As the demand for innovative infrastructure solutions continues to rise, cutting-edge machinery like the noise barrier cold bending machine is garnering attention for its impressive capabilities. These machines are a crucial part in the construction of acoustic barriers, which are integral in reducing noise pollution in urban and residential areas. Here, we delve into the essential aspects of noise barrier cold bending machines, sharing insights from industry experts, showcasing the high level of expertise that has gone into their development, and exploring the authority and trust they command in the construction industry.
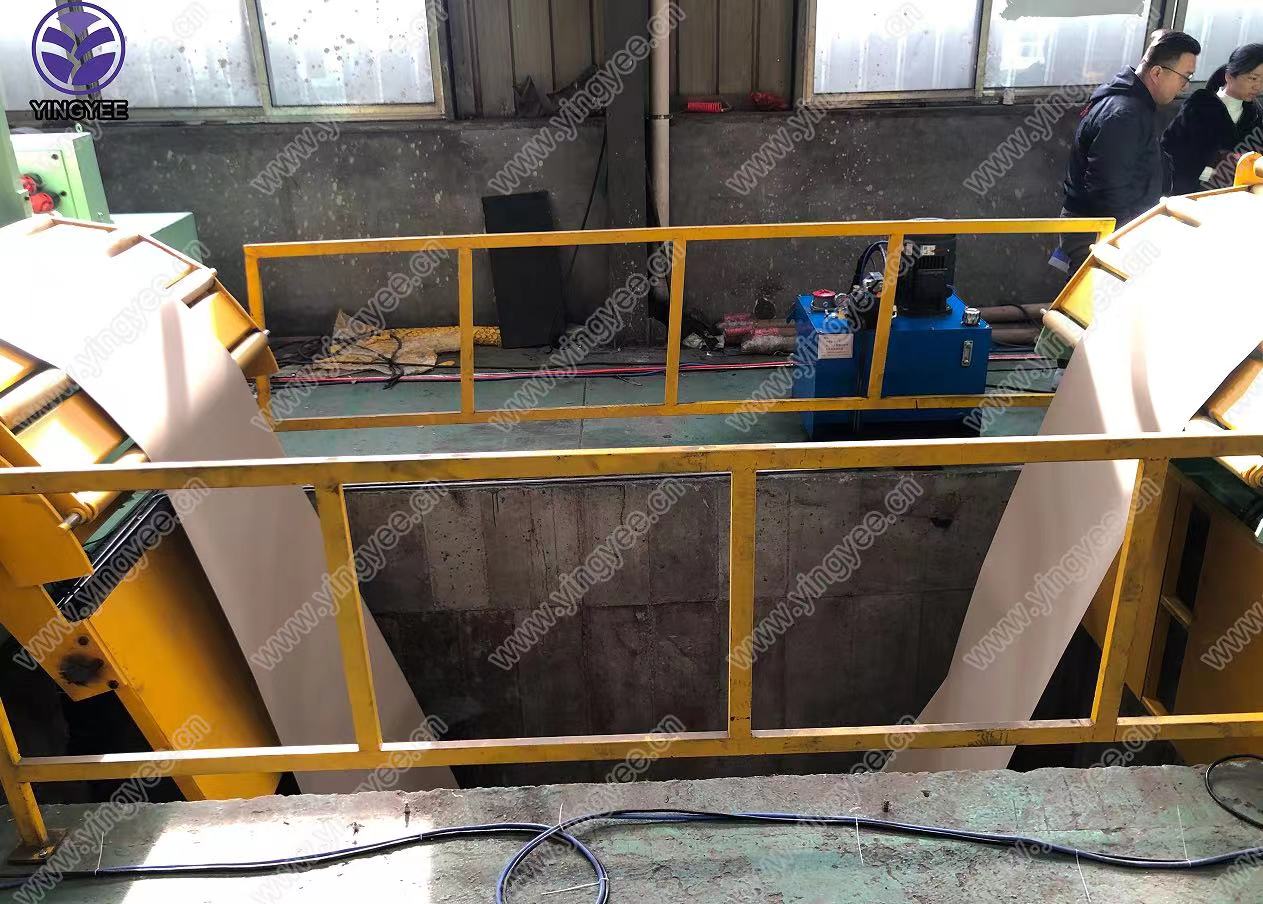
Noise barrier cold bending machines represent a technological breakthrough in the fabrication of sound insulation solutions. Unlike traditional bending methods that use heat, these machines utilize a cold process, allowing for a more precise and efficient production cycle. This innovative technology maintains the material properties without compromising structural integrity, ensuring the barriers are both durable and effective.
Industry specialists emphasize that the primary advantage of these machines lies in their ability to handle a variety of metals and composite materials. This versatility enables them to meet diverse project requirements, from residential sound barriers to large-scale industrial applications. Manufacturers have acknowledged that deploying this machinery dramatically reduces the production time while simultaneously cutting costs. This efficiency stems from the elimination of the heating phase, which shortens operational timelines and reduces energy consumption.
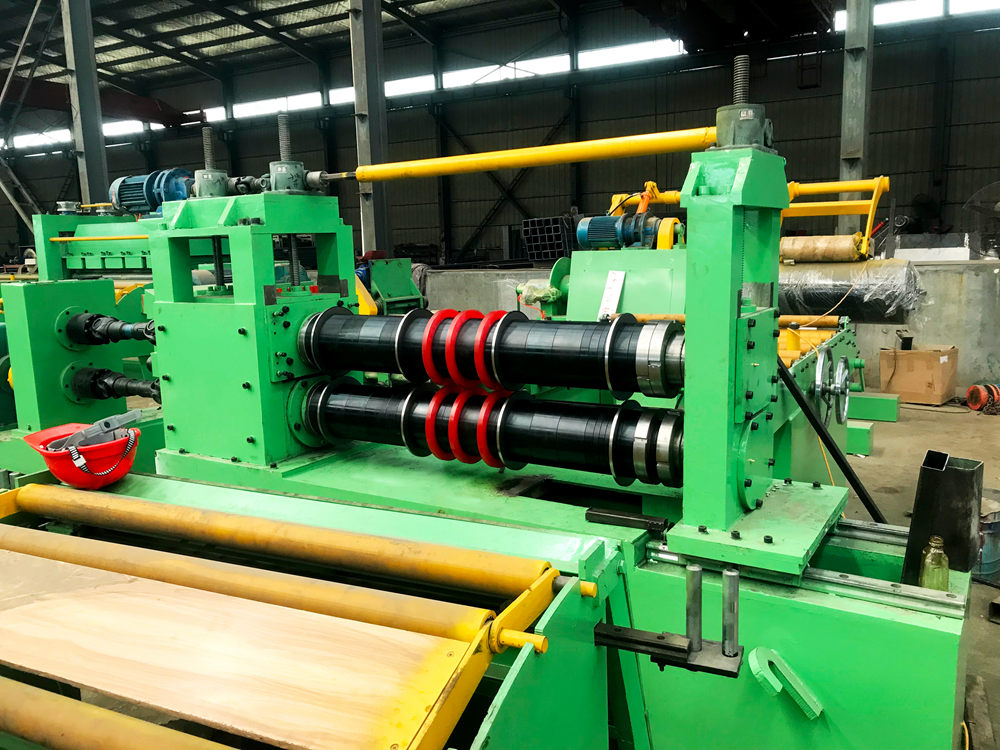
Understanding the intricate functionalities of the noise barrier cold bending machine is vital for stakeholders within the construction sector. Engineers and construction managers who have worked with these machines affirm their reliability and high performance. According to recent field studies, noise barriers produced with cold bending technologies have shown enhanced resilience in adverse weather conditions, leading to extended product life spans. This longevity is crucial for constructions subjected to harsh environmental stresses, such as highways, where traditional barriers might falter over time.
noise barrier cold bending machine
Experts in the field highlight that an integral component of these machines is their software integration capability. This allows seamless interfacing with computer-aided design (CAD) programs, optimizing the design process for noise barriers directly within the production framework. The precision achieved through this integration marks a significant leap in customization capabilities, providing a tailored noise reduction solution for clients, a crucial factor in elevating customer satisfaction.
Furthermore, as cities evolve and environmental considerations become central to infrastructure development, the sustainability of construction processes garners increasing scrutiny. The implementation of noise barrier cold bending machines aligns with eco-friendly construction practices. By minimizing waste and reducing energy use, these machines not only contribute to lower carbon emissions but also align with sustainable development goals, a major consideration for future urban planning endeavors.
When it comes to authoritativeness and trustworthiness, the credibility of the companies that manufacture these machines plays a pivotal role. Leaders in the field, renowned for their progressive engineering solutions, often have decades of experience and are backed by extensive research and development facilities. Certifications and adherence to international quality standards further bolster their reliability, reassuring clients of their commitment to excellence.
In conclusion, the noise barrier cold bending machine emerges as a superior alternative to traditional methods, offering advantages in efficiency, versatility, and sustainability. It provides solutions that meet the ever-growing demands of modern infrastructure projects while fostering a future where urban environments coexist harmoniously with nature. This investment is not merely in machinery but in the commitment to innovation, quality, and environmental responsibility, cornerstone principles that now define the future of noise barrier construction.