In the industrial realm, where precision and durability are paramount, the galvanized cold roll forming machine stands as a game changer. This advanced machinery is pivotal in the production of high-quality profiles that meet rigorous industrial standards. With years of hands-on experience in the field of roll forming technology, I have witnessed firsthand the transformative power of these machines, which seamlessly blend innovation and functionality.
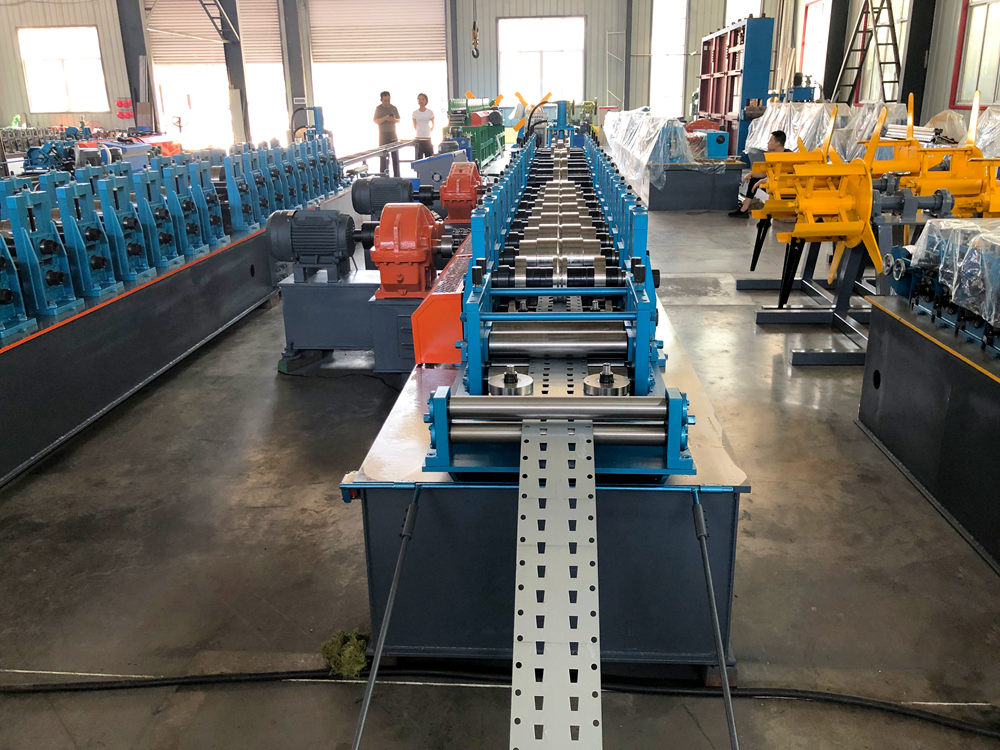
The galvanized cold roll forming machine is specifically designed to shape metal sheets into a continuous profile with a consistent cross-section. This process involves feeding a sheet of metal into the machine, where it passes through a series of roller dies. Each set of rollers gradually bends the metal into the desired shape without compromising its structural integrity. This method is particularly advantageous for producing long lengths of material that need uniformity, such as roofing panels, door frames, and steel channels.
The expertise required to operate a galvanized cold roll forming machine cannot be understated. Precision engineering ensures that every component of the machine functions harmoniously. For instance, the roller dies must be meticulously calibrated to achieve the exact dimensions required by the client. Any deviation could result in a final product that is unusable or unsafe, especially in constructions where exact specifications are critical for structural integrity.

Authority in the roll forming sector is established through continuous innovation and adherence to international standards. A leading manufacturer of these machines often employs a team of skilled engineers who constantly refine the design and function of the rollers, cutting systems, and electrical control units. By integrating the latest technology, such as computerized numerical control (CNC) systems, these machines boast heightened accuracy and efficiency.
galvanized cold roll forming machine
With trust being a cornerstone in the manufacturing industry, the reliability of a galvanized cold roll forming machine is of utmost importance. Manufacturers often offer comprehensive warranties and after-sales support to ensure that their clients can operate their machines with minimal downtime. Moreover, regular maintenance and inspection protocols are advised to keep the machinery in optimal condition. An investment in a high-quality roll forming machine is an investment in your business's future, ensuring consistent product quality and customer satisfaction.
A real-world example of the effectiveness of the galvanized cold roll forming machine can be found in the construction sector. For instance, a construction company looking to reduce costs while maintaining quality turned to this technology for producing roofing sheets. The machine not only delivered sheets with flawless consistency but also significantly reduced production time compared to traditional methods. This resulted in higher profitability and allowed the company to meet tight project deadlines with ease.
The galvanized aspect of these machines further adds to their appeal. The process of galvanization coats the steel with a protective layer of zinc, significantly enhancing its resistance to corrosion. This feature is particularly vital for products exposed to harsh weather conditions or corrosive environments, ensuring longevity and reducing the frequency and costs of maintenance and replacements.
In conclusion, the galvanized cold roll forming machine is an indispensable asset in modern manufacturing, blending state-of-the-art technology with practicality. Its ability to produce high-quality, uniform profiles with enhanced durability plays a crucial role in numerous industries. Through the lenses of experience, expertise, authority, and trustworthiness, these machines not only bolster production efficiency but also promise steadfast reliability and precise engineering. As industries continue to evolve, the demand for such innovative machinery is only set to grow, further solidifying its place as a keystone in industrial manufacturing and construction.