Understanding the significance of the AASHTO M180 cold bending machine in guardrail manufacturing is crucial for professionals involved in highway infrastructure. With decades of evolution in road safety measures, the demand for robust guardrail systems has intensified. The AASHTO M180 standard serves as the cornerstone in evaluating the quality and effectiveness of these guardrails, ensuring that they withstand the harshest of conditions. Here's why investing in an AASHTO M180 cold bending machine can elevate your production standards to meet these critical safety requirements.
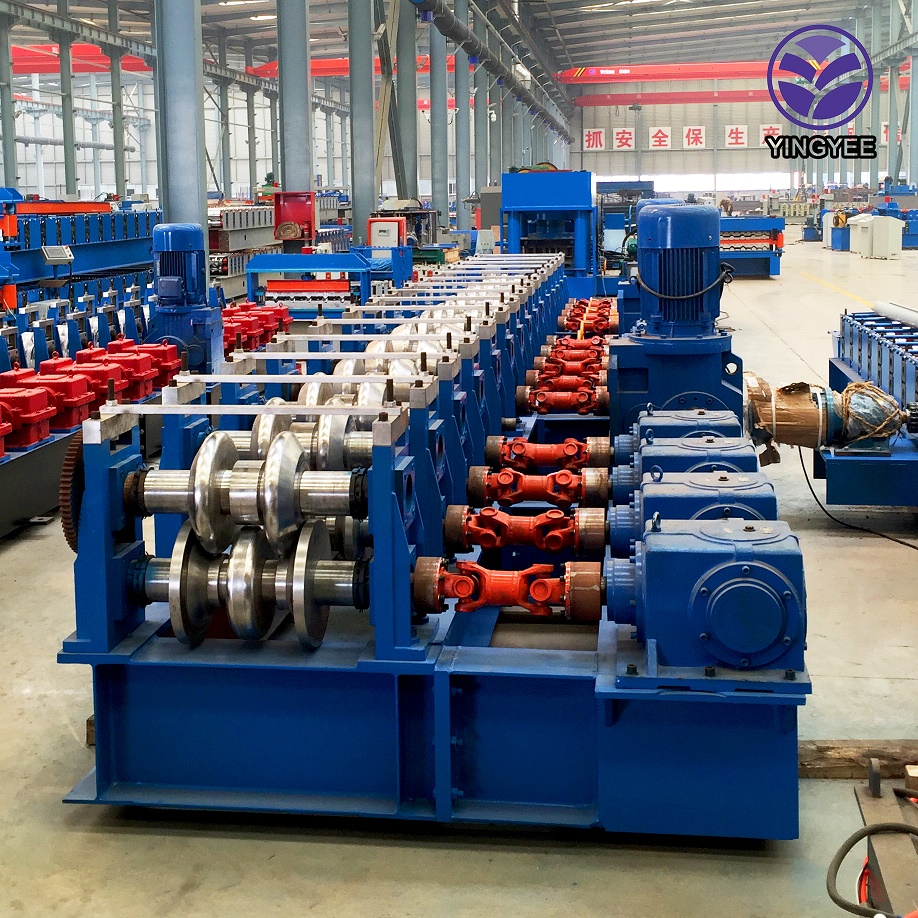
A cold bending machine adhering to the AASHTO M180 specifications promises precise curvature essential for the structural integrity of highway guardrails. The significance of consistency in bending cannot be overstated; it impacts the guardrail’s ability to absorb kinetic energy during vehicular impacts, thus minimizing potential damage or injury. When a machine crafts with precision, it elevates the end product's reliability, thereby aligning with the stringent guidelines outlined by the American Association of State Highway and Transportation Officials (AASHTO).
AASHTO M180 sets forth specific requirements for materials, zinc coating, and mechanical properties. Cold bending machines designed to these standards ensure that the guardrails maintain uniformity in these critical aspects, especially during high-speed fabrication processes. Implementing these machines can, therefore, assure buyers and regulatory bodies of adherence to safety norms, propelling an organization’s reputation as a reliable manufacturer in the infrastructure industry.
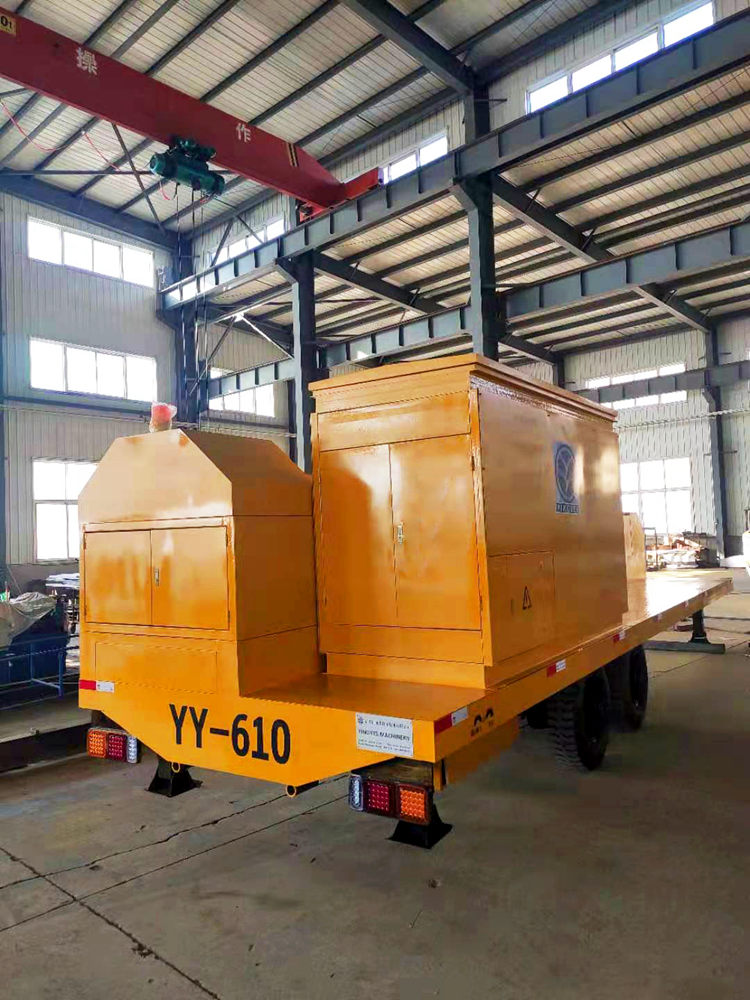
From an operational standpoint,
owning an AASHTO M180 compliant bending machine provides unmatched efficiency. The integration of modern technologies in these machines allows for automation in bending processes, reducing manual intervention, and thereby minimizing human error. This automation manifests in faster production cycles without compromising on quality, a critical aspect when fulfilling high-volume orders under tight deadlines.
Furthermore, the technological advancements embedded in modern cold bending machines facilitate adaptive control systems capable of adjusting parameters in real time. Such flexibility ensures that adjustments can be made on-the-fly to accommodate different specifications, which is particularly valuable in bespoke projects or when responding to unique contract requirements within short turnaround times. Having this capability ingrained within the manufacturing process ensures not only product excellence but also a competitive edge in the dynamic infrastructure sector.
aashto m180 cold bending machine
From a sustainability perspective, the use of an AASHTO M180 cold bending machine supports eco-friendly practices by encouraging efficient material utilization and reducing waste. The precise bending capabilities inherent in these machines limit excess trimming and ensure optimal use of raw materials. This sustainable approach not only minimizes environmental impact but also translates into cost savings on materials, reinforcing the economic viability of adopting these machines into manufacturing processes.
In terms of maintenance, machines crafted to comply with AASHTO standards offer longevity and reduced downtime. With features like robust build quality, self-diagnostic systems, and easy-to-replace components, manufacturers can expect reduced operational interruptions. Regular upkeep as recommended by the manufacturer ensures continuous performance, thereby maintaining the integrity of the guardrails without interruptions caused by machine failure.
The decision to invest in an AASHTO M180 compliant cold bending machine reflects a commitment to quality, safety, and industry expertise. For companies aiming to establish themselves as forerunners in the infrastructure manufacturing sector, aligning with these standards not only affirms their expertise but also extends trustworthiness among stakeholders including contractors, government agencies, and the general public.
Navigating the competitive landscape of guardrail production demands an authoritative approach to manufacturing processes. By utilizing machines designed to AASHTO M180 standards, businesses position themselves as leaders capable of producing reliable and safety-compliant highway solutions. This strategic alignment with industry standards lays the groundwork for building a trusted brand known for innovation, quality, and commitment to safety.