The Innovation of Perforated Cable Tray Manufacturing with Cold Roll Forming Machines
The advent of perforated cable tray cold roll forming machines represents a significant leap forward in the manufacturing sector, particularly for businesses involved in electrical infrastructure and cable management. This innovative technology streamlines the production process of perforated cable trays, which are essential for protecting and organizing wires and cables in various settings such as industrial, commercial, and data centers.
Perforated cable trays offer ventilation and allow for the efficient dissipation of heat generated by the cables. Traditionally, producing these trays has been a labor-intensive process that often involves multiple steps and equipment. However, with the introduction of cold roll forming machines specifically designed for this purpose, manufacturers can now enjoy increased efficiency and reduced production costs.
Cold roll forming is a process whereby sheet metal is gradually shaped through consecutive sets of rollers, without the use of heat. This method preserves the material's strength and integrity while allowing for precise and consistent profiles to be created. When applied to the manufacture of perforated cable trays, the cold roll forming technique ensures a high degree of accuracy and repeatability in the finished products.
The machinery used in this process is specially configured to handle the specific requirements of perforated cable tray designs. It can be programmed to punch holes of desired sizes and patterns directly into the material as it is being rolled, thus eliminating additional punching or drilling steps It can be programmed to punch holes of desired sizes and patterns directly into the material as it is being rolled, thus eliminating additional punching or drilling steps
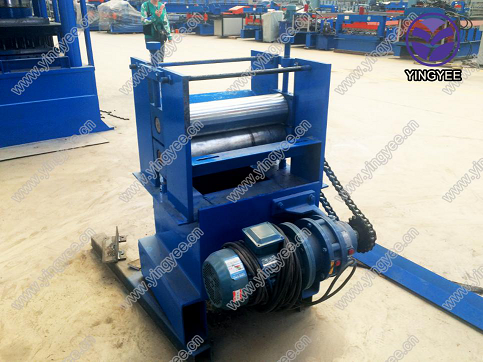
It can be programmed to punch holes of desired sizes and patterns directly into the material as it is being rolled, thus eliminating additional punching or drilling steps It can be programmed to punch holes of desired sizes and patterns directly into the material as it is being rolled, thus eliminating additional punching or drilling steps
perforated cable tray cold roll forming machine. The speed and consistency of the cold roll forming machine also mean that long lengths of perforated cable tray can be produced continuously, reducing material waste and increasing output.
Furthermore, the use of cold roll forming machines for perforated cable trays opens up possibilities for customization and innovation. Manufacturers can easily adjust the machine settings to produce trays with different widths, depths, and hole patterns to meet the unique needs of their clients. This flexibility not only enhances customer satisfaction but also allows manufacturers to diversify their product offerings and stay competitive in the market.
In conclusion, the integration of cold roll forming machines in the production of perforated cable trays signifies a technological advancement that benefits both manufacturers and end-users. It leads to faster production times, lower costs, improved product quality, and increased customization options. As we continue to rely more heavily on complex electrical systems in various environments, the demand for efficient and effective cable management solutions like perforated cable trays will undoubtedly grow, making this innovation all the more valuable.