Cold bending is a crucial process in various industries, especially in metal fabrication where precision and accuracy are paramount. Cold bending involves bending materials, typically metals, at room temperature, ensuring the structural integrity of the material is retained. Understanding the nuances of cold bending and the costs associated with it is essential for manufacturers and builders who aim to optimize their operations both in terms of quality and cost-efficiency.
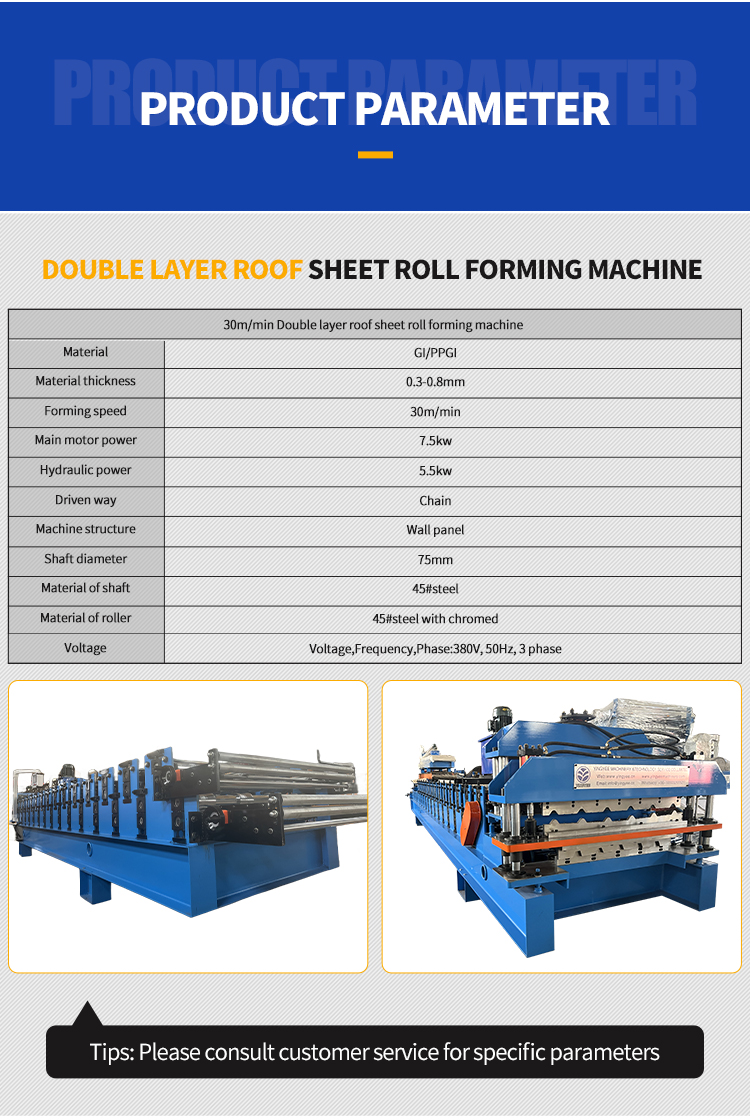
The dynamics of cold bending pricing can be influenced by several factors, each playing a significant role in the final cost estimation for a project. Material type is one of the primary determinants of cold bending price. Different metals will require distinct approaches and equipment, impacting the overall expense. For instance, bending steel might necessitate more robust machinery compared to bending aluminum, due to steel’s higher strength and rigidity.
Another crucial factor is the thickness and dimensions of the material. Thicker and larger pieces often require more energy and sophisticated machinery to achieve the desired bends without compromising the material's structural properties. This, in turn, contributes to a higher cost. Additionally, the complexity of the bend also affects the price. Simple, uniform bends are generally less costly than intricate, non-uniform shapes which demand precision engineering and advanced tools.
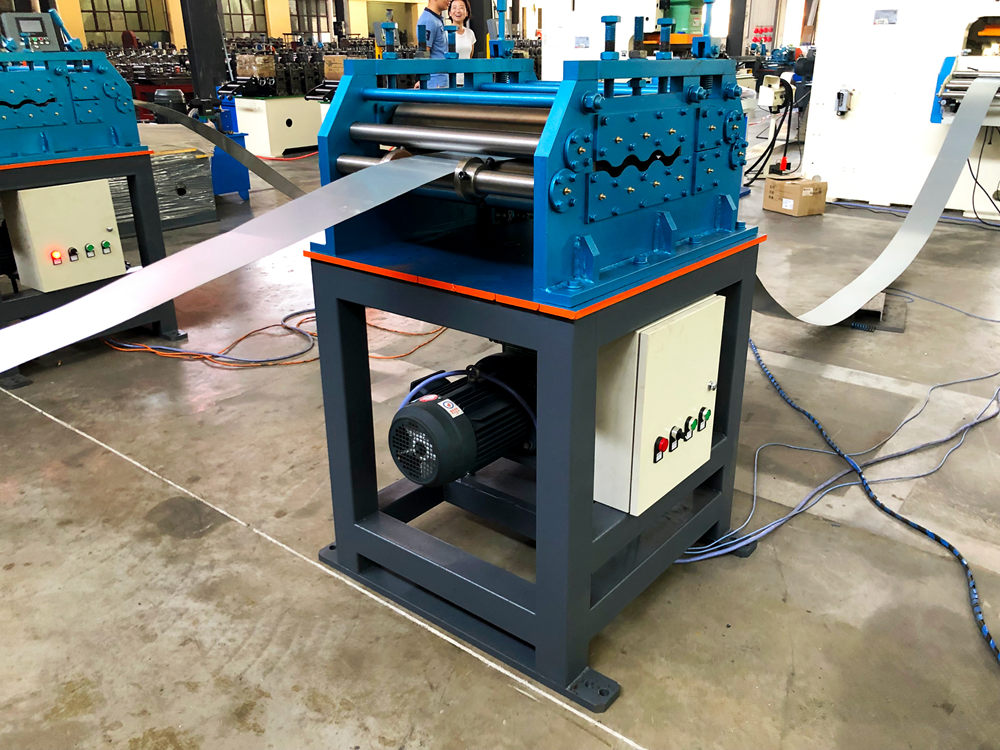
The type of equipment used in the bending process significantly impacts cost as well. Modern CNC (Computer Numerical Control) machines, while characterized by high accuracy and efficiency, can be a significant investment for a business. However, they often lead to lower per-unit costs thanks to reduced labor requirements and faster processing times. On the other hand, manual bending processes might lower initial investment but could increase labor costs and processing time.
Labor costs themselves are another variable in the pricing equation. Skilled operators command higher salaries due to their expertise and the precision required in cold bending operations. Companies must balance between employing skilled workers and the automation of processes to maintain cost-effectiveness while ensuring high-quality outputs.
cold bending price
Transportation and logistics also introduce variables into cold bending pricing. The location of the fabrication facility relative to the raw material suppliers and the project site can influence costs due to shipping and handling charges. Efficient planning in locating facilities closer to key partners might mitigate excessive logistical expenses.
Furthermore, market fluctuations can impact materials’ prices, altering the baseline cost of cold bending. Economic conditions, supply chain disruptions, and demand variations all affect raw material availability and costs, thereby influencing the overall pricing strategy. Staying informed about market trends and maintaining flexible pricing structures can help organizations manage these uncertainties and remain competitive.
Investing in sustainable practices can potentially reduce the long-term costs associated with cold bending. By incorporating energy-efficient machinery and environmentally friendly processes, companies not only contribute positively to the environment but also often enjoy reductions in operational costs. Additionally, aligning with environmental standards can open up opportunities for government incentives or funding, indirectly affecting overall cost efficiency.
Understanding these elements underscores the importance of a thorough cost analysis before embarking on a cold bending project. Employing a combination of skilled labor, advanced technology, and strategic logistical planning can optimize pricing without sacrificing quality.
By focusing on these aspects, businesses can foster a greater understanding among stakeholders about the intricacies involved in cold bending pricing. Through diligent strategy formulation, a balance between cost-efficiency and top-tier product quality can be achieved, enhancing both profitability and market position. Engaging in continuous learning and adaptation based on emerging trends ensures long-term success in the highly competitive fabrication industry.