The structural roof deck cold bending machine represents a pivotal advancement in the construction industry, engineered to effortlessly shape metal decking to precise architectural specifications. With ever-evolving construction demands, this machinery stands as a testament to innovation, combining robust engineering with sophisticated automation to deliver unparalleled efficiency and precision.
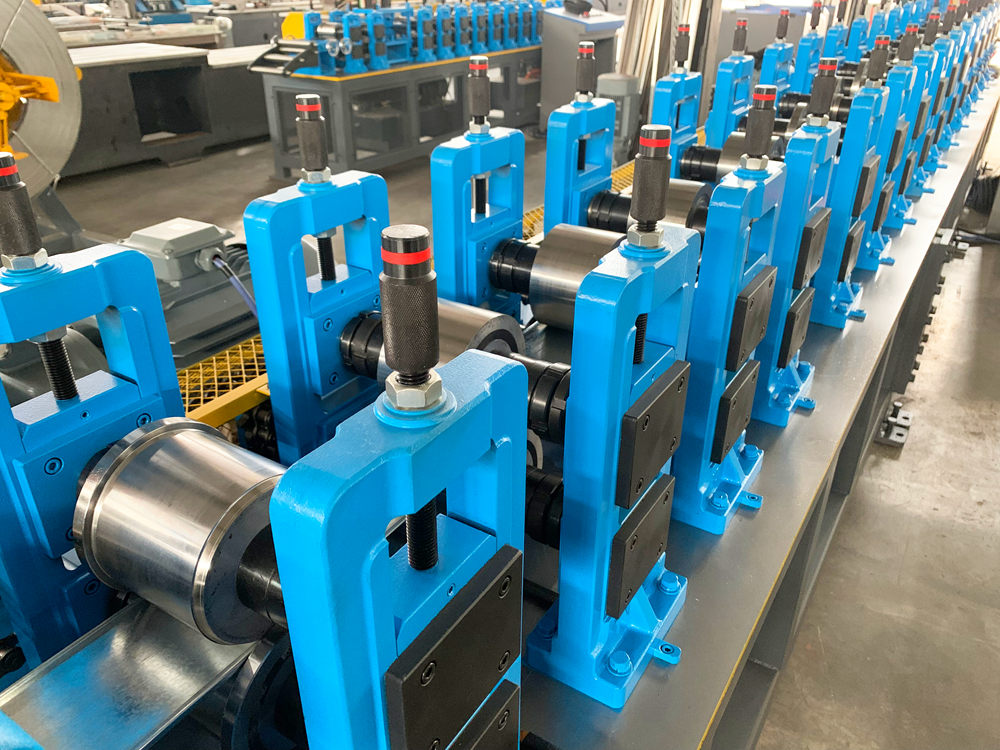
For contractors and architects aiming to enhance structural integrity and aesthetic appeal,
the cold bending machine offers a tailored approach to metal shaping, minimizing errors and maximizing output. Unlike traditional methods, which often involve manual labor and a higher margin for inaccuracies, the cold bending machine automates the process, allowing for consistent production of curved metal decking that meets stringent industry standards.
One of the machine's key features is its user-friendly interface which demystifies the bending process, allowing operators—even those with minimal technical training—to oversee production seamlessly. This intuitive system is augmented by advanced sensors and precision controls, ensuring that each sheet of metal is bent to exact specifications, reducing waste, and enhancing material utilization.
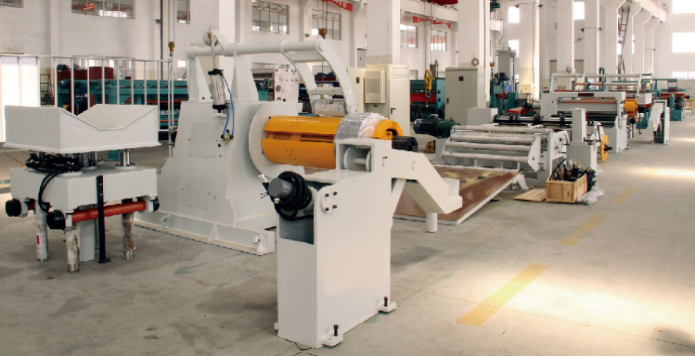
Expertise in deploying the structural roof deck cold bending machine is rapidly becoming a valuable asset within the construction sector. With a deep understanding of metallurgy and mechanical engineering principles, professionals can manipulate the machine to accommodate various types of metals, including steel, aluminum, and other alloys, each with unique properties and bending requirements. This versatility makes the machine indispensable across diverse project scopes, from residential developments to large-scale industrial complexes.
Trust in the efficacy of the structural roof deck cold bending machine is fortified by a growing body of evidence showcasing its performance in real-world scenarios. Across numerous case studies, the machine has demonstrated capacity improvements, with anecdotal reports of up to a 30% increase in bending speed compared to legacy systems. Notably, this capability does not compromise the safety standards, as built-in safety protocols ensure the machine operates within defined limits, protecting both the machinery and its operators.
structural roof deck cold bending machine
Furthermore, the machine's environmental impact is minimal when compared to traditional bending methods. By optimizing energy usage and reducing material wastage, it contributes to sustainable building practices. Contractors focused on green building certifications appreciate the machine's efficiency, as it aligns with contemporary environmental guidelines and client expectations for eco-friendly construction techniques.
The authoritative appeal of the structural roof deck cold bending machine extends to industrial partnerships with leading construction firms and associations. Its design and functionality have been vetted by industry experts, with endorsements highlighting its contribution to elevating structural quality and reducing overhead costs. For firms seeking to obtain a competitive edge, investing in such technology offers a distinct advantage—streamlining operations while ensuring adherence to rigorous safety and quality benchmarks.
As technology continues to shape the future of construction, the importance of integrating reliable, advanced machinery like the structural roof deck cold bending machine cannot be overstated. Whether employed on-site or in prefabrication settings, its capacity to deliver high-quality results efficiently positions it as an essential tool in the modern builder’s toolkit. The trustworthiness of the machine is continuously validated by its consistent performance, setting a new standard for innovation-driven construction solutions.
In conclusion, the structural roof deck cold bending machine is reshaping more than just metal; it is redefining how the construction industry approaches efficiency, safety, and sustainability. By investing in this technology, stakeholders not only ensure compliance with industry standards but also champion a forward-thinking approach to building that prioritizes precision, reliability, and environmental responsibility.