures to make them pliable, cold bending operates at ambient temperatures. This method offers numerous advantages, including reduced energy consumption, minimized thermal distortion, and enhanced precision in the final product.
Cold bending machinery employs a variety of techniques such as roll bending, press braking, and three-roll bending to name a few. These machines are designed to handle a wide range of metals, from aluminum and stainless steel to harder alloys like titanium, with remarkable accuracy and repeatability. The technology behind these machines is continuously evolving, integrating advanced computer systems that allow for complex shapes and angles to be bent with minimal waste.
One of the key benefits of cold bending is its ability to maintain the material's strength and integrity. Since no heat is applied, the materials retain their original properties post-formation. This is particularly crucial in applications where component strength and reliability are paramount, such as in the construction of aircraft, automobiles, and high-end machinery.
Moreover, cold bending machinery contributes to sustainability efforts in manufacturing
Moreover, cold bending machinery contributes to sustainability efforts in manufacturing
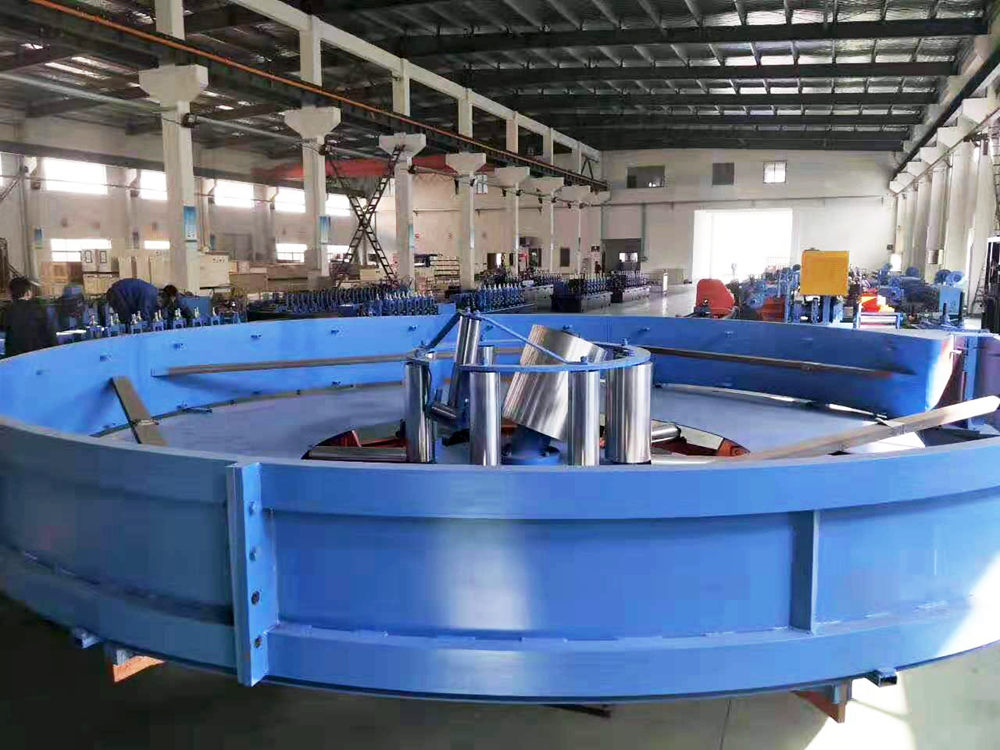
Moreover, cold bending machinery contributes to sustainability efforts in manufacturing
Moreover, cold bending machinery contributes to sustainability efforts in manufacturing
cold bending making machinery. By reducing energy needs and minimizing material waste, it aligns with environmental stewardship goals. The process also reduces the need for cooling systems required in hot bending operations, further enhancing energy efficiency.
As we look towards the future, the role of cold bending machinery is set to expand even further. With advancements in automation and artificial intelligence, these machines will become even more sophisticated, capable of self-diagnosing issues and adapting to changing production requirements in real-time. They will continue to push the boundaries of design, making possible what was once considered too complex or cost-prohibitive to manufacture.
In conclusion, cold bending machinery stands at the forefront of manufacturing innovation, enabling industries to shape metals with unparalleled precision and efficiency. As technology progresses, the potential applications for this machinery will only broaden, promising a future where manufacturing is not only more productive but also more sustainable and economical.