Pipe thread rolling machines are remarkable assets in the manufacturing and construction industries, streamlining the creation of precise threads on pipes used in various applications. These machines are critical for operations that demand high levels of precision and durability, such as in petrochemical, plumbing, and HVAC systems. For industry professionals seeking to optimize their production lines,
understanding the nuances and capabilities of these machines is paramount.
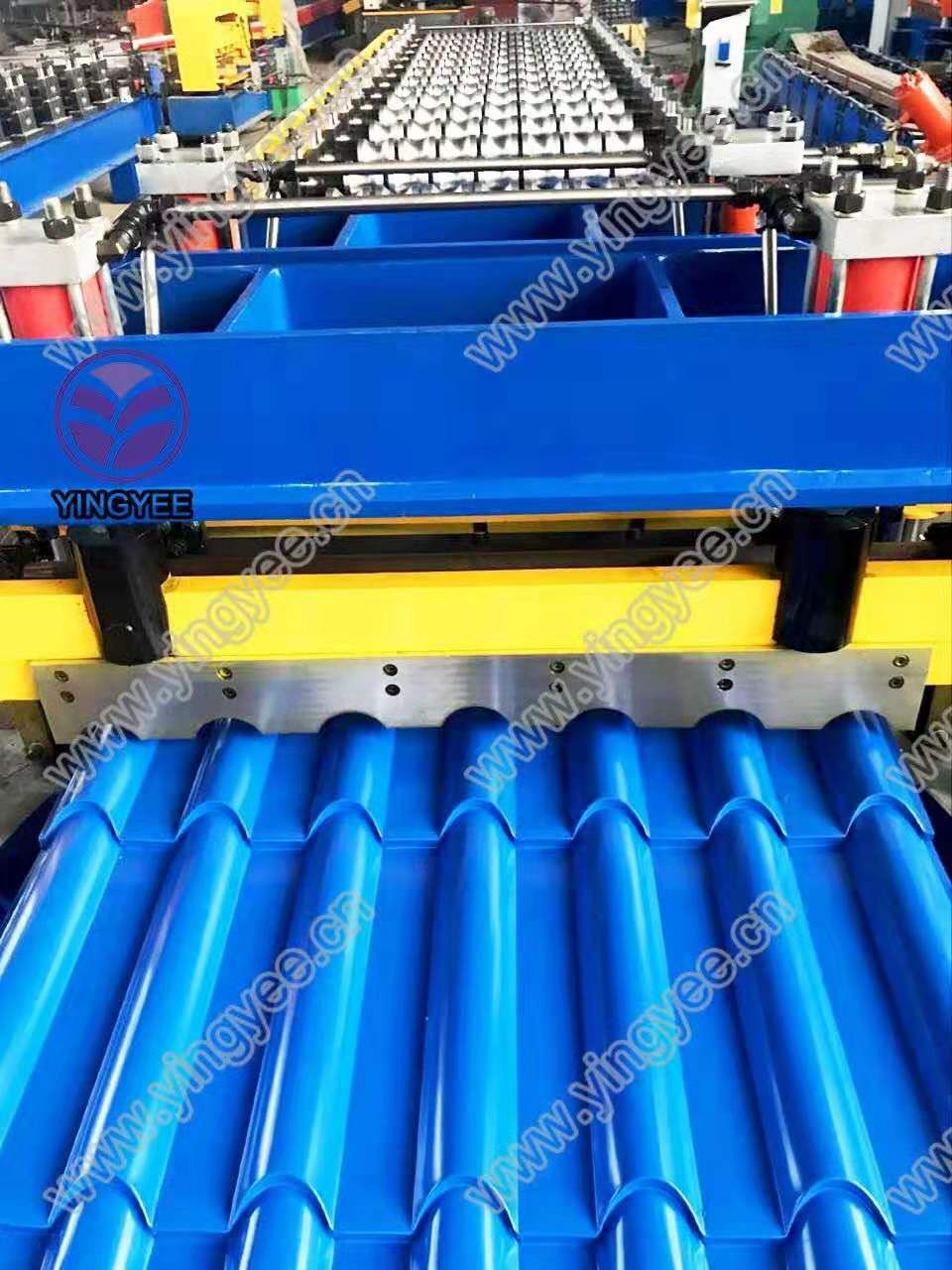
The primary advantage of utilizing a pipe thread rolling machine lies in its ability to produce consistent and robust threads without compromising the integrity of the pipe. Unlike traditional threading methods that may induce micro-cracks or other stress-induced weaknesses, thread rolling inherently strengthens the material. This process involves cold-forming the metal, which improves its tensile strength and fatigue resistance, crucial for applications where pipe failure is not an option.
To fully appreciate the value offered by pipe thread rolling machines, it's important to delve into how they operate. These machines employ a series of hardened dies that engrave the pipe's surface as it rotates. The pressure exerted by the dies is meticulously calibrated to ensure that the threads meet exact specifications, thus guaranteeing compatibility with corresponding fittings and connectors. This process not only enhances the mechanical properties of the pipe but also yields a thread profile with superior surface finish quality, reducing the likelihood of leaks.
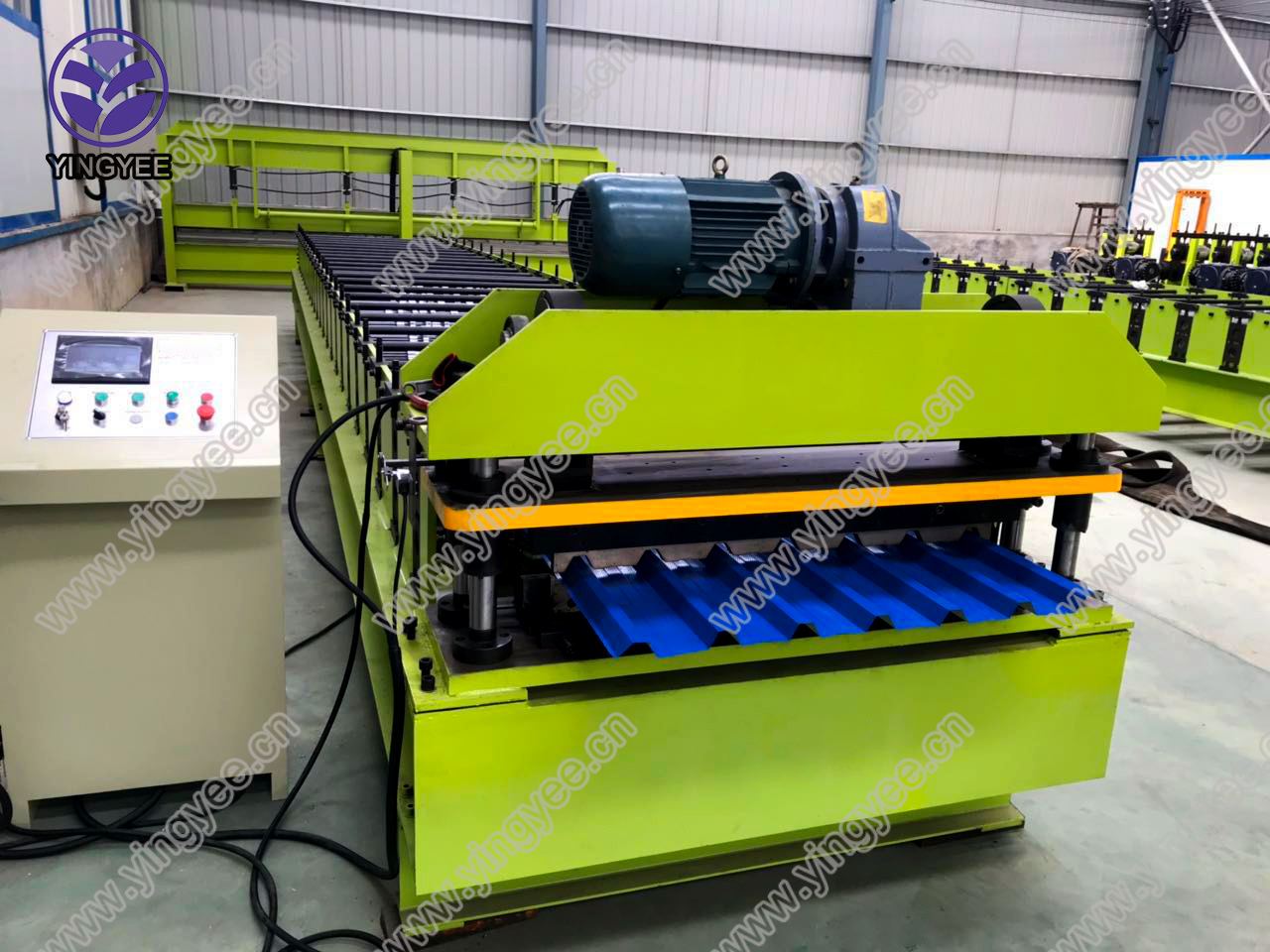
From a practical standpoint, pipe thread rolling machines offer unparalleled efficiency in high-volume production environments. They significantly reduce the time required to complete threading tasks compared to manual methods, slashing labor costs and minimizing human error. Additionally, the machines' automation capabilities allow for continuous operation with minimal supervision, further optimizing operational productivity.
pipe thread rolling machine
Expertise in operating these machines is another critical factor that underscores their effectiveness. Skilled technicians are essential in setting up and maintaining the equipment to ensure optimal performance. Regular calibration and maintenance checks prevent unwanted downtimes and prolong the machine's lifespan. The insights gained from experienced operators can inform further enhancements in the threading process, allowing for the development of innovative solutions uniquely suited to diverse industry challenges.
The authoritativeness of pipe thread rolling machines is reflected in their widespread adoption across industries that demand superior thread quality. Leading manufacturers who utilize these machines often set industry benchmarks, influencing standards and best practices globally. Their reliance on these machines is a testament to the technology's reliability and the tangible benefits it provides to end-users.
Trustworthiness in thread rolling technology is underscored by rigorous testing and certification processes that ensure each machine meets stringent industry standards. Manufacturers and users alike prioritize quality control, ensuring that the threads produced can withstand the operational demands they will encounter. Providing thorough documentation and transparency about machine capabilities and limitations further builds trust, reassuring users of the product's integrity.
In conclusion, pipe thread rolling machines represent a fusion of engineering excellence and practical application. Their precision, efficiency, and reliability make them indispensable in modern industrial applications. By capitalizing on their capabilities, businesses not only enhance their operational output but also ensure the structural integrity of their products, thereby safeguarding their reputation and customer trust. For those navigating the competitive landscape of manufacturing and construction, mastering the use of pipe thread rolling machines is not just an advantage—it's a necessity.