In the modern landscape of infrastructure development, guardrail block cold bending machines have emerged as indispensable assets for safety and durability. The essence of these machines lies in their advanced ability to curve and shape metal guardrails through a cold bending process, enabling seamless integration into road and highway safety systems without compromising the material's structural integrity.
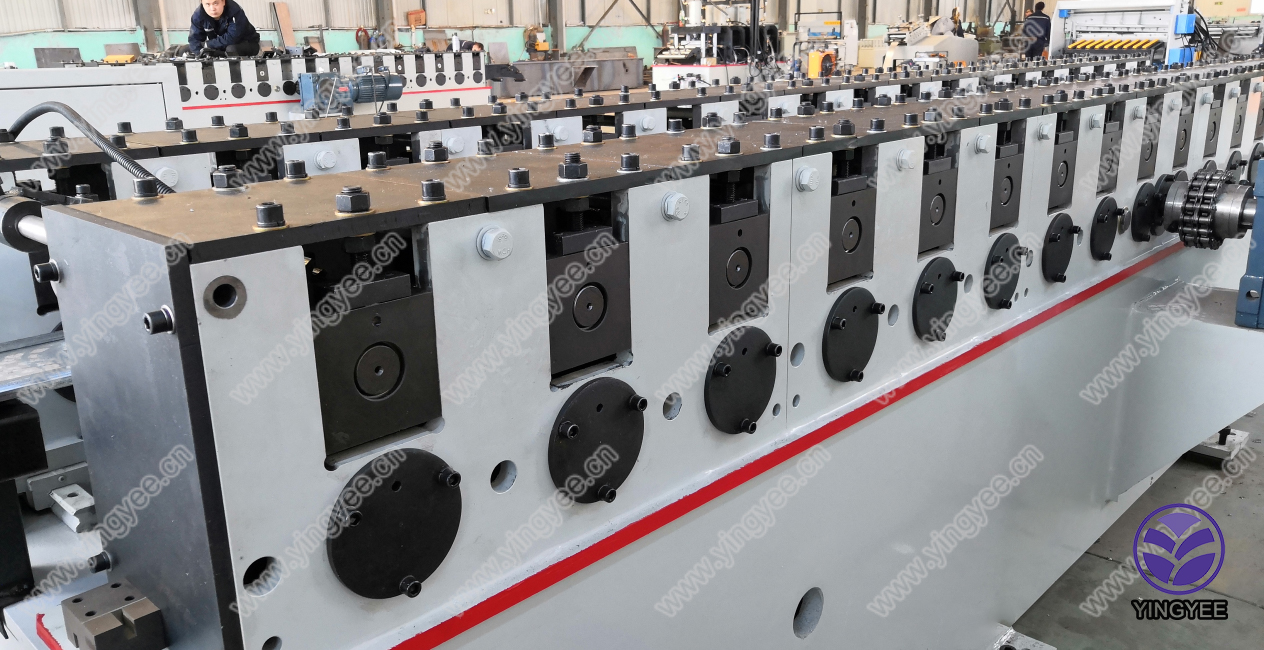
Operating a guardrail block cold bending machine involves a sophisticated confluence of mechanical precision and engineering prowess. Unlike traditional methods that rely on heating, which can alter the metal properties, cold bending maintains the guardrail's tensile strength and flexibility. This not only ensures a longer lifespan but also enhances the guardrail's ability to absorb crash impacts, thus providing a higher degree of safety to motorists.
The design of a modern cold bending machine is the product of cutting-edge technology and engineering expertise. These machines are equipped with robust frameworks and an array of advanced features including CNC control systems that offer unparalleled accuracy and programmability. Such sophisticated automation streamlines the bending process, ensuring that each piece produced meets stringent industry specifications and quality standards.
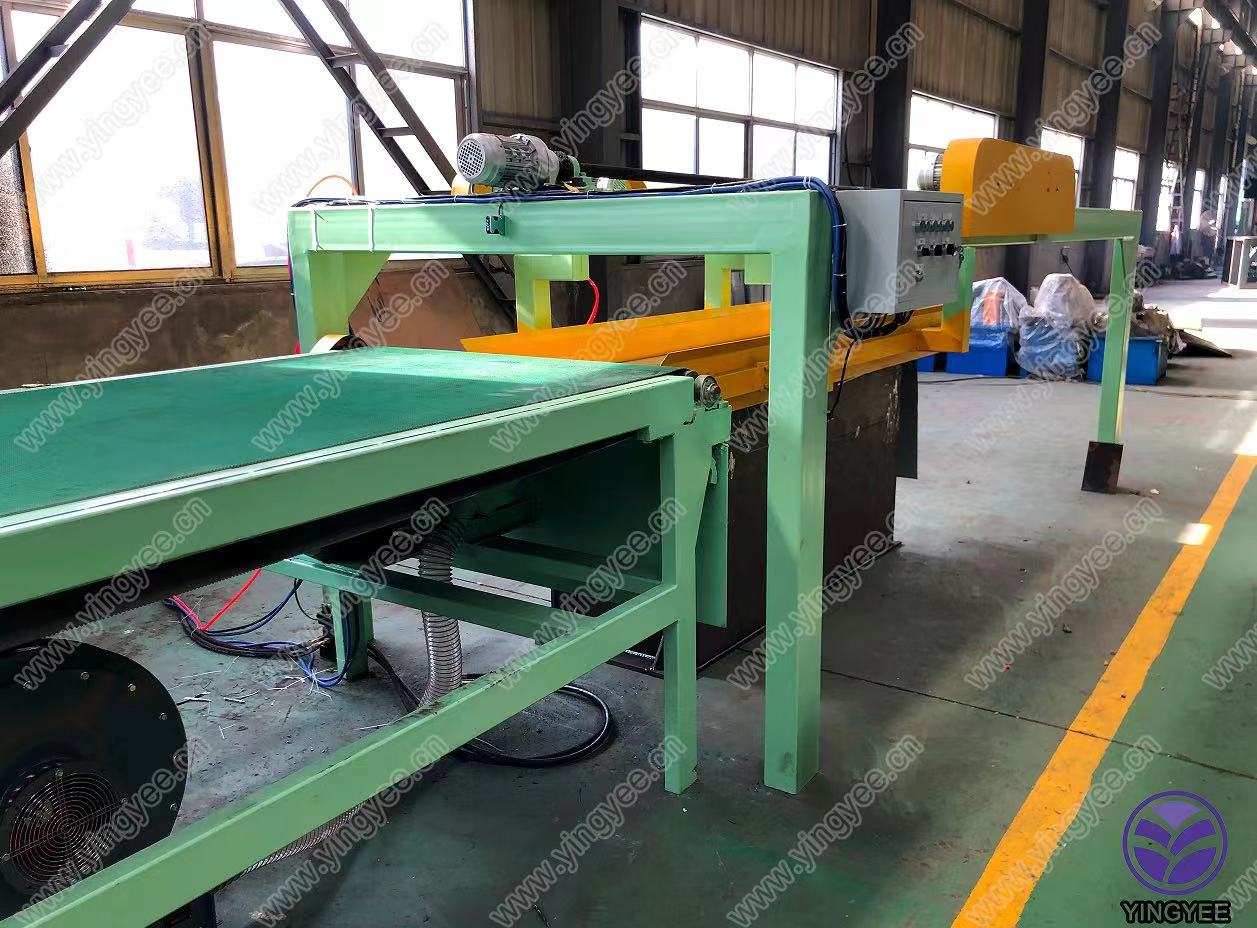
The experience of using a guardrail block cold bending machine demonstrates a significant improvement in production efficiency and cost-effectiveness. Operators benefit from intuitive machine interfaces and enhanced safety features, which reduce the risk of accidents during operation. This improvement not only enhances productivity but also fosters a safer workplace environment, aligning with contemporary occupational health and safety regulations.
guardrail block cold bending machine
Through real-world applications, companies have reported substantial reductions in material waste and operational downtime. The precision of cold bending extends the utility of raw materials, contributing to resource sustainability and cost savings. Furthermore, the quick adaptability of these machines to different guardrail profiles and dimensions eliminates the need for multiple specialized units, thus optimizing the manufacturing process.
Industry experts advocate for the use of cold bending technology due to its authoritative impact on the overall quality and reliability of guardrail systems. The seamless, smooth finishes achieved due to precise cold bending reduce stress concentrations in the metal, which are typical weaknesses in traditionally bent guardrails. This minimizes potential points of failure, thereby enhancing the structural reliability of safety barriers used along roadways.
Trust in the capabilities of guardrail block cold bending machines is further reinforced by their widespread adoption in global infrastructure projects. Leading manufacturers continue to innovate, incorporating state-of-the-art materials and processes that adhere to international environmental and safety standards. By ensuring each machine produced optimally aligns with both industry expectations and ecological considerations, manufacturers cement their status as trustworthy leaders in the field.
In conclusion, the evolution of guardrail block cold bending machines underscores the synergy between technological advancement and infrastructural safety. They epitomize a convergence of engineering expertise and industry demand, providing a compelling solution for modern guardrail production. This translates into safer roads, reduced production costs, and invaluable contributions to sustainable construction practices, keeping both manufacturers and end-users at the forefront of efficiency and reliability.