In recent years, the demand for sandwich panels in Russia has seen a notable increase, as developers and manufacturers recognize their efficiency, durability, and cost-effectiveness.
A crucial component in meeting this burgeoning demand is the sandwich panel production line. This sophisticated assembly of machinery allows for the streamlined production of high-quality panels used in a wide range of applications, from construction to refrigeration. Understanding the intricacies of a sandwich panel production line is critical for businesses seeking to optimize their manufacturing processes and elevate their market offerings.
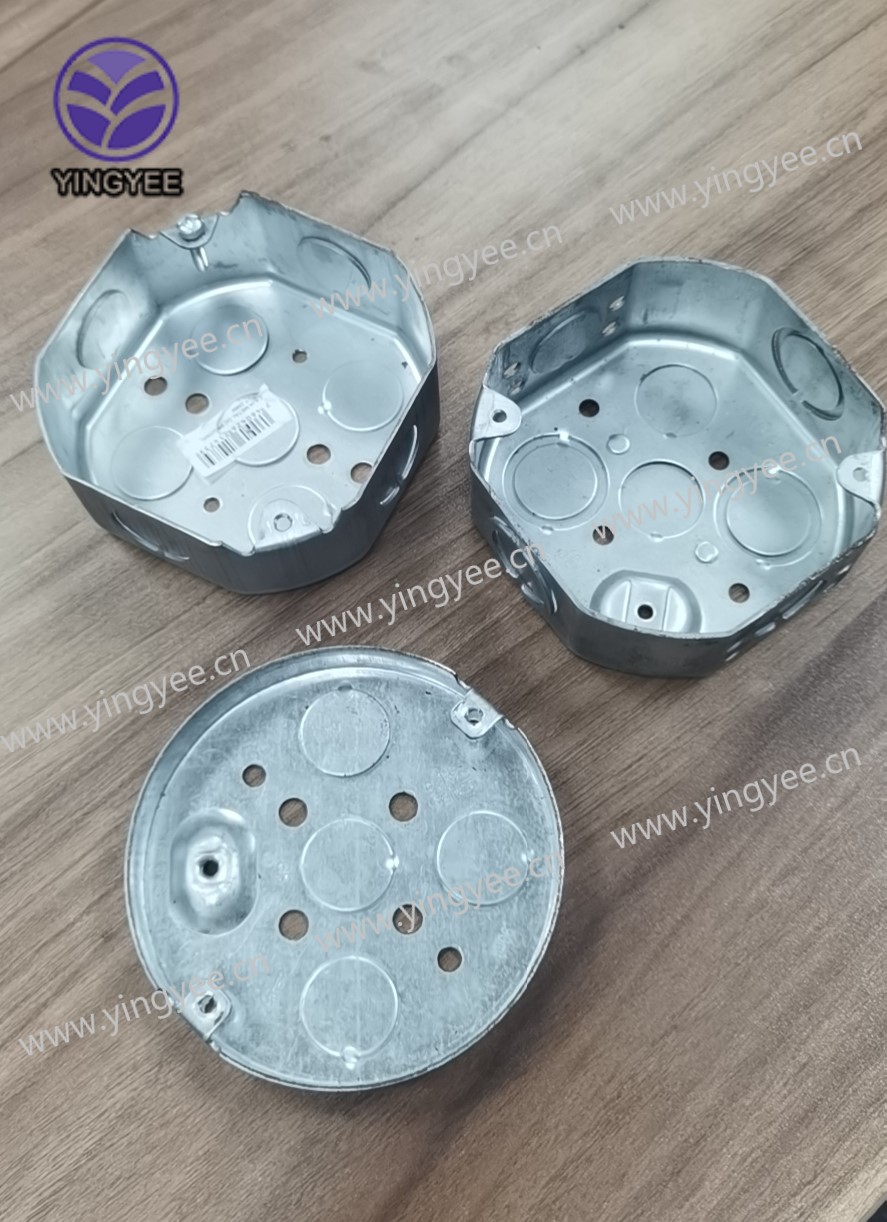
A fundamental aspect of sandwich panel production is the layer configuration, typically consisting of two metal sheets encapsulating an insulating core, such as polyurethane, mineral wool, or expanded polystyrene. This combination not only provides excellent thermal insulation but also enhances structural integrity. The precise engineering required to manufacture these panels necessitates advanced production lines.
Key features of a Russian sandwich panel production line include unwinding machines, forming machines, insulating core injectors, and cutting systems. Each component plays a pivotal role in ensuring the seamless creation of consistently high-quality panels. The unwinding machine feeds metal coils into the line, setting the stage for the forming machine, which shapes the metal sheets into the desired profiles. These profiles can be tailored to meet specific structural or aesthetic requirements, offering versatility in product design.
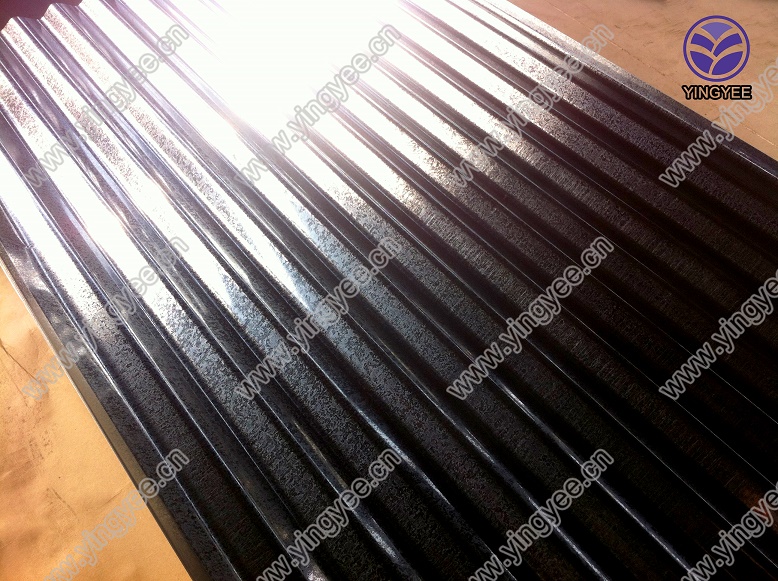
The heart of the production line lies in the insulating core injector. This component injects the chosen insulation material between the metal sheets. The injection process determines the thermal efficiency and durability of the resulting panels, making precision an absolute necessity. In Russia, where climatic extremes demand robust insulation, the choice of core material and its accurate application is of paramount importance.
Equally crucial is the cutting system, which slices the continuously produced sandwich panels into standardized lengths that meet industry specifications. This customization ensures the panels fit precisely into their intended applications without additional modification, thereby enhancing installation efficiency and reducing waste.
russia sandwich panel production line
Investing in a sandwich panel production line represents a significant commitment, underscoring the need for precise planning and understanding of market demands. For manufacturers in Russia, partnering with established machinery suppliers can provide a competitive edge. Such collaborations offer not only the latest in production technology but also the expertise required to adapt to ever-evolving market dynamics.
Moreover, given the rigorous standards applied to construction and building materials in Russia, maintaining compliance through meticulous quality control measures is essential. Production lines equipped with advanced monitoring systems can detect deviations in real-time, ensuring that each panel meets the stringent safety and performance criteria required by Russian regulations.
The economic benefits of operating an efficient sandwich panel production line cannot be overstated. Reduced operational costs, minimized waste, and superior product quality contribute to enhanced profit margins. Furthermore, the ability to rapidly adjust production parameters to cater to specific customer needs fosters innovation and strengthens market positioning.
In conclusion, mastering the technology and operations of a sandwich panel production line is crucial for Russian manufacturers aiming to capitalize on the growing demand for these versatile building components. Through strategic investments, collaborations with technology partners, and a steadfast commitment to quality, manufacturers can not only meet domestic needs but also position themselves as formidable players on the global stage. By leveraging local expertise and aligning with international best practices, Russia can continue to enhance its reputation as a leading producer of high-quality sandwich panels.