In the ever-evolving landscape of metal processing, the coil metal cut to length line stands out as a pivotal advancement that addresses the precise requirements of industries ranging from automotive to construction. This sophisticated equipment transforms master coils into flat sheets or plates of predetermined lengths, ensuring accuracy and efficiency.
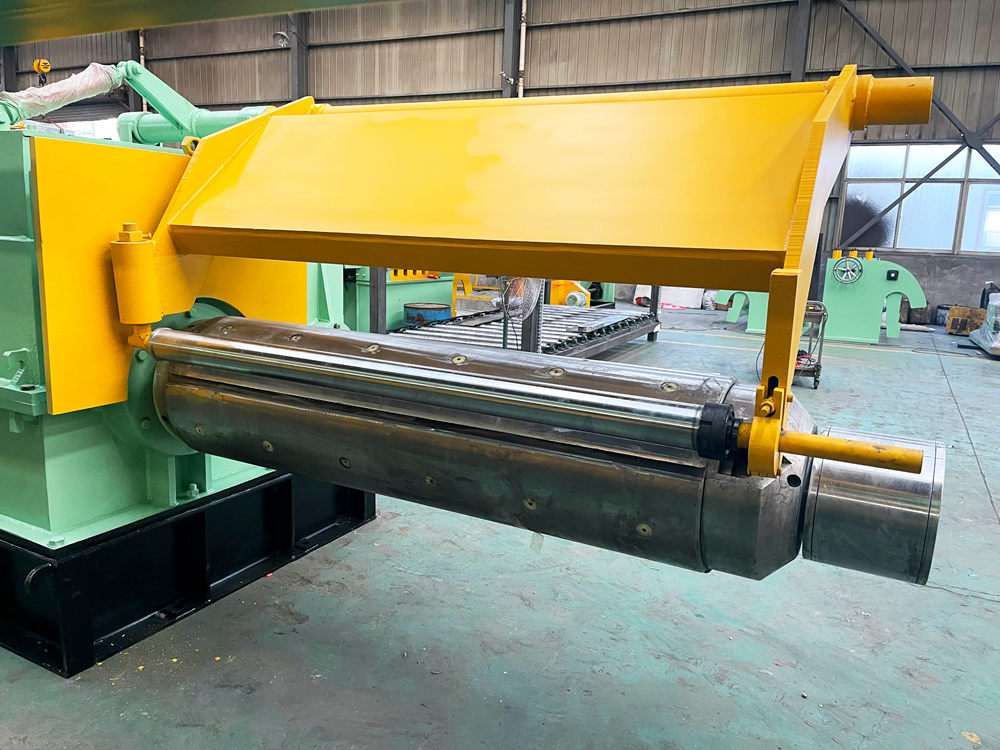
The journey of coil metal to a finished cut to length line begins with an uncoiler, responsible for feeding the metal sheet into the line. This stage is crucial, as it sets the tone for precision. The uncoiler must handle various coil weights, widths, and materials, underscoring the necessity for a robust and adaptable machine. Advanced uncoilers today come equipped with automated centering and hydraulic systems to accommodate diverse coil dimensions without human intervention, which enhances both safety and speed.
Once the coil is uncoiled, it passes through the straightening process. This phase is instrumental in eliminating the natural curvature from the coiled metal. Using a combination of levelers and precision rollers, the metal is flattened effectively. The straightening ensures uniformity and prepares the metal for subsequent processing stages. Professionals in the industry emphasize the significance of this step, as any imperfection can impact the final product's integrity and fit.
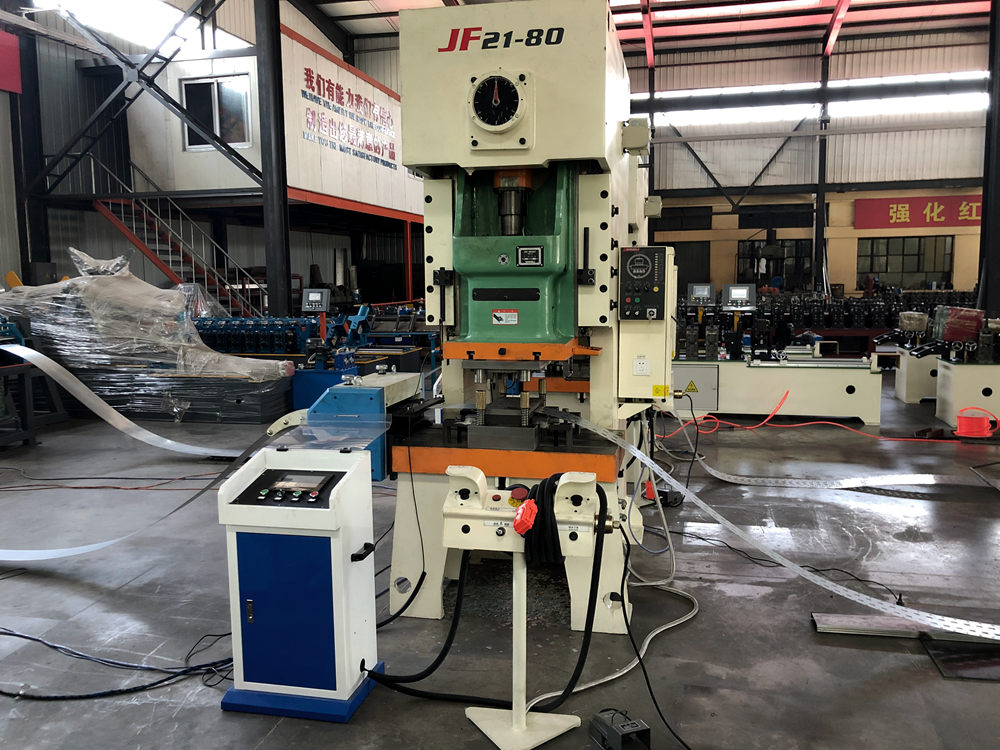
Following straightening, the metal encounters the cutting unit. This section is designed to deliver the exact dimensions required by the user. With an array of cutting techniques, such as rotary shearing and flying shearing, cut to length lines can achieve remarkable accuracy. The choice between these methods hinges on the material type and desired output rate. Rotary shearing, characterized by continuous operation, suits fast-paced environments, while the precision of flying shearing meets more exacting standards.
Moreover,
automation plays an integral role in the cut to length process. Modern lines are increasingly equipped with CNC controls and digital user interfaces, allowing operators to input specific dimensions and align the machinery accordingly. This technological leap minimizes human error, enhances safety, and bolsters productivity. These systems can store and recall customized settings for repeat orders, offering unparalleled efficiency for manufacturers dealing with large batch productions.
coil metal cut to length line
Experienced operators highlight the importance of routine maintenance to retain optimal functioning of cut to length lines. Scheduled checks on lubrication, alignment, and system diagnostics are essential to prevent downtimes and costly repairs. A reliable maintenance schedule not only extends the machinery's working life but also ensures consistent product quality, thereby solidifying the manufacturer's reputation for reliability.
Investing in a high-quality coil metal cut to length line has a significant impact on production capabilities. The ability to deliver bespoke sheet dimensions with precision reduces material wastage and, consequently, operational costs. Companies specializing in these systems provide comprehensive training and support to maximize the benefits of their machinery. Industry experts emphasize that understanding the intricacies of each component and its function within the line is critical, as it empowers operators to troubleshoot potential issues promptly.
The trustworthiness of a cut to length line provider is often measured by their portfolio of successful implementations and client testimonials. Companies seek assurances of consistent performance, support services, and ongoing innovation. Providers offering these assurances often rise as leaders, showcasing not just expertise but commitment to their customers' success.
In conclusion, a coil metal cut to length line embodies precision, efficiency, and technological advancement. It is an indispensable element for manufacturers aiming to streamline operations and deliver exceptional quality. As industries continue to demand tailor-made solutions, the role of these sophisticated lines becomes ever more critical in meeting the dynamic needs of modern production environments.