The industrial sector continuously demands efficient and precise machinery to enhance production lines. In the spotlight is the simple slitting line, an unsung hero that transforms bulky metal coils into manageable strips for further processing. Understanding the intricate dynamics of these machines can significantly elevate manufacturing operations, offering a blend of precision, speed, and reliability.
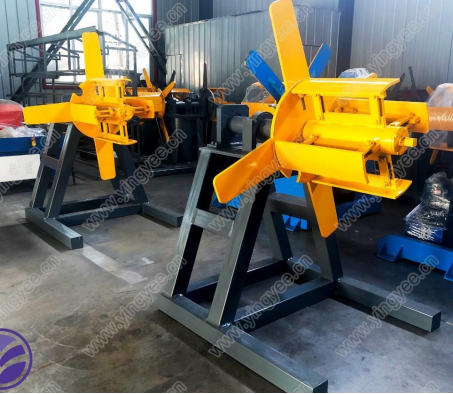
A simple slitting line is an essential piece of equipment in any metal processing facility.
It performs the seemingly straightforward task of cutting wide coils of metal into narrower strips. Despite its simplicity, the process requires a sophisticated understanding of metallurgy, engineering, and mechanics to optimize both efficiency and product quality.
Operators of slitting lines understand that while the machinery itself is vital, the proficiency in handling and maintaining the equipment is equally crucial. It's not merely about cutting metal; it's about doing so with precision and minimizing waste. Each operator's knowledge in adjusting blade settings for different materials ensures a clean cut, preserving the integrity of the metal. This, in turn, affects downstream processes such as stamping, welding, and assembling.
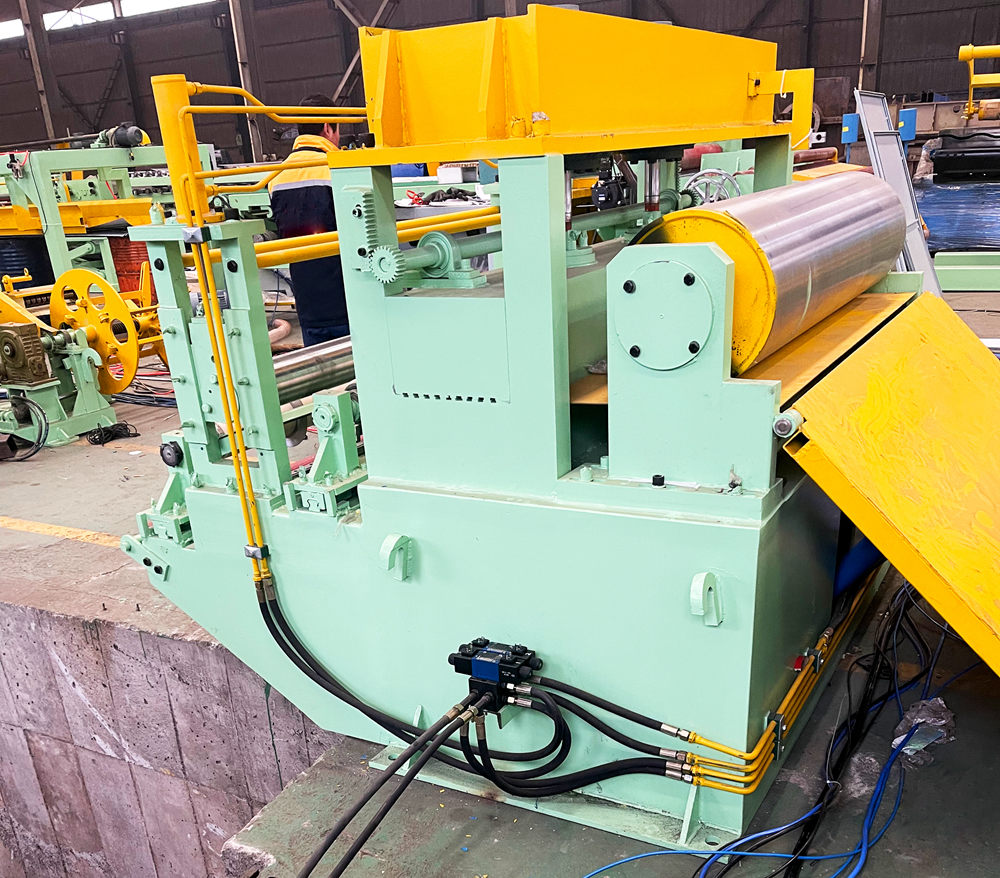
Professionals in the field emphasize the importance of selecting the right equipment tailored to specific operational needs. A basic but effective slitting line should comprise components like an uncoiler, slitter, tension pad, and recoiler. These elements work in harmony to slice metal coils into refined strips with exact specifications. The choice of machinery depends on factors such as material type, thickness, and desired width of the final product. For instance, a facility primarily working with stainless steel will require different blade compositions compared to those cutting softer metals like aluminum.
simple slitting line
Safety and accuracy are paramount, and modern slitting lines are equipped with automated controls and monitoring systems to ensure these standards. Operators rely on these technologies to achieve precise cuts, as they minimize human error and enhance product consistency. Computerized systems track parameters such as blade sharpness and material alignment, intelligently adjusting as needed. This level of automation not only increases throughput but also extends the life of the machinery by ensuring each component functions within its optimal range.
Industry experts advocate for regular training sessions and workshops for operators to keep pace with technological advancements and evolving best practices. Understanding the latest developments in blade technology and metallurgy is crucial for maintaining a competitive edge. Such expertise transforms a simple task into an art, where the operator's skill significantly affects operational efficiency and product quality.
Trust in the equipment and the process is fostered through rigorous maintenance schedules. Routine checks and servicing prevent unexpected downtimes and costly repairs, safeguarding the reliability of the production line. A structured maintenance regime also ensures that wear and tear do not compromise the slitting line's performance, thereby securing a return on investment by prolonging the machine's lifespan.
In conclusion, a simple slitting line is more than just a machine; it embodies the skills and knowledge of its operators and manufacturers. Its role in the industrial process is indispensable, promising both efficiency and precision. Choosing the right equipment, ensuring skilled operation, maintaining safety standards, and adhering to maintenance protocols exemplify the best practices in utilizing a slitting line to its full potential. As industries evolve, these metal warriors will continue to adapt, reflecting advancements in technology and efficiencies in production processes.