The Revolution in Construction Drywall Roll Forming Machines
Drywall roll forming machines have revolutionized the construction industry by streamlining the production process of drywall panels, significantly enhancing efficiency and productivity. These advanced machines are designed to manufacture high-quality drywall sheets with precision, speed, and consistency, making them an indispensable tool for modern construction sites.
Drywall, also known as gypsum board, is a widely used material in interior construction due to its fire-resistant properties, sound insulation, and ease of installation. The traditional method of manufacturing drywall involved manual processes, which were time-consuming and labor-intensive. However, with the advent of drywall roll forming machines, this has changed dramatically.
A drywall roll forming machine typically consists of several components, including an unwinding device, forming rollers, cutting system, and a stacking unit. The process begins with a large roll of steel or paper substrate being fed into the machine. The substrate passes through a series of precisely engineered rollers that shape and form it into the desired thickness and profile of a drywall panel. The core material, usually gypsum, is then applied and bonded to the substrate, followed by a final coating for added strength and finish.
The cutting system, often equipped with advanced computer-aided design (CAD) and control technology, accurately slices the formed panels to specific lengths. The finished panels are then neatly stacked by the stacking unit, ready for transportation to the construction site The finished panels are then neatly stacked by the stacking unit, ready for transportation to the construction site
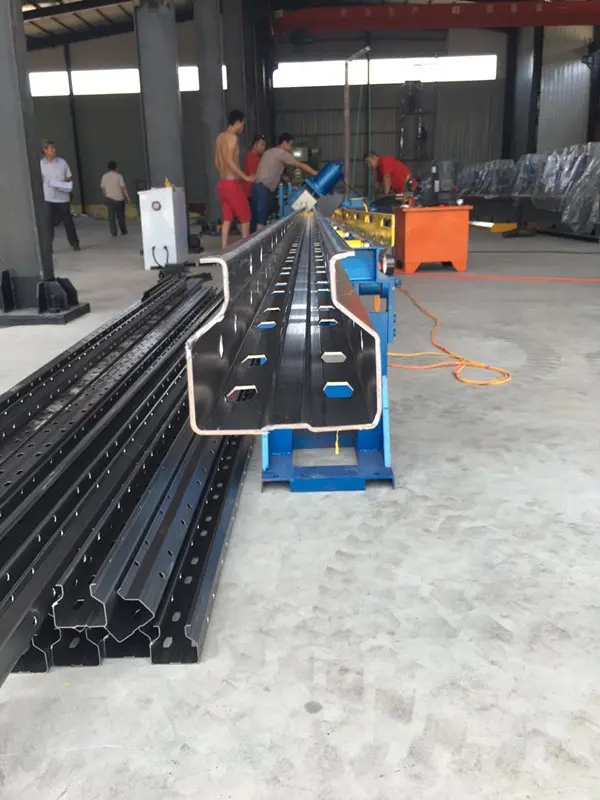
The finished panels are then neatly stacked by the stacking unit, ready for transportation to the construction site The finished panels are then neatly stacked by the stacking unit, ready for transportation to the construction site
drywall roll forming machine. This entire process can be completed at a remarkable speed, often producing hundreds of panels per hour.
One of the key advantages of drywall roll forming machines is their ability to customize panel dimensions according to project requirements. This flexibility ensures that builders can easily accommodate diverse architectural designs and space configurations. Moreover, these machines operate with minimal waste, reducing material costs and environmental impact.
In addition to increased productivity and cost-effectiveness, drywall roll forming machines also enhance workplace safety. By automating hazardous tasks, they minimize the risk of injury to workers, fostering a safer work environment. Furthermore, the consistent quality of machine-made panels ensures a higher standard of construction, leading to more durable and reliable buildings.
In conclusion, drywall roll forming machines have transformed the way drywall is manufactured, bringing about a new era of efficiency, precision, and sustainability in the construction industry. As technology continues to advance, we can expect even more innovative solutions that will further optimize the production process and contribute to the evolution of modern construction practices.